All-in-one Pelton Wheel
Pelton wheels are the driving force of the hydro-power industry, extracting energy from fast-flowing water to generate electricity. But manufacturing a Pelton wheel is a challenge. Due to the wheel’s complicated design, the impulse blades are usually machined separately and then mounted onto the rim, which is time consuming and adds to the production costs.
In a new collaboration project, Okuma and ModuleWorks have devised a solution that enables the entire Pelton wheel to be machined from a single block of metal. This new procedure accelerates production and reduces manufacturing costs.
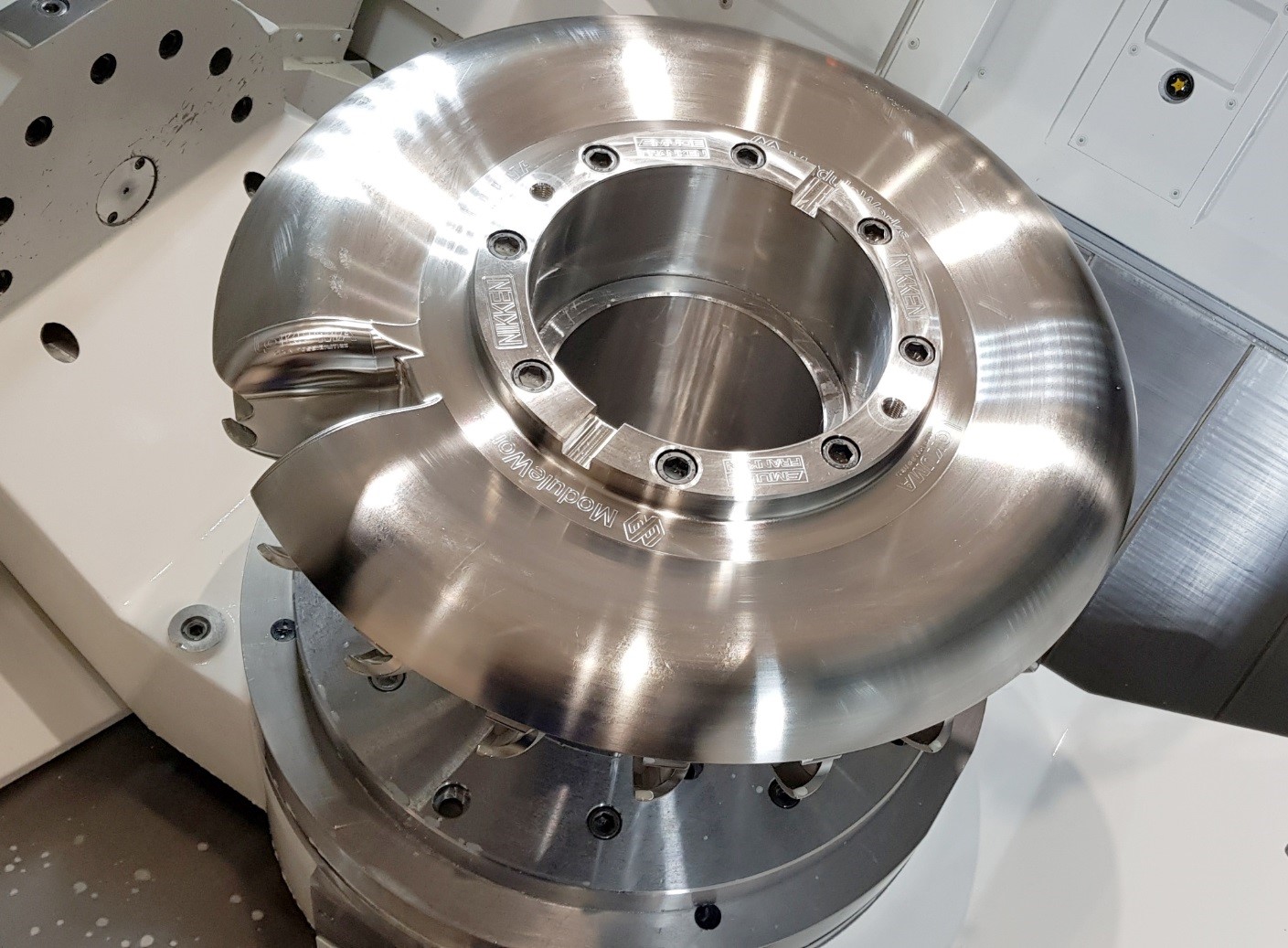
Machining a Pelton wheel from a single workpiece
The challenge - reaching the places other tools cannot reach
Machining a Pelton wheel from a single workpiece is notoriously difficult. The bucket-shaped impulse blades are situated close together and taper towards the rim of the wheel, which makes it extremely complicated for the cutting tool to navigate between the blades without causing a collision. There are also special demands on the surface quality and topological precision of the organically shaped blade cavities to ensure they extract the maximum amount of energy from the water.
