Parts with positional features need multiple setups, and this can lead to higher cycle times and process errors. Complex part geometries don’t allow for pure 3-axis roughing. In these scenarios ModuleWorks Automatic 3+2-Axis Roughing provides an efficient solution. By just selecting part geometry, users can generate roughing toolpaths for multiple sides automatically. This helps to avoid the manual labor of finding the correct direction for roughing of features such as undercuts.
Major Challenges
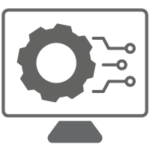
Complexity of Programming
Finding the correct direction of roughing for complex multi-sided parts is a tedious task, where the effectiveness of the process depends on users’ skills and experience. This increases the programming time as well as the machining cycle time of the parts.
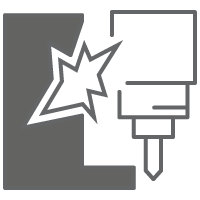
Avoiding Collisions
Collision checking is also a major challenge as no information about the current rest material and the in-process stock is generally available.
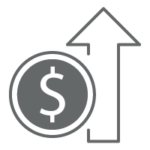
Higher Machining Costs
Overall machining cost increases due to longer programming time, requirement of skilled programmers and longer machining time due to inefficient toolpath.
Solution Offered by ModuleWorks
With ModuleWorks Automatic 3+2-Axis Roughing, the system automatically generates a roughing toolpath from different directions, including undercut areas that are inaccessible from the primary machining direction.
Key Features
Key Benefits
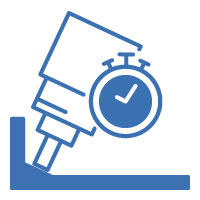
Easier and faster roughing of complex parts with multiple undercuts
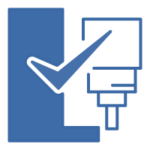
Collision-free and safe toolpath using Dynamic Holder Collision (DHC) checking
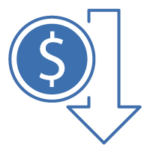
Reduced machining cost with automatic roughing process and minimum indexing
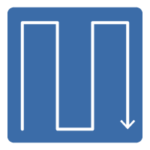