Funding agency: EIT Manufacturing
Project Number: TBA
The project CAMplus4.0 is funded by EIT Manufacturing.
Details
A common problem for CAM companies is the lack of skills with the additional lack of trained personnel to drive automation to the next level. With this lack, opportunities for productivity improvements and competitive advantages remain unconquered. The aim of the project CAMplus4.0 is to close the skills gap by developing an interactive training program for professional manufacturing engineers, empowering them in the field of advanced CAM and NC code simulation and optimization methodologies. As result, manufacturing companies can expect further advances in areas such as small batch size productions, scheduling opportunities, machine equipment, and resource efficiency.
The motivation for the project is the importance of CAM technology on one hand, as is well established in the industrial field for fast and efficient NC code generation in both subtractive and additive technologies. On the other hand, many companies, and small and medium-sized enterprises, in particular, are lacking the required skills and trained personnel. This gap limits possibilities to further drive automation and optimization of productivity and competitiveness.
Starting from this as a motivation, the aim of CAMplu4.0 is to close this identified skills gap by developing an interactive training program for professional manufacturing engineers, to empower them in the field of advanced CAM and NC code simulation and optimization methodologies. The project specifically focuses on opportunities through FEM simulation tools, advanced CAM add-on algorithms, and the utilization of sensor data. This training will enable engineers to leverage improvements on their shop floor, which have so far not been accessible via standard CAM functionalities. This leads to an increase in resilience, digitalization as well as the reduction of processes and material waste.
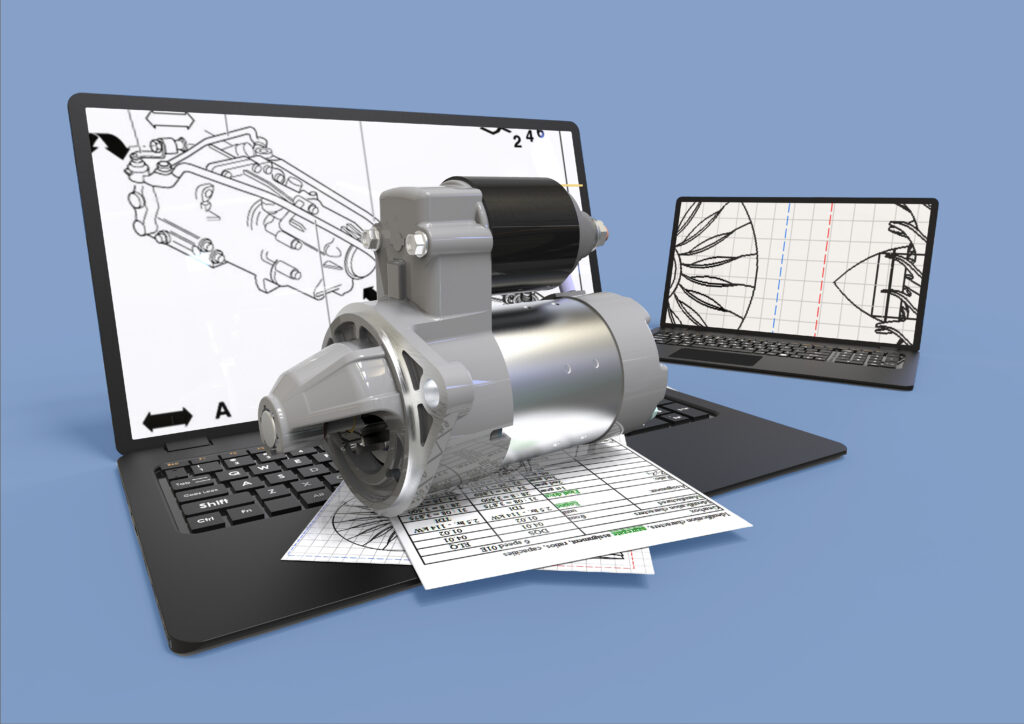
The project starts with a requirement analysis, interviews, and details on the training concept. In a next step, training nuggets or learning paths are developed and a visual twin is implemented in a laboratory. Once this is done, pilot training with professionals from the industry start until the project results are finally disseminated.
The result of the project will be major improvements for manufacturing companies. These include, but are not limited to, improvements in smaller batch size productions, flexible scheduling opportunities, higher utilization of machining equipment, less waste in materials and processes, make-to-order production setups, production of high complex shapes and materials, and the minimization of downtimes or interruptions.
Partners
Start: January 2022
End: December 2022