ModuleWorks is at the forefront of multi-axis machining and simulation technology, providing the toolpath and simulation technology that powers many of the leading CAM systems around the world today.
With this latest release, ModuleWorks launches its new components for Fused Deposition Modeling (FDM). There are also new features for 5-axis, 3-axis and 2-axis machining, machine simulation, the MultiXPost post processor and the NC Editor.
Additive Machining
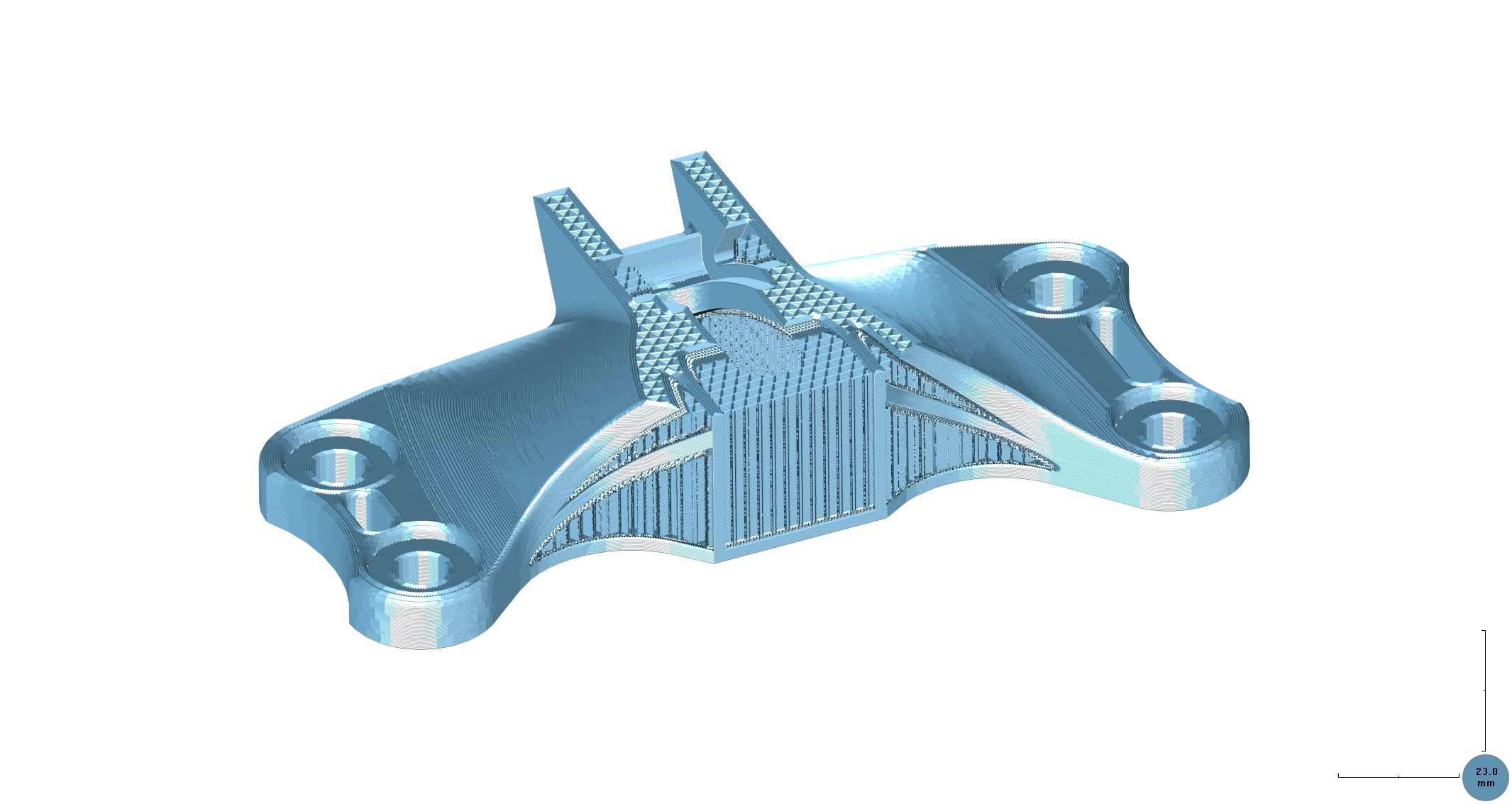
Fused Deposition Modelling
ModuleWorks now supports Fused Deposition Modelling (FDM). This is one of the most popular additive manufacturing methods, especially for plastics such as ABS and PLA, and it is currently one of the most cost-effective technologies for manufacturing 3-dimensional objects.
