Funding agency: Bundesministerium für Wirtschaft und Klimaschutz (BMWK)/ Projektträger Jülich (PTJ)
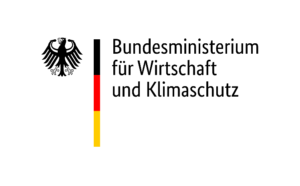
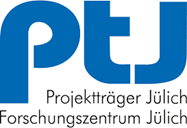
Project Number: 03LB3063D
The project “Digitaler Produktentstehungsprozess zur Auslegung von TFP-Preforms” is funded by the Federal Ministry of Economic Affairs and Climate Action (BMWK) and the Projektträger Jülich (PTJ) under the project no.: 03LB3063D.
Details
Tailored Textiles (TT) are a form of fibre-reinforced composites and bear great potential to reduce the weight of components as well as the use of material while simultaneously increasing the performance of components. Eventually, Tailored Fibre Placement (TFP), a manufacturing process for Tailored Textiles, has been developed. Tailored Fibre Placement is a variant of technical embroidery in which semi-finished products are produced through CNC-controlled variable-axis depositing of reinforcement fibres. The process is highly efficient but still challenged by medium-sized or small production batches and distortions of consecutive production steps. With these challenges, the advantages and potentials of lightweight construction remain unused. To change this, the project DigiPEP set out to develop a holistic and digitally connected product development process.
Tailored Textiles (TT) have already helped to reduce component weight and material used in production while simultaneously increasing the component performance for the use case of motorcycles. This efficiency leads to more sustainable product life cycles (PLC) and a reduction in production costs. The manufacturing process in which these improvements with Tailored Textiles (TT) are reached is called Tailored Fibre Placement (TFP). The process is a variant of technical embroidery in which semi-finished products are produced through CNC-controlled variable-axis depositing of reinforcement fibres.
The process is highly efficient, yet the component design and embroidery patterns in the form of machine code for Tailored Fibre Placement are a burden for industrial applications of smaller production batches. There are first steps for the design such as finite element analysis, path planning, models of failure, draping, and costs, but the parameters of the process steps influence each other, causing several distortions which require iterations of costly corrections. In current Tailored Fibre Placement processes, components cannot be efficiently produced regarding the cost, weight, and performance of each component. Thus, the advantages and potentials of lightweight construction remain unused.
Therefore, the aim of DigiPEP is to establish Tailored Fibre Placement in the German industry, especially for small and medium-sized enterprises to realize a material and resource-efficient lightweight construction. This will be done by preparing and validating a holistic, digitally connected product development process. The approach to implementation is model-based systems engineering (MBSE). For this, the value chain including construction, structural mechanics, textile technology, and production technology will be aggregated in the form of a system model and displayed in digital submodels. These submodels such as finite element analysis, strength model, path planning, and draping will be connected on the parameter level which allows a complete digitalization and consistency of data. The system model is suitable for production and optimized regarding costs, weight, and performance. This firstly requires the definition of relevant input and output parameters. It secondly necessitates a design model used for structural mechanics. Thirdly, production conditions need to be researched. Lastly, the forming behaviour needs to be transferred into a model. The developed efficient models can generate an optimized TFP concept within a short time.
The product development process of the project will be transmitted into a user-friendly graphical interface. The project’s results consist of the realization of a software-based, user-friendly algorithm which allows the design and production of material efficient components for the future. By this, resources in the form of material waste will be saved and lighter components will be produced, thus lowering carbon emissions.
The project is innovative in several ways. Previously, most research has been focused on thin-walled aluminum workpieces. The distortion behavior of bulky, forged, Ti6-4 parts are now researched in the project for the first time. Secondly, the project develops a new residual stress model to simulate initial residual stress in the workpiece, instead of destructive measurements like previous models that only focus on the initial residual stress. Building on this new knowledge, the project will gather information on how to correct predicted distortions by influencing the machining strategy. Moreover, the project will develop a closed-loop with distortion optimization logic that unties finite element analysis data with dexel-based CAM material models.
The result of the project is beyond state-of-the-art research that focuses on industrial relevant Ti6-4 materials, develops a novel residual stress simulation model, and defines distortion optimizing machining strategies that are not yet available to science and industry.
Partners
Start: May 2022
End: April 2024