Extending the service life of railroad wheels through wire-based deposition welding
Funding agency: Bundesministerium für Wirtschaft und Klimaschutz
Project Number: 03EN2103D
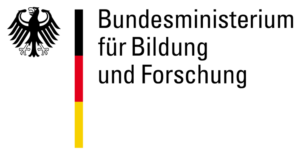
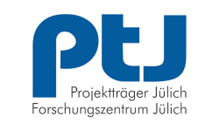
The project LEDA is funded by the Federal Ministry for Economic Affairs and Climate Action (BMWK) and the Projektträger Jülich under the project no.: 03EN2103D.
Details
Rail vehicle wheels are subject to life cycle-related wear from both local defects such as flat spots and chipping on the tread and circumferential tread wear. Currently, for safety reasons, the repair of damaged or worn railroad wheels by deposition welding or other additive processes is not permitted for trains on the public rail network in Germany and Europe. Thus, the aim of the joint project LEDA is to test the feasibility of such repairs and increase the economic efficiency of the repair process chain for railroad wheels by proving the potential of wire-based deposition welding processes as suitable new repair methods. By reducing the mass of a railroad wheel, the new repair process will significantly increase the material, energy and resource efficiency in the development and repair of railroad wheels. Thus, the development of a repair process for railroad wheels using deposition welding represents a big leap forward in terms of innovation and circular economy.
As rail vehicle wheels are safety-critical components, rail freight transport and maintenance fleets are predestined for testing innovative approaches, as there are lower barriers to the introduction of new technologies here than in passenger transport. Against this background, the joint project LEDA aims to use state-of-the-art wire-based deposition welding processes such as wire-based Laser Metal Deposition (LMD-w) and Wire Arc Additive Manufacturing (WAAM) to develop a repair process for both categories of wear, with a focus on quality and sustainability. For this, destructive and non-destructive testing methods during and after the process are needed to be able to detect the defects and to test the entire repaired wheels. Essentially, the project LEDA aims to achieve the long-term goal of increasing the economic efficiency of the repair process chain for railroad wheels by providing technical proof of the suitability potential of wire-based deposition welding processes as new repair methods.
Therefore, to achieve these goals, a holistic and automated standard repair process chain will be developed. Firstly, this will include the analysis of process parameters for defect-free build-up welding on railroad wheel materials. Moreover, quality assurance methods will be developed for the reliable detection of critical process and component defects. Finally, a feasibility test will be performed for the approval of the new repair process.
Thus, the repair welds will be tested under real conditions on the test stand and on the test track as it follows. Once the defects have been identified by metrological detection, the appropriate repair process is selected. To this end, the affected areas are first prepared by machining. As not only the geometry of the railroad wheels but also the material properties must meet the requirements, the repair areas are subjected to heat pre- and post-treatment, using LMD-w or WAAM. Next, based on the measured geometry of the wheels subtractive reworking is carried out, and non-destructive methods are used to ensure the quality of the repaired wheel.
At the end of the project, this procedure enables a technically sound statement to be made about the reliability of the additive repair process and the expected long-term stability. Additionally, the data generated during the metrological recording of the railroad wheel and quality assurance is recorded using digital technologies, enabling the automation and standardization of the process.
As a result, the project LEDA will develop a stable and reproducible deposition welding process for wheel repair, where defects on real railroad wheels are repaired using LMD-w and WAAM with the aid of process specific software. Finally, innovative methods of both destructive and non-destructive process and component monitoring, as well as concepts and strategies for automating the repair process chain will be developed to ensure efficient and reliable wheel repair. Overall, the use of such innovative technology will increase the efficiency of the repair processes and logistics capability and reduce the consumption of resources. As such, the associated cost reduction will lead to an increase in the competitiveness of rail transport, which will help to increase its market share.
Partners
Start: December 2023
End: November 2026