FDM works like a hot glue gun, where the object is printed onto a moveable and heated build plate. To ensure a high quality printed structure, ModuleWorks 2018.12 offers different infill patterns with a defined density and rotation angle that can be applied to each layer of the infill. A support structure can be created for overhangs and an additional brim layer can be used to provide extra adhesion to the plate. To check whether the nozzle is correctly calibrated and whether the material has been sufficiently heated, a skirt line can be printed around the model.
5-Axis Machining
Side tilt by contact point
This convenient new tilting option for 5-axis machining lets you define tool axis tilting by specifying a contact point on the tool profile. This significantly simplifies operational setup, especially for tools with complex profile geometries, such as barrel tools. Users can specify a static contact point or a dynamic range, allowing the contact point to change along the contour.
Automatic tilting for barrel mills
The blending distance option provides even more control by adding orientation points in the event of a collision.
2-Axis Machining
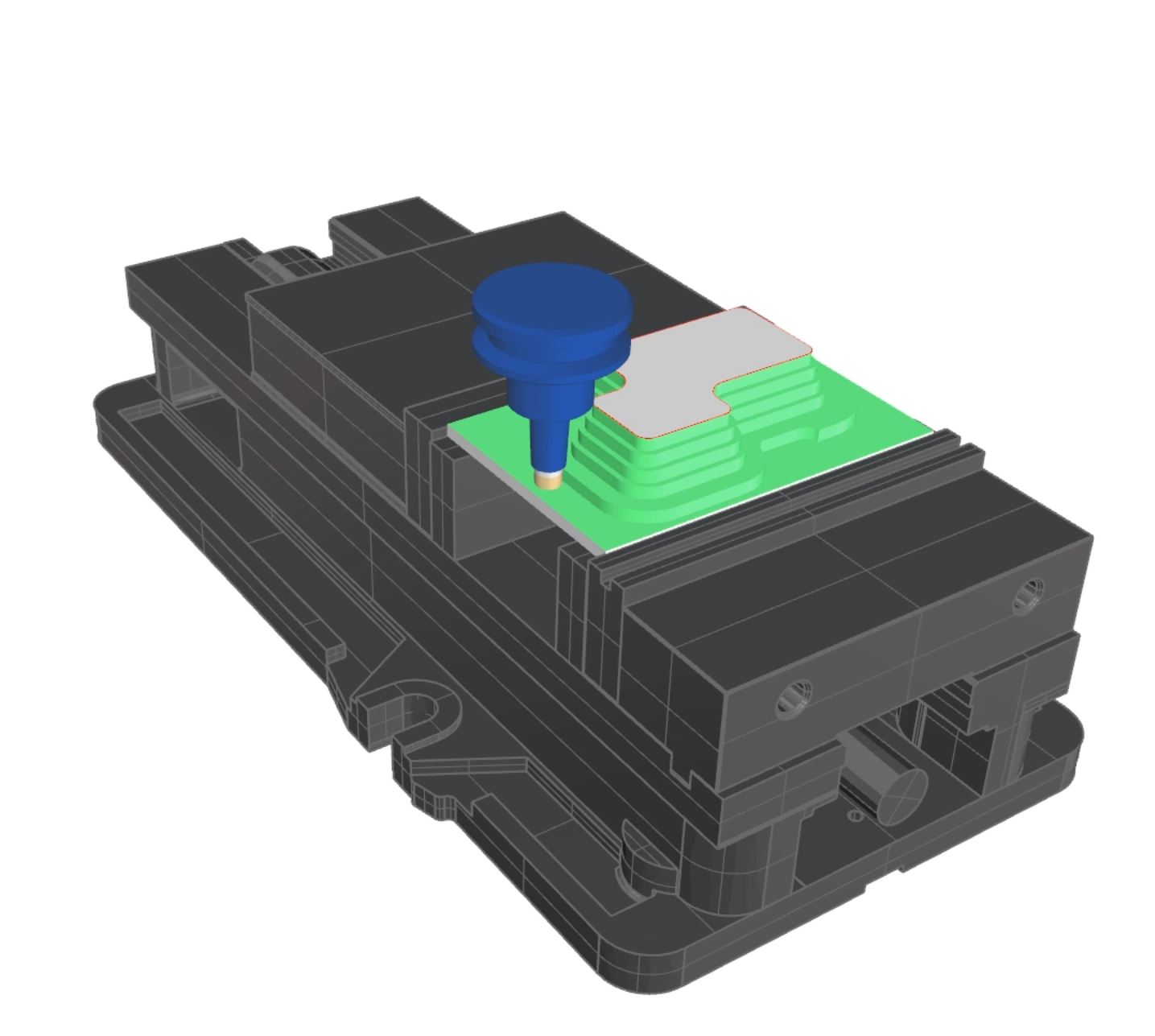
Dynamic holder collision avoidance for 2-axis roughing
To enhance machining safety and productivity, this new feature takes the shape of the holder and arbor into consideration during the toolpath calculation to avoid collisions between the entire tool and stock material.
