3-Axis Machining Solution
Optimize 3-Axis Machining with ModuleWorks Technology
Advanced, Safe, and Efficient 3-Axis Machining Solution
ModuleWorks offers advanced software technology to optimize 3-axis machining, empowering CAM software developers and CNC controller manufacturers with high-performance components for collision-free roughing, rest-roughing, finishing, and rest-finishing. Designed for seamless integration, these components enable rapid, next-level development of innovative 3-axis solutions across a range of industries, including aerospace, automotive, mold and die, and production machining.
Major Challenges
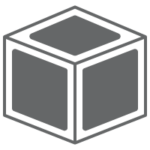
Increasing Complexity of Parts and Programming
As technology advances, parts are becoming more complex, making it increasingly challenging to create efficient toolpaths and CNC programs. The parts often include complex contours, undercuts, and internal corners that make CAM programming difficult.
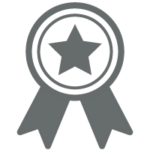
Achieving the Required Part Quality
Because customers expect products of the highest quality, it is imperative to machine parts with the utmost precision which is often challenging.
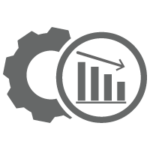
Reducing Rework/Rejections
Minimizing or eliminating rework and rejection during the machining process is crucial to reduce the Cost of Poor Quality (COPQ). This requires a highly accurate machining process.
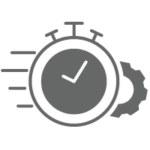
Reducing Programming and Machining Times
Manufacturers need to reduce programming and machining time to achieve faster machining cycles and lower manufacturing costs. This is key to reducing time to market and remaining competitive.
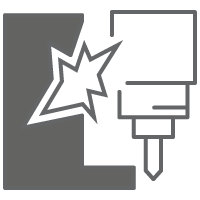
Avoiding Collisions
During the machining process, there is often a risk of collision for the tool or holder which needs to be detected and assessed during toolpath generation. Any collisions during the actual machining process lead to loss of productivity and sometimes even damage to the costly machine tool.
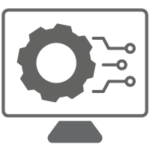
Optimizing the Utilization of Computer Hardware
Manufacturers use state-of-the-art workstations with the latest computer technology for CAM programming. However, the full capabilities of the computer hardware often remain untapped.
Solution Offered by ModuleWorks
The ModuleWorks 3-Axis Machining Solution enables CAM software developers and CNC controller manufacturers (and the manufacturing organizations who are their customers) to resolve challenges such as optimizing manufacturing cycle times, reducing manufacturing costs, and improving the quality of machined parts.
The ModuleWorks solution boasts a state-of-the-art software architecture resulting from 500 person-years of cumulative and dedicated 3-axis research and development by an experienced and highly skilled team.
Modern Architecture
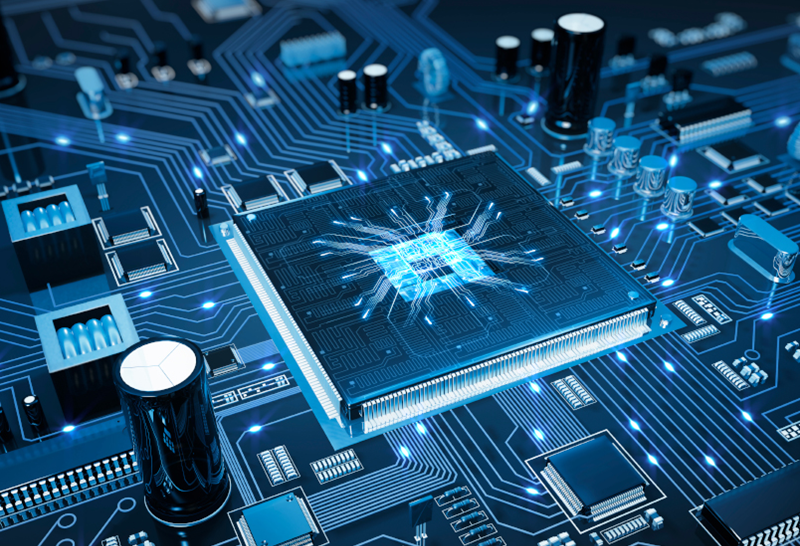
ModuleWorks delivers an advanced kernel to seamlessly handle complex toolpaths.
- Modern programming techniques generate efficient and precise toolpaths.
