Funding agency: Ministerium für Wirtschaft und Klimaschutz / Projektträger Jülich
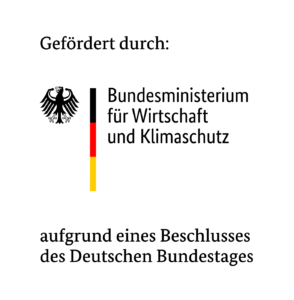
Details
Thin glasses are very versatile and therefore used for different technological items. This led to a steep increase in the markets demands but the problem of thin glasses is that they require either a production that is high in energy or high in temporal effort. To solve these problems, a nonthermal forming process has been developed at the IPT. The new process is environment friendly and time efficient and now has to be amended to the requirements of real industrial production.
Thin glass is ever present in entertainment technologies such as phones, tablets or TV screens. It is also important for other glass surfaces in cars, sensors and buildings. About 70 % of these thin glass structures are provided with functional layers or structures to create a specific haptic or add functionalities such as water resistance and anti-reflection. Due to these various fields of application, the market demand for thin glass is already high and currently rising.
But there are environmental and economic issues to its production: forming the glasses by conventional methods does either require a huge amount of energy or a huge amount of time. Additionally, functional layers or structures are either created through etching with environmentally hazardous substances or through structured mould inserts with a low tool life.
An alternative to energy or time consuming forming processes is a non-isothermal process that has been developed at the Fraunhofer IPT recently to resolve these problems. For this, the preheated glass is placed on the much colder mould and heated together with it in the oven. Because of the significantly lower mass, the glass heats up to the forming temperature a lot faster and can be formed directly. After this, the hot glass is removed from the colder mould and exposed to an external cooling process. The key innovation of the process is the separation of heating and cooling phases from the moulding process with the resulting temperature gradient between glass and mould.
In the case of non-thermal glass forming processes, functional layers or structures require a 2D surface and are therefore added before forming. Since these structures will get distorted, a digital model to compensate deformation is required. The compensation model is the foundation of the tool path. Once this is done, the non-thermal forming can begin to produce thin glass.
To satisfy market demands and to enable an environment-friendly production, the project “EffF3D” is researching the upstream functionalisation of thin glass by laser structuring with a subsequent non-isothermal glass forming process. Non-isothermal glass forming increases material and resource efficiency when compared to alternative forming processes. This is due to high tool life and cycle times. Thus, the new process chain allows a thin glass that can reduce energy consumption by 67% and the CO2 emissions by 63%. What is more, the novel approach to thin glass production is able to satisfy the increasing market demands for thin glass with lower economic and environmental costs.
Given these potentials, a prototypical laser and forming production system will be developed. This system considers realistic industry requirements and is able to be adapted for more specific applications through new projects. ModuleWorks’ specific task in the project is to develop a digital model to compensate distortions during forming processes.