The Hammer Peening solution is designed for companies that develop software solutions integrating Hammer Peening processes into their workflows. This includes CAD/CAM companies, machine tool builders, robot OEMs, and integrators aiming to support the Hammer Peening process within the manufacturing chain.
Major Challenges
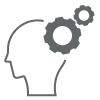
Manual Control
Improper control of Hammer Peening can lead to surface irregularities. To achieve consistent results precise management of peening parameters such as impact force, frequency, and coverage is essential.
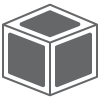
Complex Part Geometries
Programming complex parts for Hammer Peening involves significant challenges. The process demands completing complex and large parts in a single operation to ensure consistent surface finishing across the entire part.
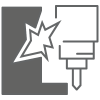
Collision Avoidance
Ensuring collision-free operation is difficult because we lack advanced simulation tools. This makes it hard to simulate and verify the toolpath.
Solution Offered by ModuleWorks
The ModuleWorks toolpath calculation optimally drives the machine tool with a process-relevant parameterization up to 5-axis machining. It includes collision checking, linking, and other essential process parameters.
Key Features
Key Highlights
Advanced Toolpath Generation for Complex Geometries
Technology offers various options that allow precise control over the toolpath. Additional options like support for the constant distance between the toolpath slices, lead/lag angles or side tilt angles, full collision avoidance, and multi-layer toolpaths. Precise control over the direction and movement of the peening ensures that the surface finish will be consistent at each point.
Proven ModuleWorks Technology
Key Benefits

Achieve high surface finish in one operation with modern peening tools

Simplifies the production of complex parts through precise control and intuitive parameter settings

Simulate and verify the toolpath before executing on the machine for maximum safety and reliability
