As machining processes become more and more sophisticated, the risk of collisions between the tool, workpiece and machine components increases. Collisions mean costly downtime and cause expensive damage to the workpiece, spindles and sometimes even the whole machine.
Most CAD/CAM vendors provide simulation software to check the toolpath for collisions before it is sent as NC code to the machine. But there is no guarantee that the real machine behaves exactly like the simulation. This is why more and more machine manufacturers are implementing additional, real-time collision detection on the CNC controller.
The ModuleWorks Collision Avoidance System (CAS) is real-time collision avoidance software especially designed for fast and seamless integration into the latest CNC controllers. It is connected to the CNC’s look-ahead buffer to receive data directly from the NC interpolator. This eliminates the need for parser maintenance and ensures a realistic simulation that is analyzed for collisions in real-time. Because it runs on the controller, ModuleWorks CAS takes the real axis positions, machine geometries and workpiece position to provide full-scene verification and clash detection during the milling and turning process in all operating modes, including jog mode, to minimize the risk of expensive machine damage and downtime and optimize the machining process.
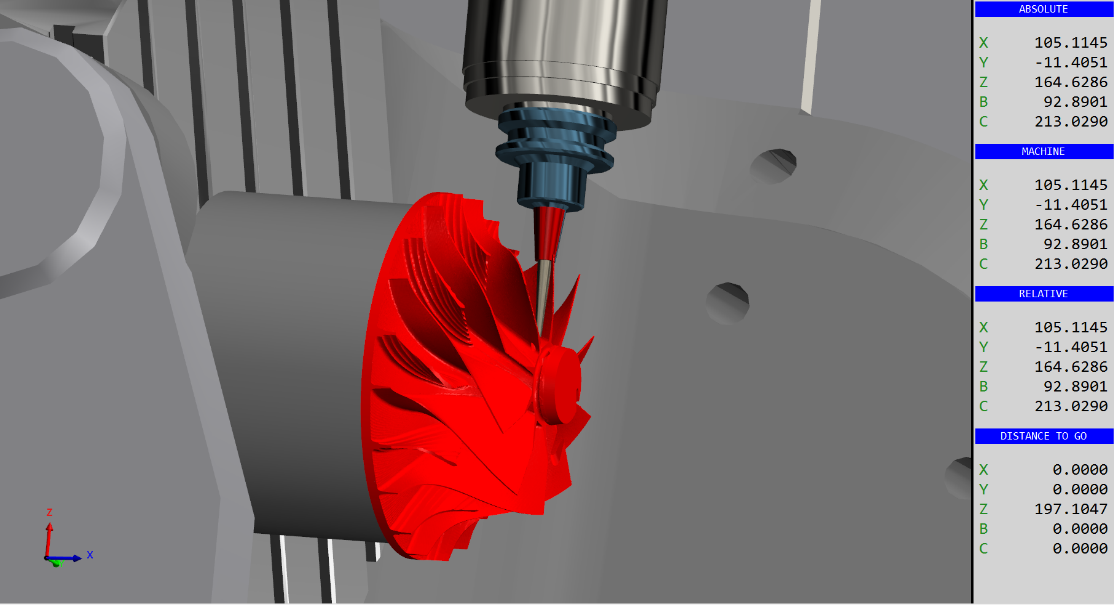
Real-time behavior is possible even on non-real-time operating systems thanks to the look-ahead buffer provided by the CNC core. This enables asynchronous collision checking which allows for the jitter that is experienced on standard operating systems.
If the performance of your CNC processor is limited, there are measures you can take to accelerate the performance of the simulation to achieve real-time response. For example, you can minimize the amount of mesh data and use bounding volumes to reduce the amount of checks.
There are also techniques specific to the CPU and hardware configuration that can significantly boost the real-time performance of CNC simulation and collision checking. ModuleWorks has been involved in many successful integration projects for CNC simulation technology, and we have gathered strong experience with different hardware / platform combinations ranging from small-scale ARM based CPUs up to standard desktop based x86 compatible CPUs with high TDP thermal allowances. This experience helps us advise our partners on how to fine-tune the simulation parameters to give an optimal user experience across a variety of platforms.
One of the first companies to use the ModuleWorks CAS is Huron. The ModuleWorks CAS is integrated into the Huron PreciPROTECT collision avoidance system. The ModuleWorks components run directly on the Siemens Sinumerik 840D SL CNC control and enable Huron to provide real-time collision avoidance for its new K3X8-Five and 0KX50L 5-axis vertical machines.
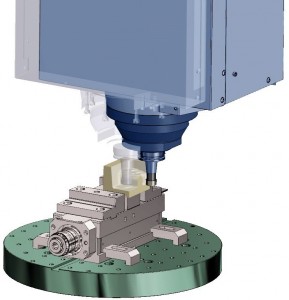
The Huron PreciPROTECT system on the Siemens Sinumerik 840D SL CNC control.
To find out more about the ModuleWorks CAS and how we can help you get the most out of your real-time CNC simulation, please get in touch with us.
About ModuleWorks
ModuleWorks is a software component provider for the CAD/CAM/CNC industry. ModuleWorks’ expertise in toolpath creation and simulation is recognized throughout the industry and its software components and development services are used by the majority of the leading CAM vendors for industry focused solutions across diverse business sectors. Already integrated on leading CNC controllers, ModuleWorks CNC Simulation brings advanced real-time simulation and collision avoidance to the shop floor.