Developing simulation technologies is a complex, multi-year endeavour. Yet, manufacturing organizations and end-users demand efficient and reliable solutions to support their machining or additive manufacturing processes.
ModuleWorks addresses these challenges by offering state-of-the-art and cutting-edge simulation components. These components empower CAM software developers, machine tool builders, and CNC controller manufacturers to swiftly integrate and deliver top-tier toolpath and NC program verification tools. With advanced simulation functionality, ModuleWorks supports the verification of diverse manufacturing processes—from milling and turning to specialized areas like sawing and punching—coupled with an intuitive UI and powerful rendering methods.
Major Challenges
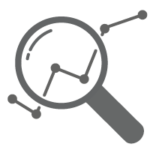
Need of Proven Systems
The CAM programming always requires thorough validation of the toolpath and NC code. Users demand tried and tested simulation technologies to ensure their NC programs are 100% safe.
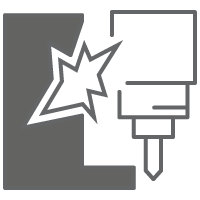
Avoiding Collisions
Manufacturers need to produce parts without any damage or collision on the machine tool. To do this, a lot of time is spent verifying the CAM program and executing the same as a trial which can be avoided through software systems.
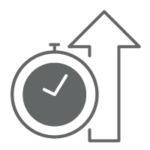
Reduced Overall Time to Produce a Part
Without simulating the manufacturing process, CAM programmers and machine operators face variety of surprises on the machine tool or robot which results in costly mistakes and subsequently delays that result in higher overall time to produce a part.
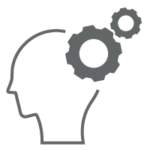
Visualization of the Process
It is always desirable, in general, for users to visualize the machining or additive manufacturing process. However, due to the limitations of software technology, they often need to compromise on many aspects of the process.
Solution Offered by ModuleWorks
ModuleWorks Simulation Systems product line provides multiple ready-to-go software systems that our partners can rebrand to market typical simulation solutions in the fastest way. The product line offers state-of-the-art tools that enable high performance and accurate toolpath and NC program verification.
The simulation components support Microsoft Windows-based desktop systems as well as Linux-based machine controllers located on the machine tool (depending on your hardware and software requirements).
Features
- Simulate both subtractive as well as additive manufacturing processes
- Supports milling, turning, wire-EDM, drilling, threading, laser, grinding, punching, sawing and more
- Broad solutions to address any kind of requirements around simulation
- Compatible with most modern hardware and software systems
Key Highlights
Collision Avoidance
ModuleWorks Collision Avoidance protects CNC machine tools against operating, parametrization, and programming errors during production. Collision Avoidance is available in two product variants, Core and System, to fulfill the industry requirements for both standardization and customization.
- The Collision Avoidance System is a plug-and-play solution that can be easily integrated into CNC machine tools.
- With Collision Avoidance Core, the core business logic of the system is made available to integrators who want to develop their own, customized collision avoidance solution.
Machine Simulation (MachSim)
Machine Simulation is a state-of-the-art CAM simulation solution that supports the user during toolpath creation. It simulates full machine models with integrated material removal simulation and performs collision monitoring during the simulation process. The Machine Simulation component supports subtractive processes for milling, turning, and beam cutting as well as additive manufacturing processes for laser cladding and 3D printing. Flexible kinematic definition, powerful APIs, and a range of customization tools ensure fast and seamless integration into existing and new applications.
External Posting Enabler
Drive state-of-the-art ModuleWorks Machine Simulation and Toolpath Verification from your post processor using the ModuleWorks External Posting Enabler. With the External Posting Enabler, ModuleWorks provides a powerful set of commands and services to control the simulation and bring it closer to the NC G-code and the real machining process. Adapting your existing post-processor to control the simulation is fast and seamless thanks to an integration-friendly architecture that enables rapid roll-out and convenient maintenance.
NC Editor
NC Editor is a powerful and easy-to-use tool for editing, simulating, back plotting, and verifying G-code for CNC machining.
The intuitive interface provides instant 3D simulation while you edit the program to detect potential collisions and errors at a glance and to instantly verify your changes to the code. Integrated Job Setup for fast and easy tool creation and built-in support for multiple CNC machines further accelerate and simplify the editing and verification process to make the NC Editor a complete NC verification system that optimizes the quality and efficiency of machining processes.
Visual Twin
Visual Twin is the next generation of machine visualization. It combines the power and flexibility of the ModuleWorks simulation components with state-of-the-art computer graphics to achieve a new level of realism that brings machines to life. It simulates a real production machine in real time and can be connected to a real CNC control just like the drives of the real machine.
Key Benefits
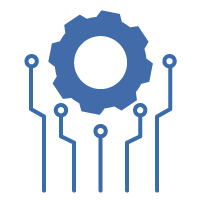
Ready-to-use systems that seamlessly integrate for the shortest time-to-market
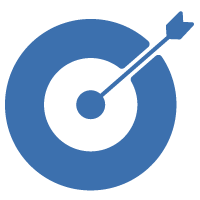
Proven technologies for confident implementation without the need to develop the technology from scratch
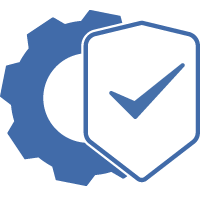
Accurate, faster, and safer process execution for end-users through advanced verification and simulation functionalities
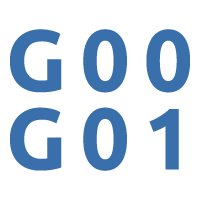