Next Generation Shop Floor Programming (NGSP)
Revolutionize On-Machine CNC Programming using Next Generation Shop Floor Programming
Challenges Faced by Manufacturers
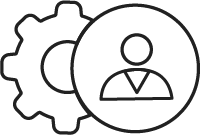
Scarcity of Highly Experienced/Skilled CNC Programmers
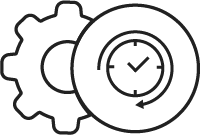
Longer Time for CNC Programming and Longer Machining/Cycle Time
The manufacturing industry is growing at a fast pace and the demand for experienced, skilled CNC programmers is rising due to the complexity of products to be manufactured and complexity of CNC machine tools. The learning curve for the new CNC programmers is very steep which results in longer programming cycle times and, hence, longer overall machining cycle times.
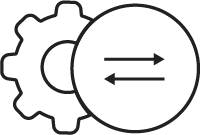
Inconsistency in Program Output and Quality
Depending upon the skill levels and professional experience of CNC programmers, they may follow different approaches to programming. In the absence of a structured step-by-step guided approach, this may result in inconsistent NC code output. This may lead to inconsistent quality of the parts produced.
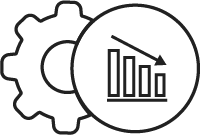
Higher Risk of Loss of Productivity
Solution Offered by ModuleWorks
It is our vision to help manufacturing companies to increase their throughput while maintaining full availability and optimum utilization of the machines by empowering skilled as well as new operators to be even more productive on the shop floor.
In line with our vision, we have developed Next Generation Shop Floor Programming (NGSP) to support machine tool builders and controller manufacturers to overcome the above-mentioned challenges. It is an innovative and highly automated embedded CNC programming solution for on-machine programming on the shop floor.
It empowers operators to program a large variety of prismatic parts easier, faster, safer, and in a cost-effective manner than before. This is especially helpful in a high mix, low volume type manufacturing environment.
Key Features of NGSP
Touch-Based Feature Detection
Automatic Selection of Tool and Cutting Parameters
Based on the geometry of the feature and type of machining operation, NGSP proposes the most suitable available tool for the operation. If connected to a tool database, the correct cutting parameters are automatically selected based on the tool grade and the stock material.
Support for Variety of Machining Capabilities
Major Benefits of NGSP
Reduced Programming Time and Reduced Machining/Cycle Time
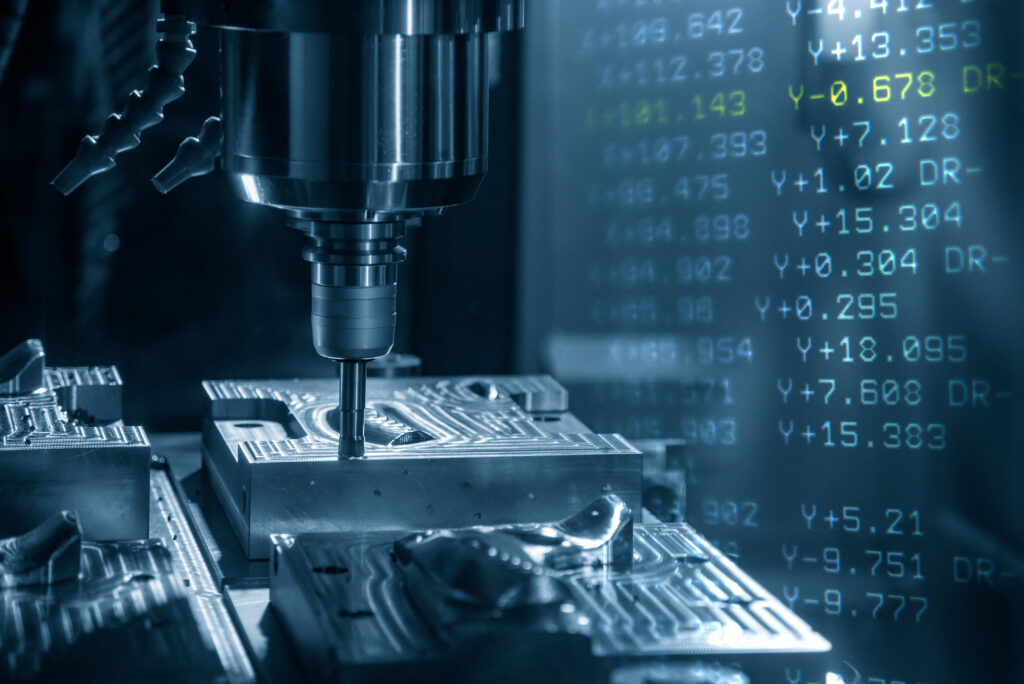
- CNC programming cycle time is significantly reduced irrespective of skill level & professional experience of the programmer. This also helps to reduce the machining time and, hence, the overall cycle time and manufacturing cost.