- Leverage the full computing power of the latest workstations with up to 24 cores for ultra-fast toolpath generation.
- Deploy the kernel on all major operating systems such as Microsoft Windows, and Linux as well as machine controllers.
- The solution is cloud-ready for effortless deployment in cloud environments.
- Native support for modern 64-bit systems ensures optimal performance and compatibility.
Generate Best-in-Class Toolpaths
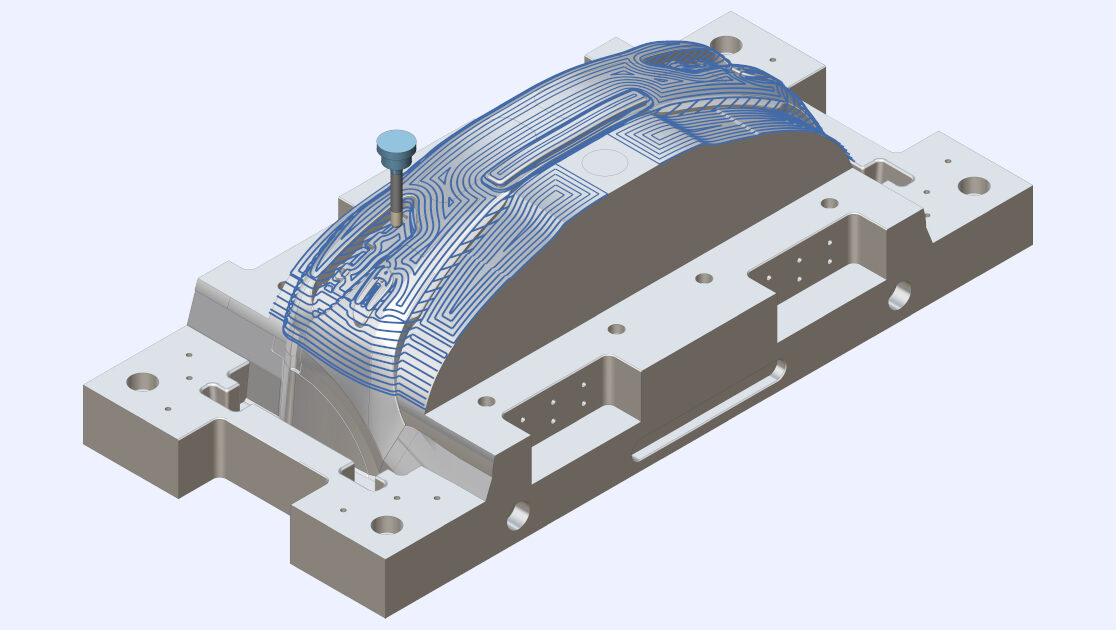
Utilizing the high-performance architecture, ModuleWorks technology generates best-in-class machining toolpaths that include:
- Various options for roughing (high-speed offset roughing, adaptive roughing, or traditional parallel roughing).
- Rest roughing to remove leftover material using a smaller roughing tool.
- A variety of finishing toolpaths to completely machine both shallow and steep regions.
- Rest finishing to finish corners or regions left by the previous finishing toolpath.
Achieve Quality/Precision and Reduce Rework/Rejections
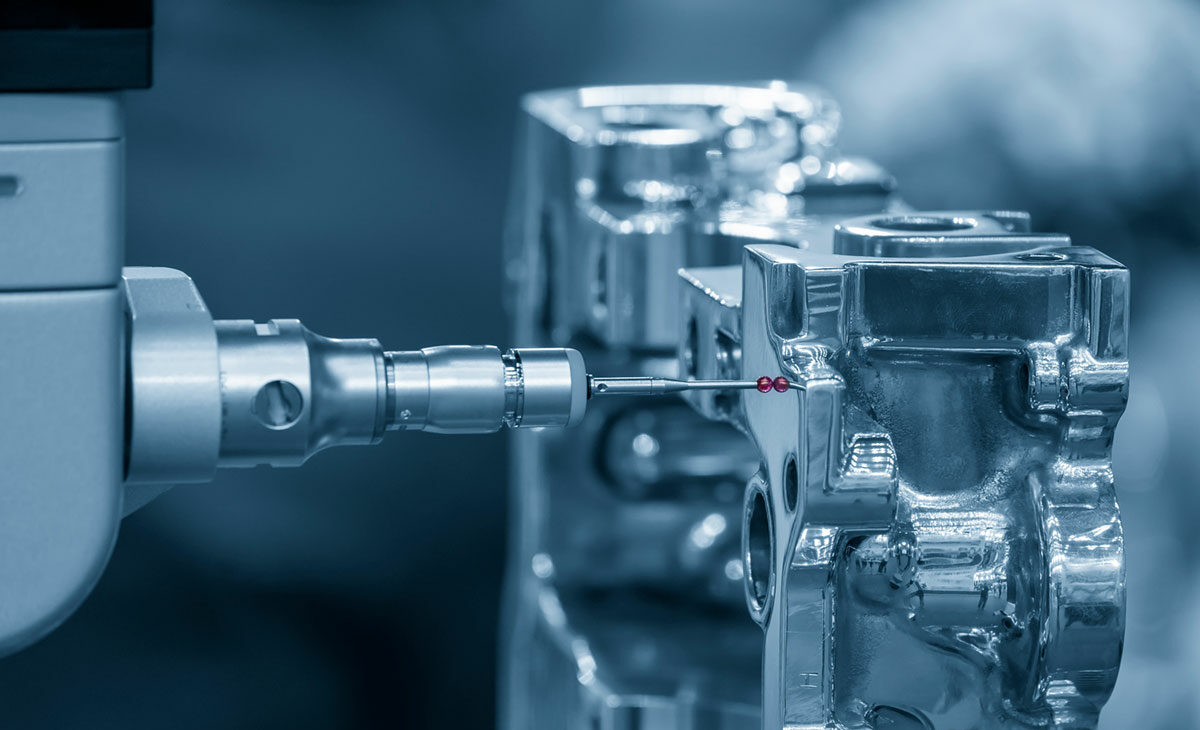
