Despite the increasingly widespread use of additive manufacturing technology, the full potential of additive systems remains untapped. Many parts are produced using only 3-axes, even though robots and systems with linear or parallel kinematics are capable of more complex movements. These systems can also handle automatic tool changes between DED, pellet FDM and mechanical processing, making them available for hybrid manufacturing.
In addition, plant engineers and system integrators invest a lot of time and resources in developing and continuously refining their hardware solutions and technology. But after hand-over to the customer, the vast array of sophisticated features and options brings a steep learning curve and the systems do not immediately deliver the long-awaited 3D printed components at the push of a button.
To unlock the potential of the latest manufacturing systems, 1A Technologies teamed up with ModuleWorks to develop a push-button solution for manufacturing and repairing components with both additive and subtractive processes for all kinematics and different types of technology. The new solution is available in the HY5CAM software from 1A Technologies.
How It Started – The Mobile Smart Factory
The collaboration started on a customer project with Bionic Production GmbH, a company that offers an on-site Mobile Smart Factory in a container. With the mobile factory, components are manufactured at the customer’s site or on the way there (by ship or train) regardless of the environmental conditions, using only an external power connection of 63 amps. The mobile factory uses Wire Arc Additive Manufacturing (WAAM) processes and wire DED as well as automatic tool changes, for example switching to a measuring probe or milling tool, for intermediate and final machining of diverse components.
Offshore, On-Demand Manufacturing
One of the main applications of the Mobile Smart Factory is the rapid delivery of components in small quantities on demand. A good example is the housing of a windshield wiper motor on an ocean-going vessel belonging to the Bernhard Schulte shipping company. The corroded housing impaired the function of the wiper and needed to be replaced to guarantee safe continuation of the ship’s journey (Figure 1 and Figure 2).
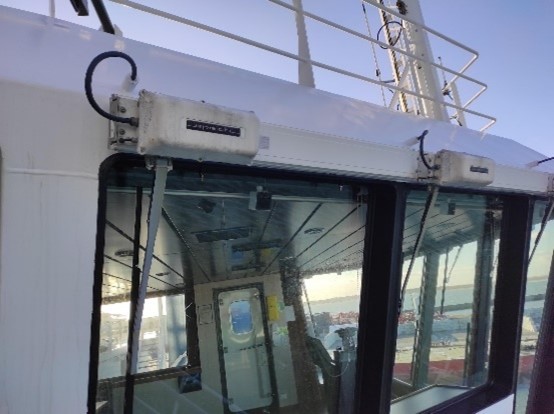
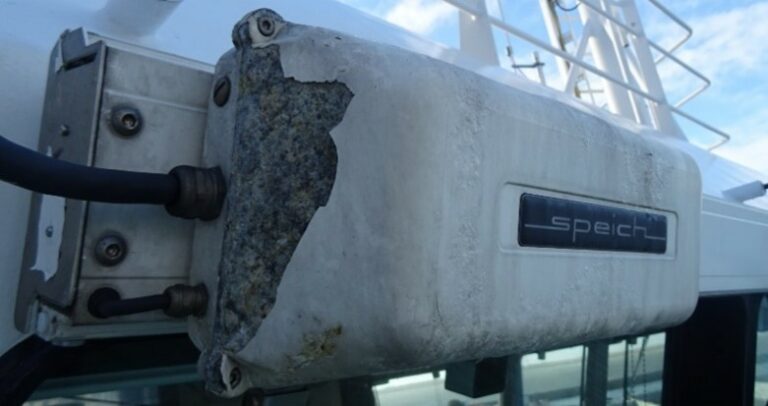
To guarantee availability of the parts and rapid repairs, Bernhard Schulte GmbH commissioned the manufacture of these parts in a mobile factory stationed on an offshore oil and gas platform. The factory is able to produce the motor housings on call as needed by the ships.
Scanning the Data
For spare parts production, complete CAD data is usually not available, but is instead stored in the form of drawings. To ensure effective data preparation and fast manufacturing, a CAD model of the component is created using the digitizing tool in the mobile smart factory and, if necessary, reworked on the defective areas and functional points (Figure 3).
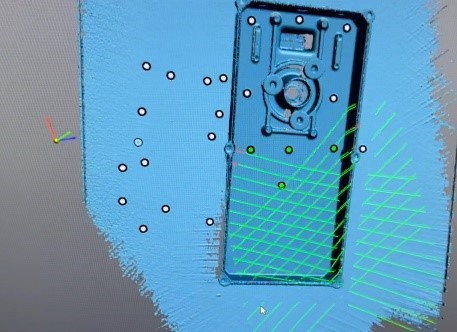
Automated Programming with HY5CAM
The digitized part is then programmed for both additive and subtractive manufacturing using HY5CAM. The system offers a large range of highly automated processes to assist inexperienced operators as well as complex algorithms adapted to the respective part for fast and intuitive path planning (Figure 4).