- As per the benchmarks conducted, NGSP enables on-machine CNC programming which is approximately 70% faster than regular G-code programming and up to 50% faster than classical conversational programming, in terms of programming time required.
Consistent Quality of Program Output and Part Manufactured
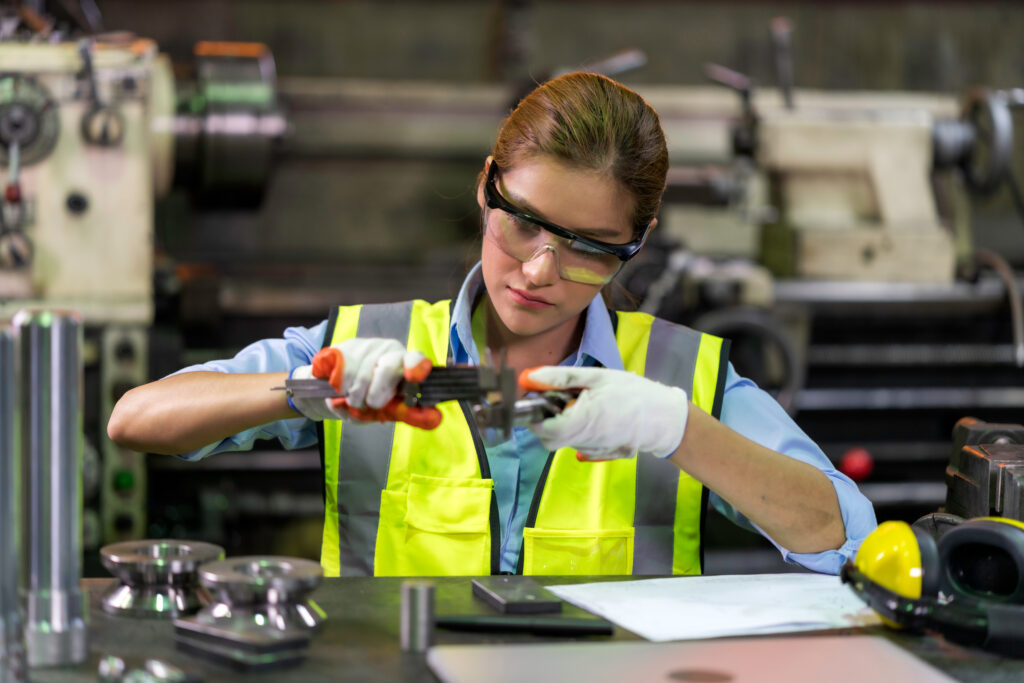
- CNC programming output is more consistent irrespective of skill level & professional experience of the programmer, ensuring better control over the quality of the part manufactured. This minimizes rejection and rework during the machining process, allowing better control over Cost of Poor Quality (COPQ).