Based on advanced mathematical algorithms, ModuleWorks toolpaths ensure the highest levels of machining precision and safety.
- The toolpaths deliver high-quality surfaces thanks to optimized point distribution and advanced arc-fit options. This generates precise toolpaths for outstanding surface finish.
- All the strategies support collision checking against the current workpiece, the in-process workpiece (IPW), and fixtures. For gouge checking, the calculation considers the tool flute, shank, arbor, and holder to ensure the creation of safe toolpaths.
Reduce Programming and Machining Times
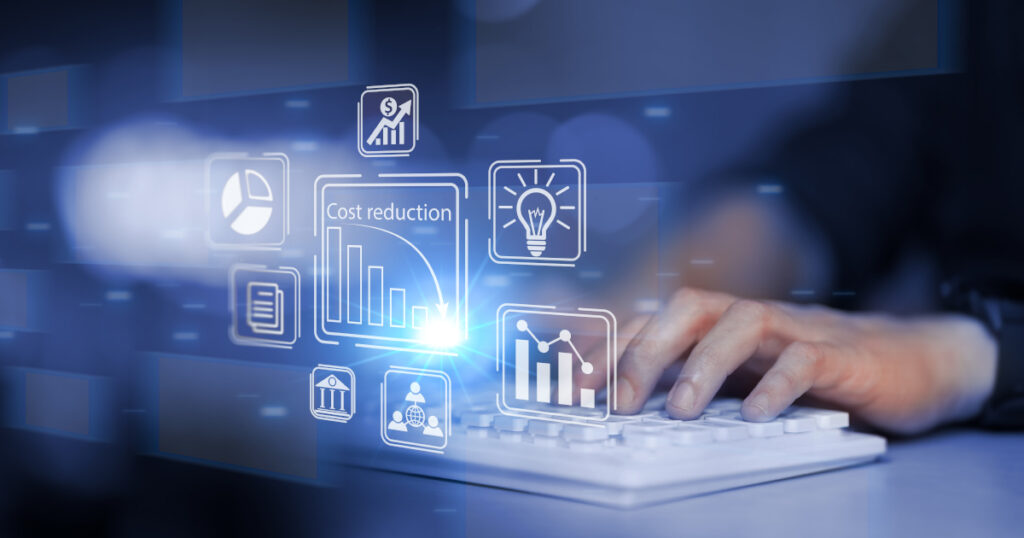
The ModuleWorks solution accelerates throughput by reducing the overall manufacturing cycle time for parts.
- The toolpaths provide a comprehensive range of options for machining components according to requirements. End-users can select the optimal strategy for the job in hand.
- Link and ramp entry heights are also optimized as in-process stock information is always available.
- Link moves are further optimized to provide the shortest gouge-free traverse motion.
