5-axis roughing is a common topic of discussion in modern day machine shops as it offers its benefits over traditional 3-axis roughing processes. With highly advanced multi-axis machines now being readily available in the market, programming these machines for their best utilization in terms of their capabilities and capacities is a challenge. Where traditional positional machining approach poses challenges during both programming and machining, Area Roughing by ModuleWorks enables users to program 5-axis simultaneous machining faster and with shorter tool shaft length (Projected tool length outside holder).
Major Challenges
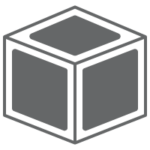
Roughing of Intricate Shapes
Roughing of intricate shapes is challenging as it requires precise control over the cut pattern and tool tilting. Inefficient toolpaths can cause higher cycle times and tool wear. Machining of undercut areas also gets difficult from primary direction.
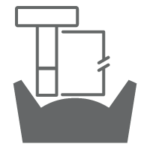
Higher Tool Shaft Length
Traditional machining approach for roughing operation requires higher tool shaft length to reach into deeper areas which results in excessive vibrations and uneven rest material and sometimes it even performs excessive machining (over-cut) on the part.
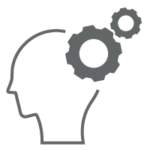
Lack of Programming Automation
Lack of programming automation would lead to higher programming time, possibility of higher human errors, and underutilization of the machine tool.
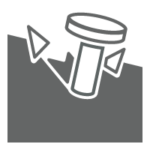
Lower Material Removal Rates
With the traditional approach of cutting the material by z-level slices, cycle times are much higher due to low material removal rate. When machining complex shapes using this method, it is difficult to control the non-machining time which results in higher cycle time.
Solution Offered by ModuleWorks
Area Roughing by ModuleWorks is developed to work on the mesh model to generate simultaneous 5-axis toolpaths for roughing. This roughing technology establishes better control over multi-axis roughing process by having the tool axis controlled by the floor surface. Area Roughing with adaptive cut pattern can reduce the cycle time and improve the tool life drastically.
Key Features
Mesh based input and very few subset geometries ensure faster programming. Users can select the entire part as a machining geometry and then apply containment to limit the toolpath to their preference. Users only need to define the following subset of geometries.
- Part surfaces
- Floor surfaces
- Ceiling surfaces (if needed)
- Stock geometry
- 3D containment
Area Roughing cut pattern is developed to adapt to variety of part geometries, even those with complex surface topologies. Majorly offset and adaptive cut pattern are part of the solution but in addition following sub types are also available,
- Offset from the ceiling
- Offset from the floor
- Morph between ceiling and floor
- Adaptive pattern
Just like in 3-axis machining, stock-based rest roughing is now possible. Highly automated stock manager accurately determines the rest material to generate efficient toolpath. Stock awareness optimizes the links, which reduces the non-cutting time. With detect stock thicker than option, users can get rid of the redundant passes.
Key Benefits
Area Roughing by ModuleWorks can be deployed in both 5-axis roughing and pre-finishing processes. Also, it finds its place in the Aerospace and Automotive industry and any manufacturing sector which involves machining of complex parts.
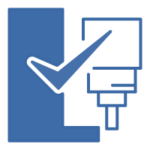
Safe and efficient toolpath
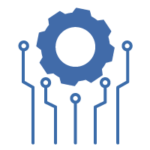
Less programming time due to highly intuitive workflow
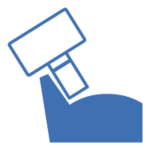
Improved stability and less vibrations due to shorter tool shaft length
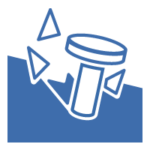
Reduced machining cycle time due to higher material removal rate
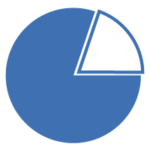