Collision Avoidance System
Making Manufacturing Process Safe and Reliable with ModuleWorks Collision Avoidance System
With a variety of complex multi-axis machine tools being developed, it is challenging to ensure safety from collisions and major accidents unless the manufacturing process is verified. ModuleWorks Collision Avoidance System is developed to work on CNC controller, also as an integral part of the CAD-CAM software to efficiently protect their equipment from collisions. It offers a plug and play solution which can be setup on CNC machine controller. It has the edge over current competitors since it communicates with the machine for any malfunctions and stops the machine when it finds any probable collisions.
Major Challenges
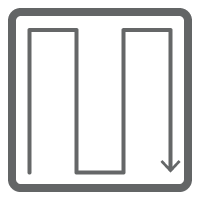
On-Machine Toolpath Verification
With fast-paced production environment, it is important to verify the toolpath for collisions to avoid the damages to the equipment. However, toolpath verification in a CAM system does often not have all the information required for an exact simulation and full G-Code based simulation systems can be costly.
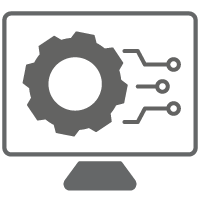
Establishing Machine Communication
The CNC control is the final authority generating the toolpath and axis movement of a machine tool. To accomplish this, it is provided information like tool lengths and work offsets, which are usually measured from the real machine setup. In order to have the most accurate simulation of a process, it is also necessary to utilize this and other CNC-specific data and therefore communicate directly to the CNC machine.
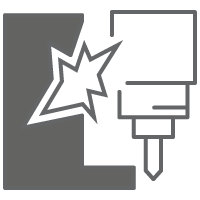
Collision Avoidance
Collision avoidance for the manufacturing process is of utmost importance since it holds a high risk of damaging machine – resulting not only in high costs for repairs but also in production downtime. Not all the movements on the machine – like manual operations during setup – can be verified before the process.
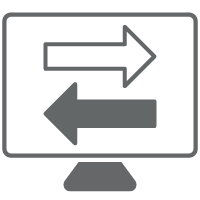
Interoperability
With traditional methods data like setup inputs from the CAM software cannot be directly imported into the machine controllers, and thus the machine operator must manually re-enter data on the machine, which can result in errors due to unused information or wrong inputs.
Solution Offered by ModuleWorks
ModuleWorks Collision Avoidance protects CNC machine tools against operating, parametrization, and programming errors during the production process. Collision Avoidance is available in two product variants, Core and System (CAS), to fulfil the market requirements for both standardization and customization.
Key Highlights
Collision Avoidance System (CAS)
CAS achieves its mission by simulating the machine movements as a digital twin. Here, not only the past and current machine movements are considered, but CAS also leverages prediction information that the NC provides about movements that will happen in the future. If CAS detects that this preview will lead to a collision situation, it stops the NC machine before the collision actually happens.
Dedicated workflows allow the use of common data types, such as STEP or STL, to define the tooling. Data exchange with other IT systems can be implemented via the publicly available Manufacturing Data Exchange Specification (MDES).
Ideally the shop floor process flows are built to ensure high quality end products, yet some errors get carried forward due to manual interference. The Collision Avoidance System increases process safety by using the actual data available on the CNC.
Collision Avoidance Core
With Collision Avoidance Core, the core business logic of the system is made available to integrators who want to develop their own, customized collision avoidance solution. The Collision Avoidance Core is a software component that contains all known features for processing control data, detecting collisions based on a virtual representation of the physical machine tool, and reacting to the detected collisions.
It can be integrated into a software solution with a tailor-made user interface to provide the best possible user experience for either specific use cases or as part of a universal automation system. For this purpose, the Collision Avoidance Core offers a modern programming interface (API) in C++.
Key Benefits
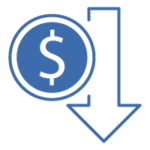
Avoidance of costly machine breakdowns and production holds
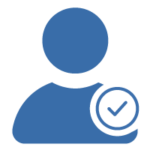
User friendly workflows improving the setup effectiveness and reducing the operator fatigue
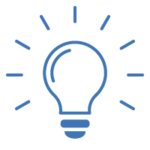
Shorter learning curve
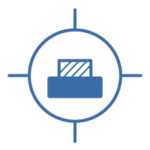
Import of setup and tooling data from CAM systems through MDES which helps to reduce the need to define digital twin which saves operator time
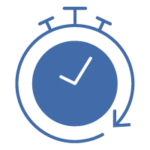