Reduction in Training Time and Cost
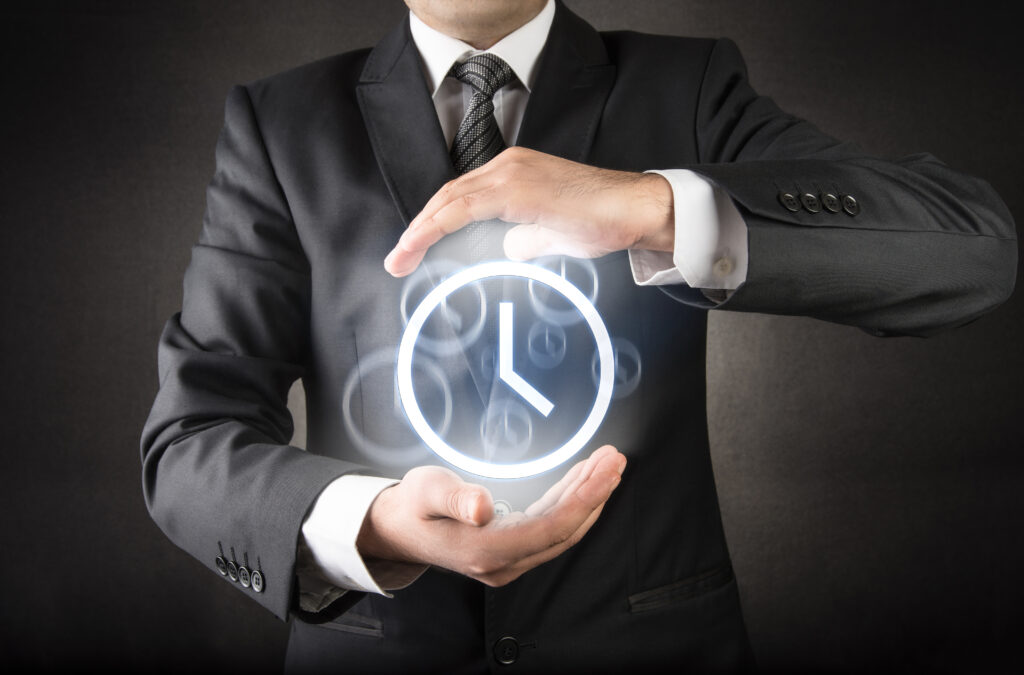
- The learning curve for new CNC programmers is shorter due to user-friendly interface and inbuilt programming knowledge based on features. This results in less training time and training cost. Dependency on highly experienced, skilled programmers is also reduced.
Smooth Execution with Improved Productivity
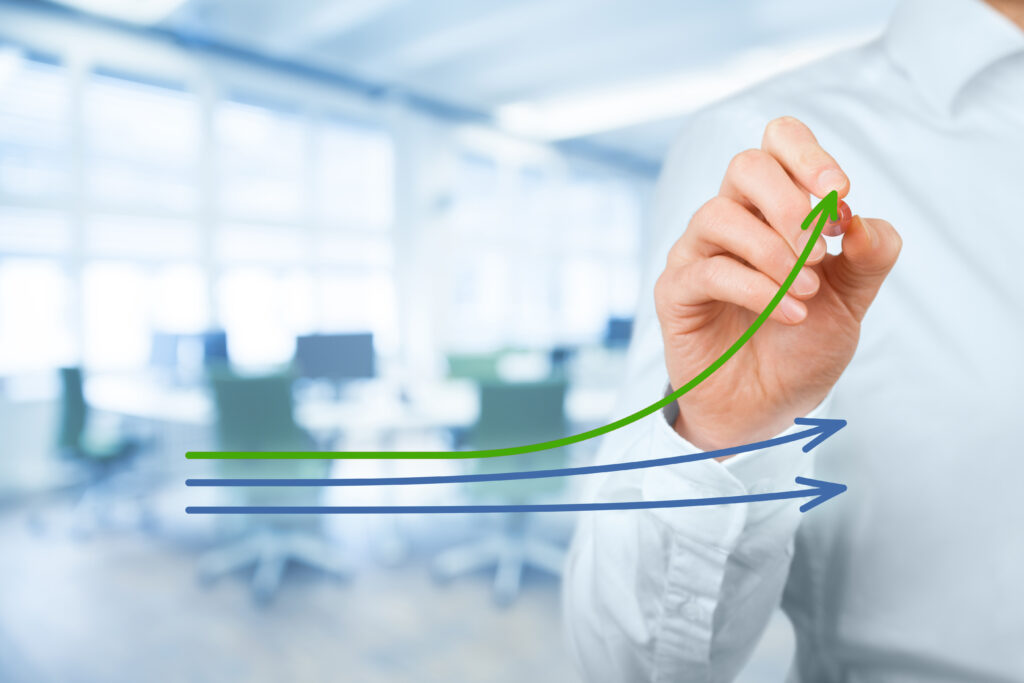
- Through the awareness of the complete manufacturing environment, which includes the in-process stock calculated after each operation, the final part geometry, the fixture, and the safe clearance to be maintained, NGSP reduces the risk of gouges, collisions, and tool breakages as well as eliminates air cutting.
- This avoids downtime and enables completion of machining operations according to the plan, ensuring on-time delivery to the end customer. This also enables optimum utilization of the CNC machine tool, providing better Overall Equipment Effectiveness (OEE).