Polymer Printing
Take Rapid Prototyping to the Next Level with ModuleWorks Polymer Printing
Since its emergence polymers and composites have been well-known for its efficiency, precision, and customization potential. The 3D Printing technology utilizes through layer-by-layer deposition to produce near-net-shape parts of intricate designs or functional prototypes. ModuleWorks Polymer Printing Technology supports for all kind of geometry complexity and gives users all the required flexibility to freely configure all sub-components, such as free print pattern generation in the infill and in the support areas. This technology is developed for Fused Filament Fabrication (FFF), Large Format Manufacturing (LFAM) or continuous fibre laying.
Major Challenges
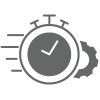
Quality and Speed
In additive manufacturing and even with other materials in 3D printing, achieving high quality often means sacrificing speed. This affects the production rate badly.
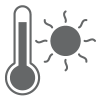
Managing Part Quality
Polymers expand when heated and contract when cooled. This can lead to warping, shrinkage, or layer separation, particularly in methods like Fused Filament Fabrication (FFF) where layers are added sequentially. Also visible seams on the part or stairs effect in shallow areas can be a visible drawback of additive technology.
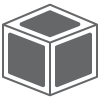
Complexity of Parts
With increasing part complexity, printing of lattice structures, internal channels and organic shapes is favoured instead of being milled, to reduce material wastage.
Solution Offered by ModuleWorks
Polymer printing utilizing different materials such as plastics ABS and PLA, continuous fibre laying material, concrete and others due to its cost-effectiveness in producing three-dimensional objects. In this process, the object is constructed layer by layer on e.g., a movable or fixed positioner, which helps prevent warping and ensures proper adhesion of the bottom layer.
Depending on the design, either the nozzle, the build plate, or both may move. The printing speed must be carefully controlled to allow optimal build up and consider required cooling temperature. The quality of the print depends not only on the digital model but also on the precision of the movements, the fineness of the nozzle, and the thermal properties of the material used.
Key Features
The outcome of this technology is a continuous toolpath which guarantees uninterrupted material supply and ensures a stable process and high component quality. Additionally, this solution prevents toolpath trimming, which usually results from the constant offset. This ideally works on feature addition such as building up additional segments on pre-existing surfaces.
Key Highlights
Proven Technology for Rapid Prototyping
Moduleworks Polymer Printing solution enables 3D printer manufactures to produce functional prototypes and organic shapes to build parts at much faster rate. This technology works with NURBS and meshes, evaluates the model for overhang and builds support structures that too with minimum contact area with the workpiece. User friendly workflow ensures faster programming times and less human errors.
Multi-axis Enabled
Complex parts can be manufactured without any support structures. With Enablement of multi-axis technology users can print on curved freeform surfaces which do not necessarily have a base structure. Moduleworks offers a full range of 2.5D and 5-axis additive solution which helps 3D printer manufacturers to build a customized solution for their customers.
Simplified 3+2 Polymer Printing
These systems eliminate the need for support structures, allowing for faster build times and the effective segmentation of complex parts. They utilize intelligent build-up orders and collision avoidance mechanisms to streamline production while minimizing errors. Multi-threaded capabilities and automated systems further accelerate the process, ensuring rapid completion of tasks. Additionally, these systems feature auto-analysis of print quality across different zones of the workpiece, enabling real-time adjustments for optimal results. Users can manually place build planes and apply these techniques to any part family, whether for functional components or intricate organic structures, demonstrating the technology’s adaptability and precision.
Non-linear Printing
3-axis 3D printers typically operate using a layer-by-layer method, resulting in a 2.5D approach. This means they primarily move in the X and Y axes while the Z axis adjusts in a constant manner, which can create a staircase effect on shallow areas. To minimize this effect, the printer needs to adapt to the surface topology, requiring simultaneous movement of the Z axis. While most printers are capable of such simultaneous movements, the limitation lies in the software’s ability to accurately compute the necessary machine coordinates. Coming from a multi-axis background, Moduleworks provides ready-to-use strategies that can calculate additive paths on freeform surface.
Key Benefits

Lower cost of rapid prototyping

Easier manufacturing of complex shaped parts

Shorter learning curve due to highly intuitive workflow

Less waste during manufacturing due to automatic support structures
