Adaptive Roughing
Elevate Machining Productivity to the Next Level with ModuleWorks Adaptive Roughing
With a wide variety of materials being used for diverse applications, achieving faster machining speeds without compromising on tool life is a challenge. This is why ModuleWorks has developed a CAM software component that enables CAD-CAM software developers, machine tool builders and CNC controller manufacturers to offer faster roughing with improved tool life for end users. This high-speed roughing strategy delivers optimal roughing, especially for complex parts in automotive, aerospace, and oil and gas applications.
Major Challenges
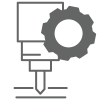
Lower Material Removal Rate (MRR)
Conventional roughing processes have a lower material removal rate, leading to longer machining cycle times. The top-down Z-level slicing approach is relatively slow for roughing and has a lower material removal rate, especially when machining harder alloys.
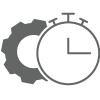
Optimizing the Tool Life
Higher forces and varying tool loads, especially in sharp corners, can cause premature tool wear. Also, unavoidable full width cuts can reduce tool life due to constrained chip evacuation while cutting the material.
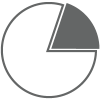
Underutilization of CNC Machine Capabilities
Since machines are often subjected to inconsistent loads during conventional roughing, operators cannot apply higher speeds and feeds, resulting in underutilization of the machine tool.
Solution Offered by ModuleWorks
ModuleWorks Adaptive Roughing is a high-speed roughing strategy that generates a smooth spiral and trochoidal pattern by continuously measuring the engagement of the tool within the stock. In addition, the minimal curvature radius produces smooth toolpaths in the corners to avoid abrupt motions along the entire toolpath.
Cut Pattern
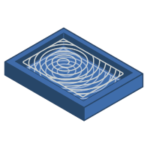
- The high-speed roughing pattern effortlessly adapts to any part geometry.
- High axial depth and low radial stepover provide constant chip load for higher material removal rates.
- The Adaptive pattern automatically generates smooth spiral and trochoidal motions, allowing higher accelerations.
Geometry Support
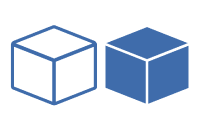
- The flexible Adaptive Roughing strategy optimizes machining on a variety of geometries including solids, surfaces and STL meshes.
- 2D wireframes can be used as input.
Stock Awareness
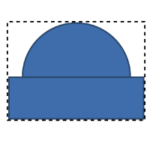
- Smart ordering inside the toolpath ensures fewer links between areas.
- Open areas can be approached from outside the stock.
- Stock awareness opens new rest roughing possibilities and creates safe and efficient toolpaths.
Adaptability and Safety
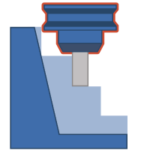
- ModuleWorks Adaptive Roughing comes with pre-drill hole management, empowering end users to further optimize the toolpath.
- Step up approach for the 3D contours enables end users to perform roughing on 3D shapes to provide a uniform stock finish after roughing.
- Dynamic Holder Collision (DHC) check to ensure collision-free toolpaths.
Applications
ModuleWorks Adaptive Roughing integrates seamlessly with other ModuleWorks components, including 2D wireframe, 3-axis, multi-axis, turning and port machining to enhance the performance and scope of digital manufacturing solutions.
Key Benefits
Safe and Collision Free Toolpaths
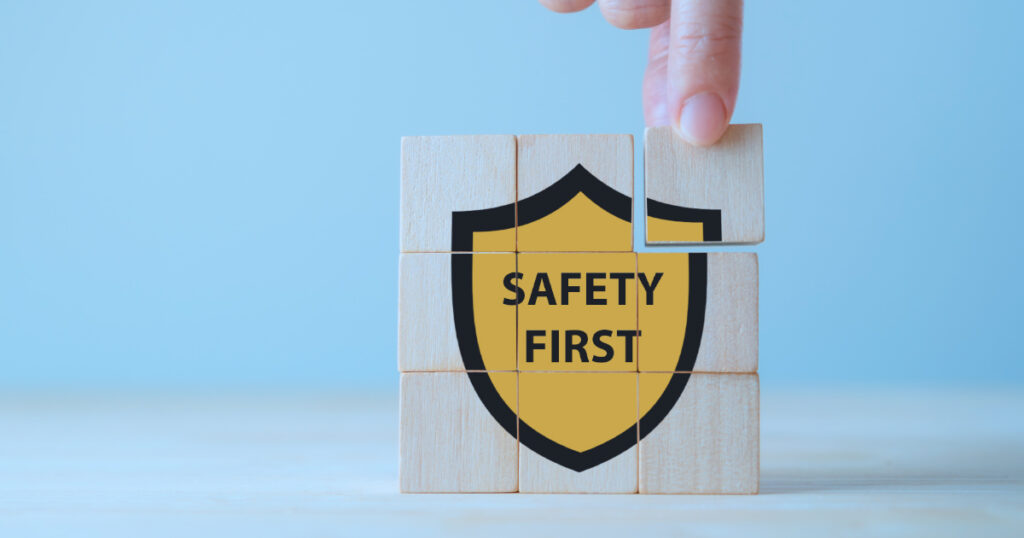
- Adaptive Roughing is equipped with Dynamic Holder Collision (DHC) checking for generating safe, collision-free toolpaths.
- Comprehensive collision checking includes the part geometry and in-process workpiece (IPW). If a collision is detected, colliding passes are trimmed and a safe toolpath is created.