Pioneering Quantum Computing for Metalworking
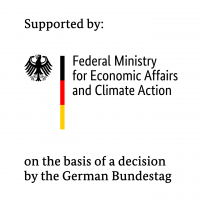
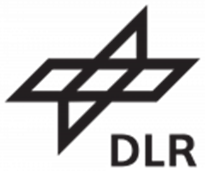
The project “QUASIM – QC-Enhanced Service Ecosystem for Simulation in Manufacturing” is founded by the Federal Ministry of Economic Affairs and Climate Action (BMWK) and the German Aerospace Center (DLR) under the project no.: 01MQ22001D.
Details
The project QUASIM unites quantum computing and metalworking. Since metalworking is the biggest industrial sector in the European Union with millions of jobs depending on it, it is vital that the industry remains stable and open to transformation. Contrary to the ubiquity of metalworking, quantum computing has not been researched outside of theoretical applications. In QUASIM, metalworking and quantum computing are brought together to optimize industrial practice and finally apply quantum computing outside of academia.
Involving thousands of companies, which employ about 3.7 million people, metalworking is the biggest industrial sector in the European Union. Since metalworking is so important, digital twins have been developed to ensure the highest product quality of the most common metal process, machining. Digital twins are virtual representations of physical objects that allow to control and optimize machining processes by gathering and re-feeding data, for example about material properties and machining parameters. However, despite the significance and size of the metalworking industry and the specific process of machining, both are faced with several limitations.
While machining could be optimized with virtual representations, industrial applications often exclude simulations such as digital twins because of their high computing requirements and the expert knowledge necessary. This exclusion largely affects small and medium sized businesses due to their restricted economic capacities. The ensuing consequence is that physical effects of industrial practice are either completely neglected or only approached by rough estimations. Exclusion and neglect further cause significant disadvantages, particularly for smaller businesses.
Very far from these industrial practices and from any application, quantum computing (QC) so far has been only applied to theoretical problems to evaluate the basic principles of the technology. But if quantum computing is practically feasible, it will override the limits of current computing applications. This includes the limits of metalworking caused by the current low use of digital twins in machining.
Once metalworking and quantum computing are brought together, enormous advantages for both sectors become clear. Data from real production environments such as machining has not been transferred to quantum computing, so that the usefulness of quantum technology is not practically visible as of now. The relation of quantum computing based machine learning, the effects on production processes, and the resulting product quality also remain to be investigated. Quantum computing based machine learning could not only make digital twins more accessible but could surpass the utility of virtual representations with quantum based algorithms.
This is why the project QUASIM gauges opportunities for growth of the metalworking industry with the implementation of quantum computing. QUASIM is an acronym for the complete project title “Quantum Computing Enhanced Service Ecosystem for Simulation in Manufacturing”. As the title suggests, the aim of the project is to develop and test algorithms of quantum computing for manufacturing simulations. The guiding question for the development is if and how simulation of machining processes can be optimized and accelerated by quantum computing. Methodologically, the project is embedded into the industry 4.0 as “Quantum-as-a-Service” (QaaS), pursuing a practically oriented knowledge transfer from production simulation to quantum computing.
The basis of the project is the connection of quantum computing and numerical models: a promising application of quantum computing for the simulation of machining processes is the Hessam-Harrow-Lloyd (HHL) algorithm within a finite element method (FEM). The HHL algorithm has not yet been introduced to mechanical engineering because interdisciplinary teams and specific case studies are lacking – a gap that QUASIM aims to resolve. In an additional step, quantum computing and machine learning (ML) models are connected because combinations of quantum hardware and data-driven methods derived from artificial intelligence or data science might be able to replace numeric methods such as the finite element method in the long-term.
The connected approaches of quantum computing, numerical models and machine learning resulting from the project will be compared to the standard of the industry: semiconductor computers with use of the finite element method. Lastly, the resulting QC Numeric and QC ML-based services will be integrated into the existing digital twin framework. Both open possibilities for the existing digital infrastructures and enable the usage of quantum computing in industrial contexts.
Examples for possible improvements are machining processes of BLISKS and the metal sheet removal during laser cutting. Blade Integrated Disks (BLISK) are turbomachine components that are time-consuming and costly in machining. Yet, time and cost of BLISK productions could be lowered by means of quantum computing simulations which optimize the production process. Another problem in machining is the laser cutting process because withdrawal processes of cut metal sheets run often far from optimal. This is because existing models of the withdrawal process do not factor in the heat impact of the lasers and ensuing thermal expansion of the sheets. These incomplete models regularly cause machine downtimes and require human intervention. This is not only uneconomical, but also undesirable from an automation perspective. Quantum computing algorithms of the metal sheet removal could model the heat impact and predict the optimal removal conditions. This would eliminate downtimes of the machine and the need for human intervention. Additionally, the quality of both BLISK productions and laser cuts could be significantly increased.
More than practical applications, the project illustrates how quantum computing can be implemented to recognize and ensure competitive advantages in the mid- and long-term. This is where ModuleWorks plays a key role in the project. As a provider of system applications and software developer, ModuleWorks can contribute as the intersection of data sources and the development of software modules for industrial applications. This especially includes addressing small and intermediate sized businesses around the globe by enabling them to access quantum technology. In this way, ModuleWorks does more than to tap into the market potential of quantum computing – it expands the possibilities for third party providers to engage with new digital environments.
Before quantum computing becomes feasible on larger scales, possibilities and advantages for metalworking are tested out in QUASIM. This allows to research potentials of implementing quantum computing for small and medium sized businesses. ModuleWorks and the project partners are uniting their knowledge and efforts to pioneer quantum computing for metalworking, especially addressing smaller businesses.