Powder Bed Fusion (PBF), also known as Selective Laser Melting (SLM)/Selective Laser Sintering (SLS), is a widely used additive manufacturing technique due to its low cost and recyclability of powder. As applications grow, there is a rising demand for efficient CAM software solutions that meet all requirements.
ModuleWorks provides an advanced and research-based Powder Bed Fusion (PBF) solution that is tailored for organizations offering CAM software solutions for Powder Bed Fusion, such as Trumpf. This includes CAD/CAM software developers looking to break into the additive manufacturing market, as well as hardware manufacturers who develop PBF machines. With ModuleWorks, these companies rapidly develop innovative and powerful PBF solutions and features and get them to market faster. Typical PBF applications include aerospace, medical, and prototyping.
Major Challenges
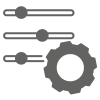
Controlling Process Parameters
The control of process parameters, such as optimizing laser settings, is crucial to achieve a stable result and a near net shape structure. This ensures consistent part quality and reliability.
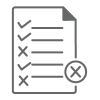
Reducing Defects
PBF is also prone to several defects such as porosity, residual stresses, and surface roughness. Controlling the repeated cooling cycles during layer-by-layer deposition to ensure precise layer alignment and bonding is also vital for high-quality results.
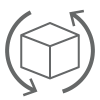
Post-Processing the Parts
Parts manufactured using the PBF process often require post-processing to achieve the final surface quality and required precision. This includes additional machining to finish the surface with the desired dimensions while staying within tolerances.
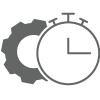
Production Time
PBF is considered to be a time-consuming process, especially for parts that are large or complex in nature.
Solution Offered by ModuleWorks
The ModuleWorks Powder Bed Fusion (PBF) software library enables quick and easy development of advanced, all-encompassing PBF solutions. It delivers high-performance laser melting for a range of materials including plastics, metals, ceramics, and sand. Freely configurable sub-components support different hatching patterns such as chess, striped, and parallel hatching. Support for very large parts enables cost-effective rapid prototyping.
Key Features
Many other parameters can be set up for the process in order to manufacture the part based on the requirement. Users can even add multiple parts where each can have its own parameters and settings, or the parameters can be kept same. This practice is very common in industries where identical parts have to be produced.
Arc output is also supported to generate exact geometry for a better surface finish. This also reduces output data up to 15 times which enables printing of large parts easily.
Key Highlights
Hybrid Manufacturing
With ModuleWorks’ holistic portfolio, a complete PBF solution can be offered that enables not just additive manufacturing but also subtractive manufacturing together with best-in-class simulation and post-processing functions. Subtractive manufacturing is enabled with ModuleWorks’s industry-proven toolpath components that range from basic 3-axis machining to more advanced simultaneous 5-axis machining.
Key Benefits

Industry-proven PBF solution for precision manufacturing of even the most complex parts

Reduced development and maintenance costs and rapid implementation for being first-to-market with the most advanced features and functionalities such as big data calculation and arc output

Opportunities for collaborating on joint development projects with ModuleWorks to form a mature technological landscape for PBF