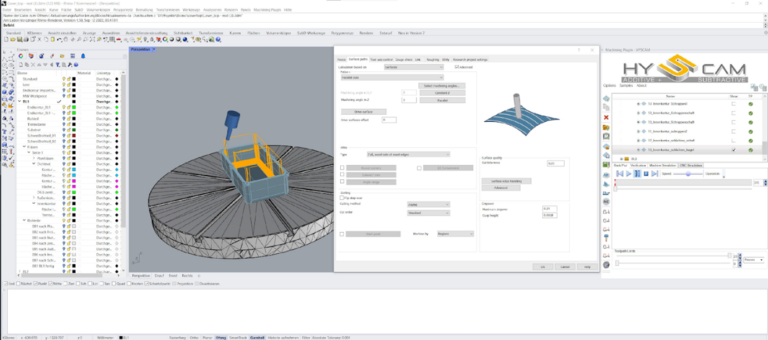
The toolpaths are then transformed according to the kinematics. Comprehensive collision analysis, from the machine to the tool and from the workpiece to the clamping device, ensures optimal accessibility to all processing positions. In this example, collision-free toolpaths were generated for the P700 hybrid parallel kinematic 6-axis machine tool from METROM Mechatronische Maschinen GmbH, which forms the heart of the mobile smart factory (Figure 5).
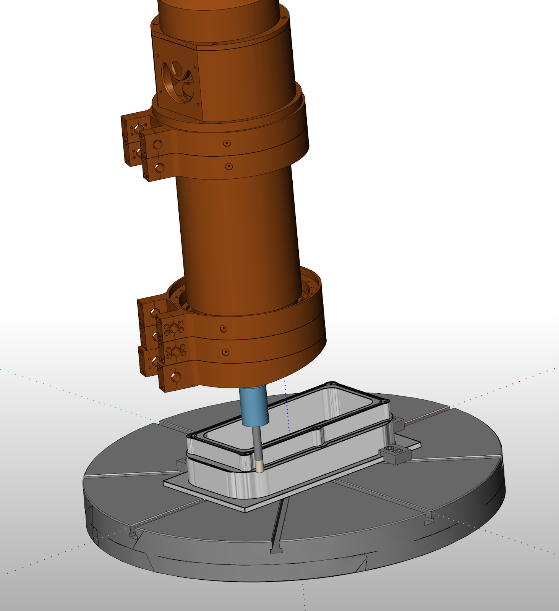
Manufacturing the Part
The motor housing is manufactured inside the mobile sea container using WAAM (Figure 6) with an automatic interlayer temperature control. This is selected in the post-processor and is implemented via the machine’s control functions.
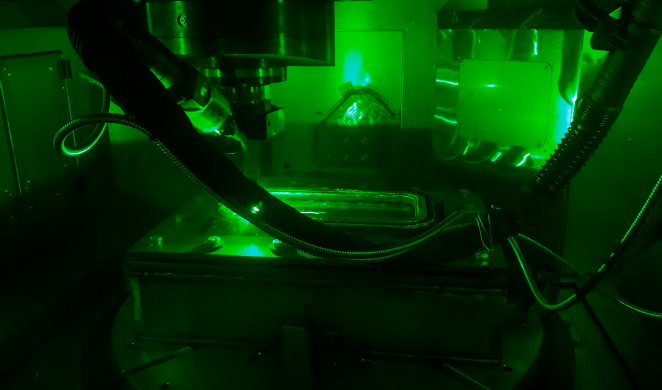
The part is then mechanically machined using the same system with various milling and drilling tools to finish the final contour.