3-Axis Machining
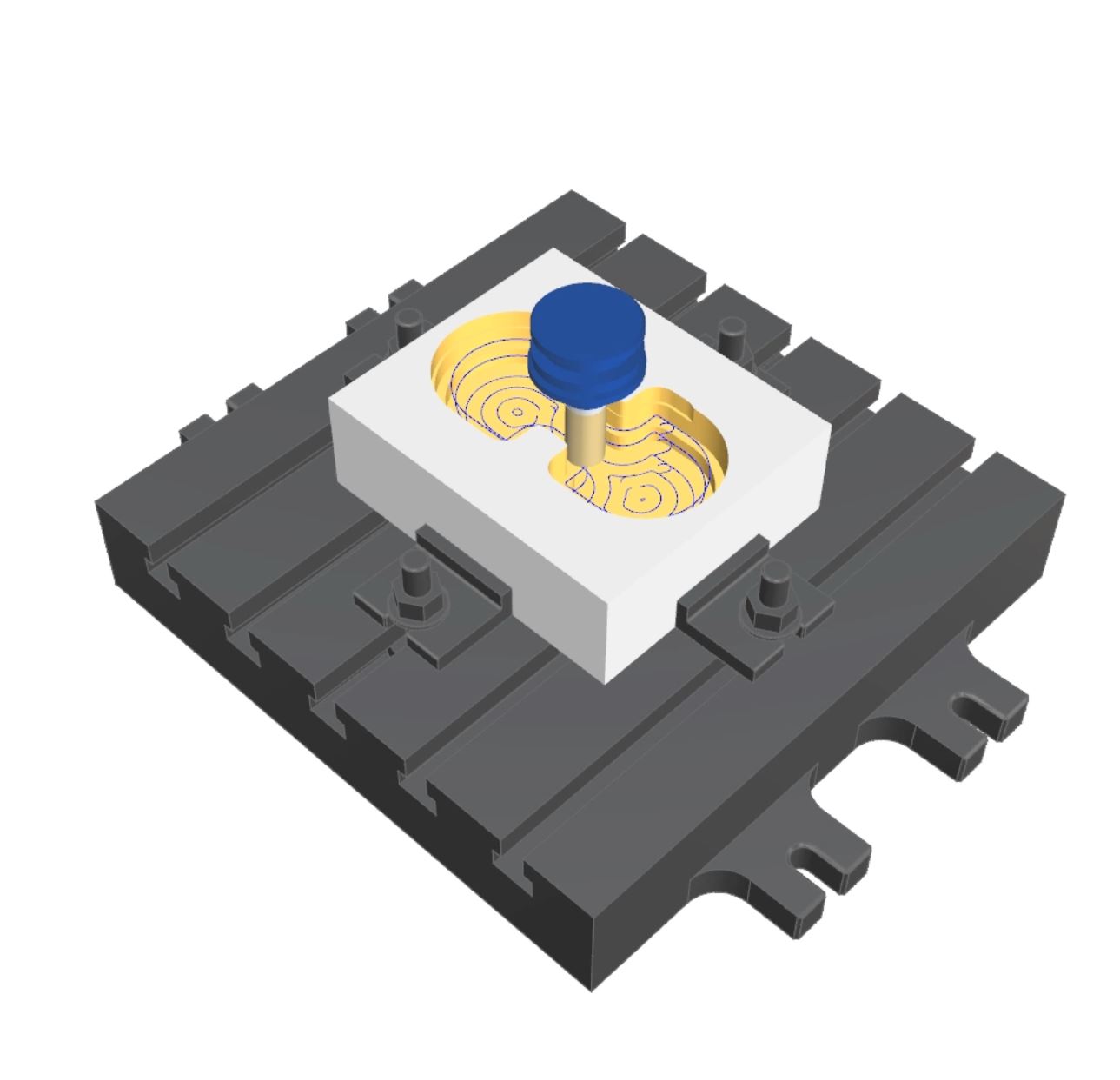
Intermediate slices filtering for 3-axis roughing
This time-saving feature eliminates machining of very thin slices that result from the cusps left over by the previous operation. The user-defined threshold lets you avoid these unnecessary toolpath segments to speed up the machining process and increase productivity.