On top of this, Pelton wheels are big and heavy and soon stretch the physical limits of the machine. This makes it difficult to machine an entire wheel in an efficient and economically viable way. To do so, the machine tool must be able to navigate around the whole workpiece in a highly dynamic motion to efficiently cut the wheel and perform high-speed 5-axis collision-free cutting to shape the blades.
To offer Pelton wheel machining on its MU-V series of machining centers, Okuma soon realized they would need technically sophisticated toolpath generation and simulation software to master the special technical challenges. This is why Okuma and ModuleWorks teamed up to find a solution.
The solution - 5-axis machining with high-quality patterns
Advantages:
- One-off machine set up Advantages
- Faster machining
- Higher profitability
- New machining possibilities
To overcome the sheer physical limitations, the wheel is machined in two stages. One half of the wheel is machined and then the workpiece is turned 180 degrees to enable the tool to reach the other half. The industry-proven ModuleWorks triangle mesh roughing components were used to cut the rough shape of the Pelton wheel.
For creating the bucket-shaped blades, the ModuleWorks adaptive roughing strategy uses consistent toolpath engagement and a smooth toolpath motion to generate an impressive dynamic pattern and high-performance roughing process that reduces the overall costs of producing non-prismatic shapes. For optimal finishing, ModuleWorks geodesic machining delivers a high-quality finishing pattern and comes with advanced features for producing rounded corners using a morph or constant stepover pattern. This enables Okuma to meet the high demands on the workpiece to ensure optimal energy transfer from the high-pressure flowing water.
ModuleWorks 5-axis calculation strategies also extend the reach of the tool to provide enhanced tilting strategies on complex workpiece geometries and areas with deep grooves. This makes the strategies ideal for machining the narrow areas between the impulse blades and enables the machine to work efficiently with the heavy workpiece to perform toolpath moves that optimize productivity and ensure an economically viable product. Combining the special toolpath generation strategies with the advanced tilting and collision avoidance algorithms extends the reach of the tool to its full limit to successfully navigate the extremely tight spaces.
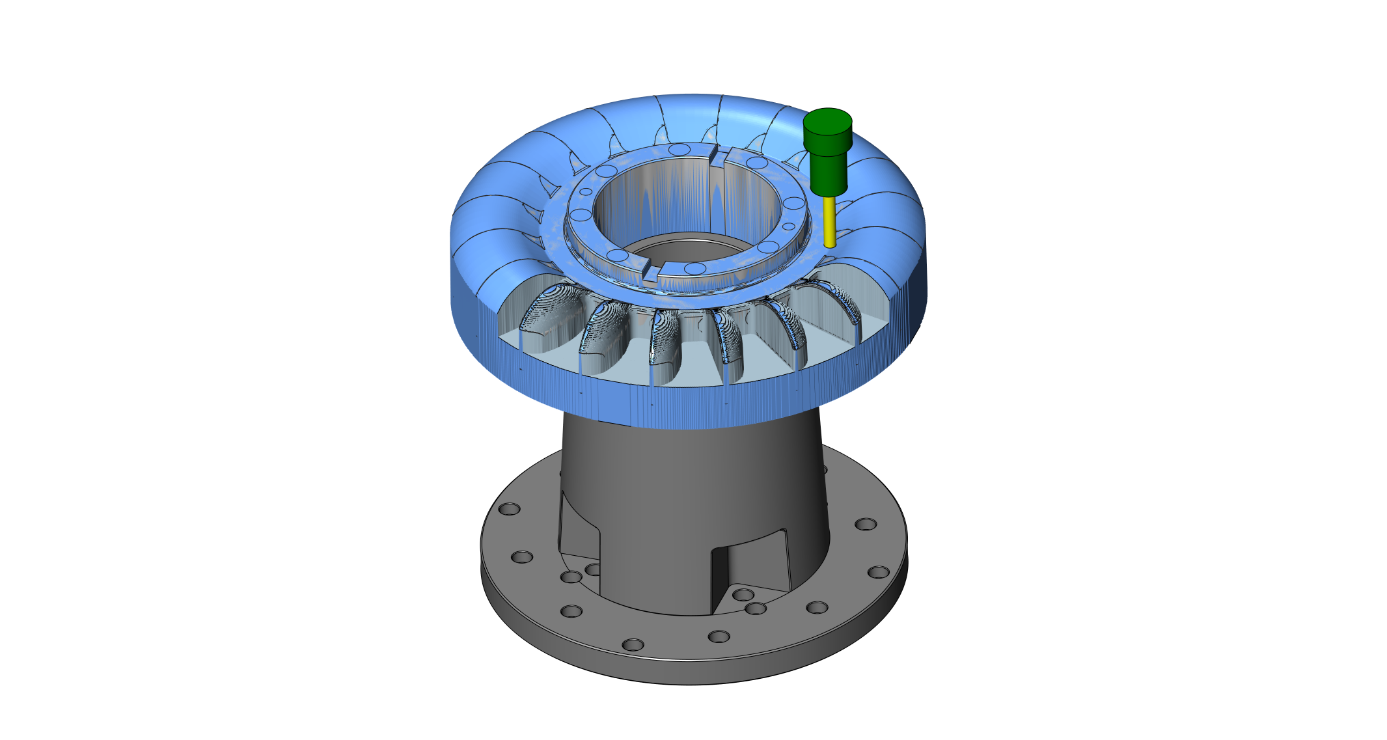
3D Kinematic simulation of Pelton wheel machining
