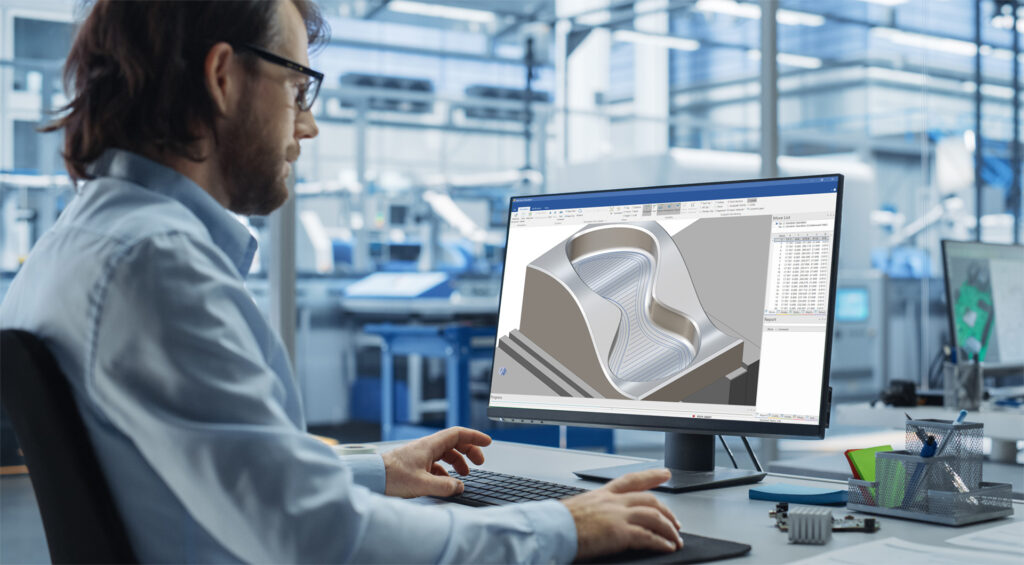
This release also includes additional features that improve the overall toolpath, simulation, and automation products offered by ModuleWorks.
Toolpath
Multi-Axis Roughing | Turn Milling
Axial and Radial Offsets for Turn Milling
Challenge: Different finishing strategies for floors and walls in a pocket typically require distinct parameters, particularly when setting individual offsets for each strategy. However, until now, users have been restricted to defining a single global offset.
Solution: With this new feature, users can either specify a single offset for all geometries using the ‘Global’ option, or use the ‘Axial and Radial’ option to define different values in each direction.
Benefits: This feature gives users more control and flexibility because they can now leave the necessary amount of offset material according to the specific finishing job, resulting in an overall better surface finish.
Multi-Axis Roughing | Turn Milling
Support for Fixtures/Chucks for Turn Milling
Challenge: The Turn Milling toolpath is designed for roughing external diameters, where the tool and holder are exposed to the fixture which increases the probability of collision.
Solution: Fixtures/Chucks can now be selected as a mesh/model. The selected mesh/model is spun and the resulting profile is used to avoid collisions.
Benefits: Support for fixtures and chucks enhances machining safety and empowers users to fully leverage the toolpath generation software. Additionally, it streamlines implementation for CAM partners.
Multi-Axis Roughing | Area Roughing
Primitives Definition as Clearance Area
Challenge: Currently, only User Surfaces can be designated as Clearance Areas. Users need to either create or select existing geometry to define these areas, as there is no option to choose from standard primitives.
Solution: Now, users will be able to construct virtual primitives like Plane, Cylinder, and Sphere while defining clearance area geometry.
Benefits: With the introduction of this feature, users can Define standard primitives for retracts. This improves the programming efficiency.
Multi-Axis Surface Finishing | Rotary Machining Finishing
Leads for Floor Finishing
Challenge: Currently, cylindrical or conical surfaces pattern for rotary finishing doesn’t allow the user to control the lead-in/lead-out. This can sometimes impact the surface finish of floor surfaces.
Solution: Now there is a provision to define lead-in/lead-out while generating toolpath with cylindrical and conical surfaces pattern.
Benefits: This features allows users to have greater control over the toolpath. It can also improve surface finish in some cases.
Multi-Axis Surface Finishing | Geodesic Machining
Multiple Boundary Passes
Challenge: When machining an area with walls, the tool bounces fast from wall to wall, stopping closely before the wall. Users could set an offset to the walls, but there was no option to finish the toolpath close to the borders with multiple passes – slowly approaching the wall.