Machine Simulation
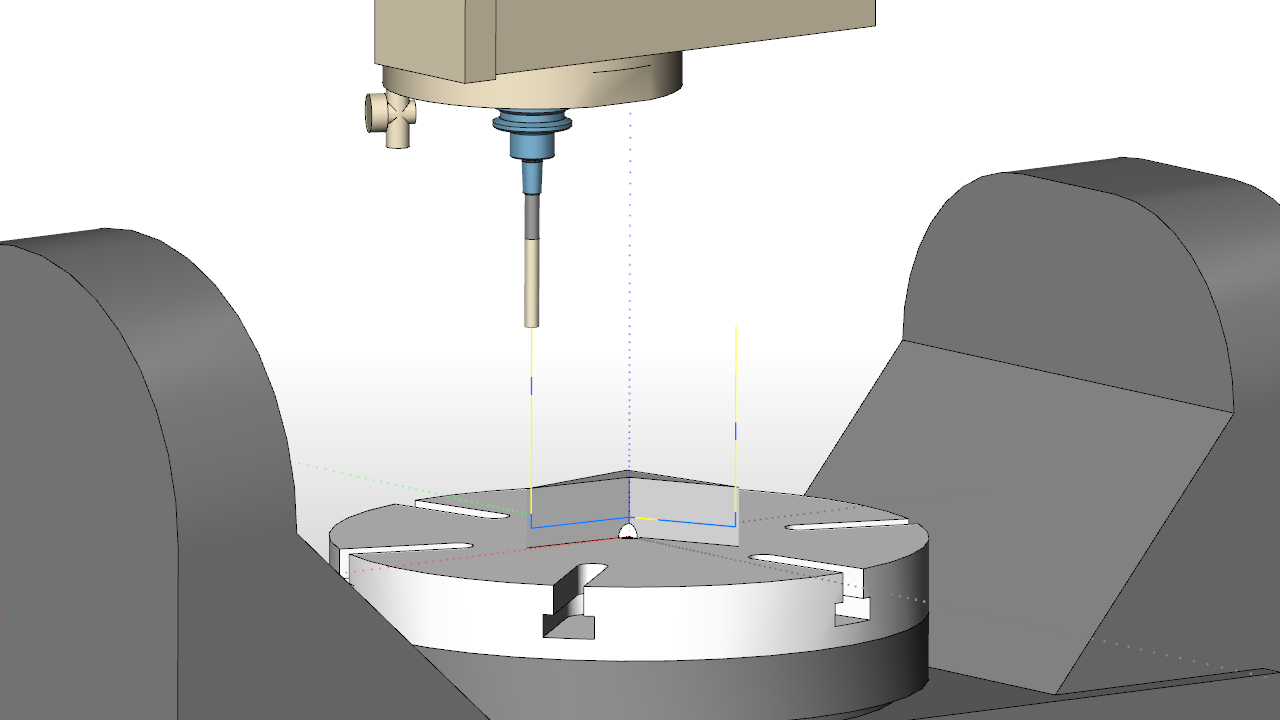
New simulation controls
New options have been added to the Machine Simulator to give users more control over the simulation process. You can now step forwards and step backwards to the next/previous feed move, jumping over (fast simulating) the rapid moves.