Gouge-checking during the toolpath calculation followed by full 3D kinematic machine simulation ensure the validity and accuracy of the toolpath before machining. Behavioural analyses of the segment length, feedrate and height allow the toolpath to be refined for optimal finish and quality. Moreover, because the wheel is machined from a single workpiece, simulation and machine set up only need to be performed once, which further increases the efficiency and cost-effectiveness of producing the wheel.
Summary - new machining possibilities
A special combination of adaptive roughing, geodesic and classical machining strategies cracks the challenge of the Pelton wheel and opens new machining possibilities by extending the reach of tools for safe operation in extremely tight areas. For Pelton wheel machining it means new design options by using new, innovative machining processes that boost productivity and cost-effectiveness.
Live Pelton Wheel Machining at EMO 2019 in Hannover:
Okuma will present a live demonstration of Pelton wheel machining on the Okuma MU-8000V 5-axis vertical machining center (Hall 27, stand D26).
ModuleWorks will demonstrate the Pelton wheel machine simulation (Hall 9, stand E01).
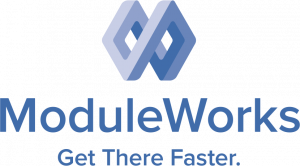
ModuleWorks is the leading software component provider for the CAD/CAM industry. With over 170 employees and 700 man years of software development, ModuleWorks’ expertise in toolpath creation and simulation is recognized throughout the industry and its software components are integrated in over 500,000 installed seats of CAD/CAM software around the world. From standard products to exclusive development projects, we work closely together with you to bring your own vision of Industry 4.0 to life. Our comprehensive product portfolio and cutting-edge software components enable you to optimize your CAD/CAM solutions and connect to CNC/MTB systems to increase your competitiveness and help you Get There Faster.
About
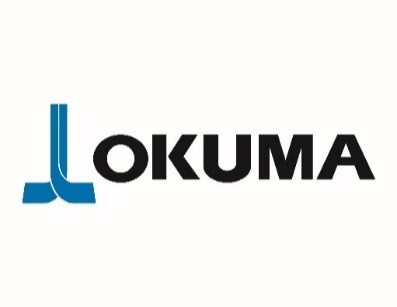
Okuma Europe GmbH is the Germany-based sales and service affiliate of Okuma Corporation, a world leader in CNC (computer numeric control) machine tools, founded in 1898 in Nagoya, Japan. The company is the industry’s only single-source provider, with the CNC machine, drive, motors, encoders, spindle and CNC control all manufactured by Okuma. Okuma’s innovative and reliable technology, paired with comprehensive, localised service protection, allows users to run continuously with confidence – maximising profitability. Along with its industry-leading distribution network, Okuma facilitates quality, productivity and efficiency, empowering the customer and enabling competitive advantage in today’s demanding manufacturing environment. For more information, visit www.okuma.eu .