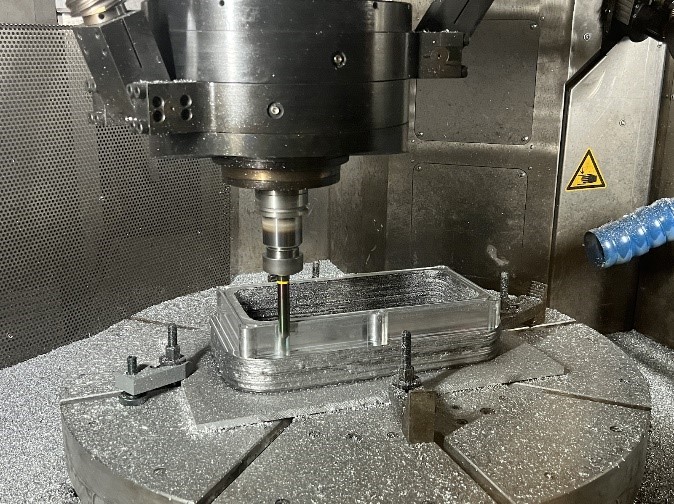
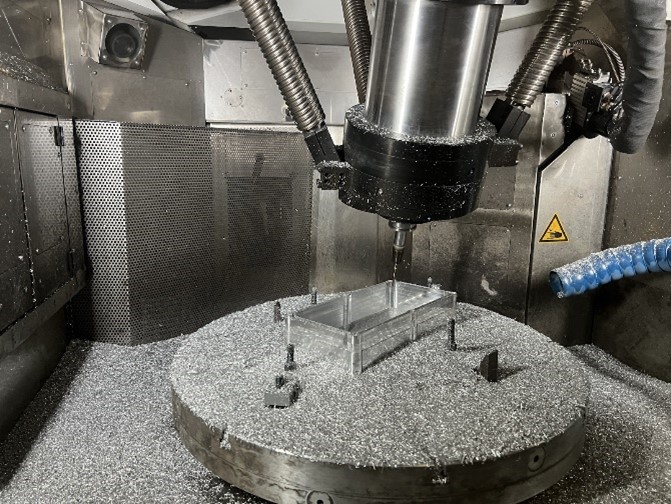
The result is a motor housing (Figure 9) which, thanks to the collaboration of all involved partners, was produced quickly and to the full satisfaction of the customer.
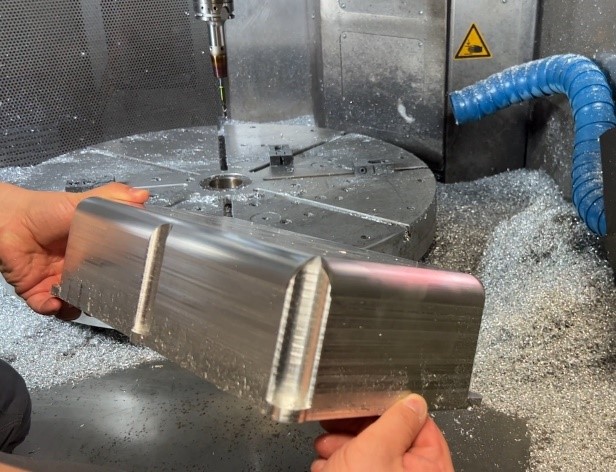
Outlook and Further Development
Usually, planning and producing the first part is more complex than repeating or optimizing the process because the process parameters (additive and subtractive) need to be determined and entered into the system. Once defined, the parameters are stored and reused as data sets, enabling identical spare parts to be reproduced even more efficiently, even in batches of one.
HY5CAM is also used in systems for DED-W using arcs or lasers as well as the Screw Extrusion Additive Manufacturing (SEAM) process for pellet FDM. The experience gained from the research and industrial environments is continuously fed into further development of the software.
About ModuleWorks
ModuleWorks is at the forefront of manufacturing software, playing a key role in enabling the efficient production of increasingly complex parts in an environmentally sustainable way. As a strategic partner to leading CAD/CAM vendors, CNC control makers, machine tool builders and cutting tool manufacturers, ModuleWorks develops software that powers solutions throughout the manufacturing industry which contributes to 16% of global GDP worth $16 trillion per year. Founded in 2003, ModuleWorks has grown to over 200 employees and already invested 1,700 person-years of software development in toolpath and simulation technologies that form the core of manufacturing processes. In the CAD/CAM area alone, ModuleWorks has a market share of 90%, enhancing the performance and quality of over 500,000 installed seats of CAD/CAM and CNC software worldwide. With a comprehensive portfolio of cutting-edge software components and the capacity to address emerging and niche technologies like AI, cloud, automation, additive, robotics and digital dentistry, ModuleWorks is committed to shaping the future of digital manufacturing with its partners, empowering the industry to Get There Faster.
About 1A Technologies
1A Technologies was founded in 2020 to make components for 3D printing industrially available. A main business area is the production and sale of the SEAM process patented at Fraunhofer IWU, which has now been adapted to 40 systems with different kinematics worldwide.