Wire Arc Additive Manufacturing (WAAM)
Implement Proven WAAM Technology with ModuleWorks
The ModuleWorks Wire Arc Additive Manufacturing (WAAM) solution is tailored for companies developing CAM software solutions that use welding techniques for 3D printing with a machine tool or robot. This includes CAD/CAM software vendors who are planning to enter the additive manufacturing market as well as robot integrators and robot OEMs along with machine tool builders and welding hardware manufacturers who are developing WAAM solutions.
Major Challenges
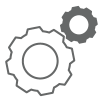
Process Optimization
WAAM requires accurate control of the process parameters such as welding speed, current, voltage, wire feed, or powder speed based on the fundamental welding principles. These process parameters have a big effect on deposition speed and the microstructure of the part. Finding the right combination of these parameters is essential to achieve the desired result.
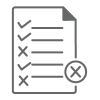
Reducing Defects and Improving Quality
WAAM is susceptible to typical defects that occur during welding such as porosity, distortion, and residual stresses, which can lead to parts of lower quality and strength, significantly impacting their performance. Minimizing these defects is crucial to producing good quality parts.
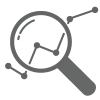
Predicting the Outcome
The quality and performance of deposited layers can be hard to predict. This is why an automated and proven system is needed to effectively define the parameters and achieve the expected output.
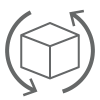
Post-Processing the Part
Because the quality of the components and features produced by WAAM is significantly lower and the surface is very rough, an additional finishing process, typically milling, is required to finish the part.
Solution Offered by ModuleWorks
ModuleWorks offers an advanced and proven solution for Wire Arc Additive Manufacturing (WAAM) to meet the requirements of the industry and support the wider adoption of this technology. The solution incorporates a toolpath planning algorithm specially designed for complex geometries and customized structures. The algorithm optimizes the manufacturing of near net shape geometries for different welding processes. Process parameters such as welding speed, current, voltage, wire feed, or powder speed can be defined to achieve a specific wall width/height (multi-layer) with maximum deposition efficiency.
Key Features
With this functionality, users can divide the workpiece into different segments and produce each individual segment with its own toolpath and individual parameters. This provides enhanced control over the weld deposition sequence and greater path planning flexibility while also reducing link motions.
ModuleWorks WAAM supports a range of strategies for automatically calculating performance-optimized toolpath patterns for different part geometries and manufacturing requirements. The solution also provides weaving toolpath patterns, such as rectangular and rounded patterns, for manufacturing components with varying thicknesses and wall structures.
Key Highlights
Advanced Toolpath Generation for Complex Geometries
The solution is based on freeform slicing and supports up to 6-axis toolpath calculations. Defining the orientation of the 6-axes is especially important for the WAAM process because the wire must be guided at a specific angle to the heat source.
The pattern is driven from a base curve, or a drive mesh surface, and all weld slices are created as 3D-equidistant paths from that contour. Various options allow precise control over the toolpath. Additional options like support for constant distance between the welding slices, lead/lag angles or side tilt angles, full collision avoidance, and multi-layer welding toolpaths ensure optimal toolpath generation.
Proven ModuleWorks Technology
ModuleWorks WAAM technology has been developed with extensive research in collaboration with leading industrial partners. The technology is also making a successful impact in numerous production environments where it has solved real-world challenges and already established itself as a proven and reliable technology.
Key Benefits

Seamless integration for rapid implementation of an industry-proven WAAM solution for manufacturing complex shapes and features

Reduction in development and maintenance costs, while providing advanced features and functionalities such as weaving or multi-body to the market

Increased cost savings for manufacturers by providing functionalities to accurately generate 3D printed parts

Possibility to join collaborative development activities to form a mature technological landscape for WAAM

Increased productivity and flexibility for manufacturers with provision for software upgrades to the latest available technologies

Support for repairing and feature additions to an existing part which reduces the overall investment and is more sustainable than building up new parts
Customer Success Stories
ModuleWorks and METROM Collaborate on Mobile Hybrid Manufacturing
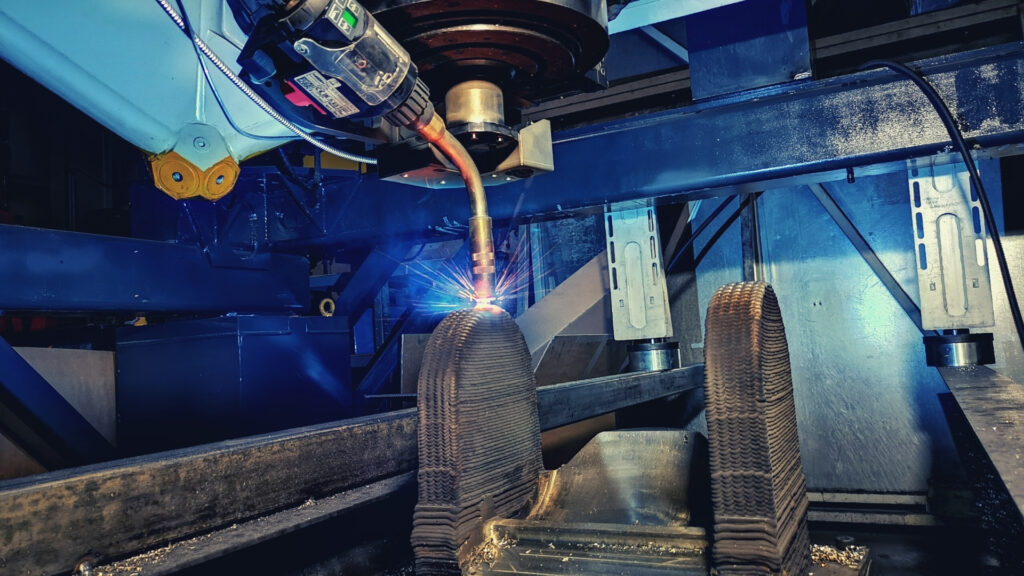
METROM, manufacturer of parallel kinematic machine tools, has integrated ModuleWorks hybrid toolpath planning software into its pentapod machining centers to offer high-performance additive and subtractive manufacturing of complex freeform workpieces on a single, mobile machine tool.
Hybrid Manufacturing at the Push of a Button
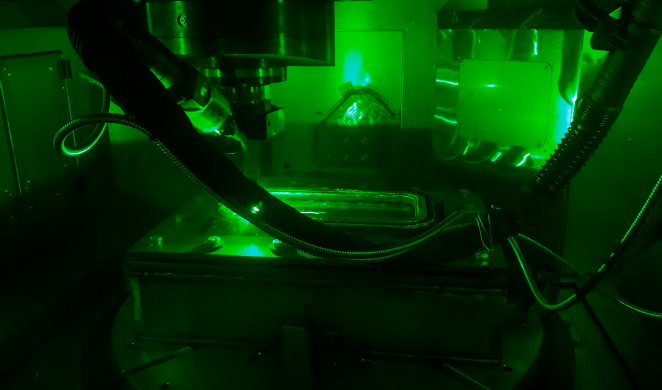
To unlock the potential of the latest manufacturing systems, 1A Technologies teamed up with ModuleWorks to develop a push-button solution for manufacturing and repairing components with both additive and subtractive processes for all kinematics and different types of technology. The new solution is available in the HY5CAM software from 1A Technologies.