Solution: Multi-boundary passes allow users to machine the border of an area as a final step and moreover, control the stepover for this operation.
Benefits: The boundary passes improve surface quality while making the operation much safer.
Special Parts | Multiblade
Feed Rate for Links in Multiblade
Challenge: Currently, it is difficult to optimize the non-cutting time as the feedrate on the links is not controllable. Although, it is often desirable during a non-cutting move to increase the feed rate to reduce machining time.
Solution: Now, It is now possible to customize the feed rates for links.
Benefits: This feature gives users greater control over machining processes while reducing overall cycle times.
2-Axis Machining
Start Point Options for 2D Chamfering
Challenge: Currently, toolpath start points are hard-coded to minimize linking distance. However, for some part geometries, this start point may not be ideal for machining conditions.
Solution: Users have the flexibility to set toolpath start points for each feature. They can choose to minimize link length, set a curve start point, define their own start points, or use the midpoint of the longest line.
Benefits: This feature improves machining conditions and enhances part quality.
Turning
"Follow tool angle" Option for Imported Tools
Challenge: Currently, when using mesh files for turning tool, it is difficult for the users to manage the toolpath on steeper areas.
Solution: ‘Follow tool angle’ is now supported for generating turning toolpath when using mesh file for a tool.
Benefits: With this enhancement, users will be able to turn steep profiles safely using mesh tools.
Turning
Safety Angle Clearance for Turning Toolpath
Challenge: During machining, the back of the turning tool holder might rub against the in-process stock.
Solution: Users can now apply a safety angle clearance between the tool and the in-process stock. This new feature is available for turning toolpaths that have been created with the ‘follow tool angle’ option.
Benefits: This feature enables users to generate safer toolpaths by avoiding areas where the backside of the tool could gouge the in-process stock.
Core Component Technologies | Convert
Enhanced Sorting Options for Rotate/Transform/Mirror
Challenge: Managing the links when rotating/mirroring/transforming a toolpath is difficult, resulting in longer linking times.
Solution: Two new sorting options have been added: ‘sort by passes’ and ‘sort by slices’.
Benefits: These new options enable users to reduce the linking time, which in turn reduces the overall machining time.
Simulation
Simulation SDK | Cutting Simulation
Asynchronous Rendering
Challenge: Rendering calls for highly complex in-process stock can be expensive, affecting the responsiveness of the CAM application.
Solution: Asynchronous rendering uses a separate thread to triangulate and render the in-process stock, independent of the simulation thread.
Benefits: This improvement accelerates simulation in play mode by eliminating wait times for in-process stock rendering.
Simulation Systems | NC Editor
Save In-Process Stock within Project File
Challenge: Currently, users cannot save multiple in-process stocks within a project file; they can only be saved on the hard drive. This makes it difficult to manage stock files along with project files.
Solution: This feature will allow users to save in-process stock directly within the project file.
Benefits: Stock file management is enhanced, allowing users to easily hide or display stock files with a simple mouse click, improving overall efficiency and accessibility.
Automation
Machine Environment | MultiXPost
Local Coordinate System for Machine Axis Definition
Challenge: With the 2023.04 release, MultiXPost began to support global transformations that impacted the entire kinematic chain of the workpiece and tool. Previously, these transformations, which were part of the kinematic description of the MachSim machine, were overlooked by MultiXPost, resulting in incorrect autodetection of the machine kinematics and, consequently, erroneous calculations of the machine axis values for the specified movements.
Solution: As a result of the existing change to MultiXPost, the X, Y, and Z values of the Directions, Vectors, and Base Points shown in the Machine Definition UI are now defined in a local coordinate system.
Benefits: The MultiXPost UI and documentation now provide a clear explanation of why the same machine kinematics are displayed differently in the MultiXPost UI compared to other machine definition interfaces, such as MachSim or Machine Builder, thereby enhancing user understanding.
Machine Environment | MultiXPost Robots
Support for Robot Axis Coupling
Challenge: Some robotic applications demand precision and repeatability, especially for high-payload robots. Axis-coupled robots offer advantages over traditional 6 DoF robots in these scenarios, enabling higher payload capacities. However, programming these robots is more complex because two of their joints are interdependent.
Solution: Our kinematics solver now supports robots with axis coupling.
Benefits: With axis coupling support, high-payload robots can now be used in applications that demand precision, speed, and repeatability, such as additive manufacturing and palletizing.