Optimum Hardware Utilization
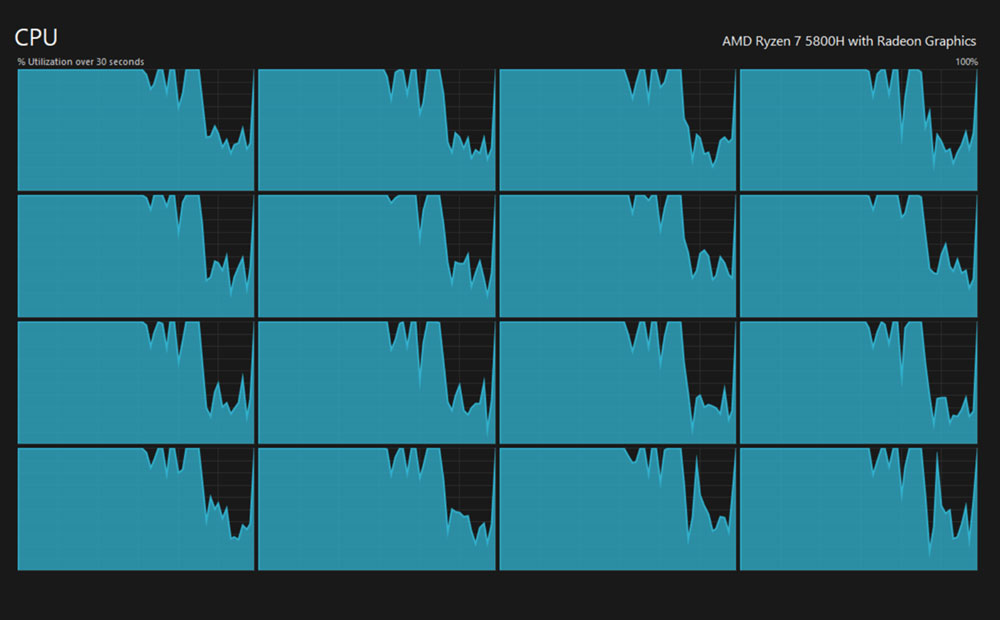
ModuleWorks provides proven technology that leverages the full performance advantages of the latest hardware to accelerate toolpath calculations.
- The toolpaths are individually computed on multiple cores and scale up easily on modern systems.
- The thread-safe kernel enables the distribution and calculation of multiple operations in parallel using multi-core processors.
- Recalculations are faster thanks to caching. Each stage of the toolpath calculation is cached so that subsequent toolpath edits are calculated much faster, especially when there are changes to the links or stepovers.
Key Highlights
3-Axis
ModuleWorks 3-Axis is an industry-proven CAD/CAM software component for machining simple to complex parts in 3-axes. The components can be easily integrated into third-party environments such as CAD/CAM solutions, CNC controllers, and even the cloud. It includes a comprehensive range of 3-axis machining strategies offering gouge-free machining on triangle mesh-based models. Strategies include roughing, rest-roughing, and a range of powerful finishing strategies.
Adaptive Roughing
The ModuleWorks Adaptive Roughing solution utilizes the full potential of cutting and machine tools to increase the productivity and profitability of roughing processes. Consistent tool engagement delivers a smooth toolpath motion to dramatically increase material removal rates, reduce cycle times, and extend tool life compared to conventional roughing strategies.
Smart Roughing
ModuleWorks Smart Roughing is the most advanced process simulation and optimization solution for 3-axis CNC programming. With Smart Roughing, the CAM software automatically calculates the stepover, stepdown, and corresponding speeds and feeds using a physics-based model. These parameters are calculated considering spindle torque/power, cutting load, vibrations, chip thickness, chatter, and tool bending forces. As a result, the material removal rate (MRR) is maximized while maintaining stable cutting conditions.
Key Benefits

Generation of efficient 3-axis machining toolpaths to produce high quality complex or large-sized parts using reliable and proven ModuleWorks technology

Better control over rejections/rework and hence the Cost of Poor Quality

Optimized programming time, machining time, and hence manufacturing costs

Generation of safer toolpaths by detecting and avoiding collisions

Improved productivity through optimum utilization of the latest hardware for faster generation of complex toolpaths

Flexibility through fast recalculation of edited toolpaths
Customer Success Story
Amod Onkar (Vice President – Milling Products, SolidCAM) talks about the benefits that SolidCAM has brought to its customers by using the ModuleWorks 3-Axis Machining solution. He explains how the ModuleWorks roughing and finishing technologies enable SolidCAM customers to manufacture parts faster, safer, and more efficiently while achieving the highest quality standards.