With increasing demand for medical equipment, lighting solutions, and security and surveillance systems, the need for high-quality optical components-such as Fresnel lenses, prisms and optical mirrors-has grown significantly.
Major Challenges
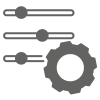
Need for Customization
Meeting the demand for customized optical solutions is challenging without advanced manufacturing technology. With a diverse customer base and high-volume requirements, addressing mass demand often becomes complex.
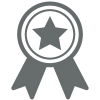
Achieving High Quality
The optics industry must uphold stringent quality standards to ensure sustainable manufacturing. Traditional practices struggle to meet modern precision and quality demands, and the cost of poor quality can significantly impact production efficiency.
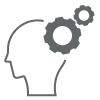
Scarcity of Skilled Labor
The scarcity of skilled labour in the optics industry underscores the need for automation to handle daily production efficiently.
Solution Offered by ModuleWorks
The ModuleWorks Optics package precisely computes toolpath positions by leveraging accurate mathematical representations of the workpiece geometry. It works directly with hybrid inputs in a single 3D CAM solution. In addition to ensuring the accuracy of individual tool positions, it effectively addresses challenging geometric configurations, such as non-tangential contacts with surface edges and scenarios involving dual or multiple contacts.
This solution incorporates Ultra-Precision Machining (UPM) features specifically designed for optical components, supporting processes such as grinding, diamond cutting and fly cutting.
Key Features
The ModuleWorks Optics package for ultra-precision machining works with diverse types of surface forms including solid BREP, NURBS, parametric surfaces, and point cloud data. This generates more accurate toolpaths without relying on mesh approximations. Integrating the ModuleWorks parametric surface library enhances OEM solutions with a wide range of pre-defined formulas: Flat, Sphere, A sphere, Torus, Radial Polynomial, XY Polynomial, Zernike Polynomial, Sine and Revolved Curve as well as various parametric surface operations: Translation, Tilt, Rotate, Trim, Combine, Multi-Surface Grid and Diffractive.
Ultra-precision spiral toolpath calculations are essential for 2D and 3D optical machining of lenses, moulding tools and lens arrays. These calculations utilize optical machining patterns based on NURBS, analytical formulas, or point clouds, enabling precise micro-adjustment of toolpaths through a measured grid. Additionally, the calculation employs an ultra-precision zig-zag pattern for fly-cutting optical components and supports a variety of grinding patterns for operations such as roughing, drilling, chamfering, slotting and contouring.
Simulating multi-axis setups, including spindles and heads, ensures precise machining of complex parts while providing high-speed visualization of complex toolpaths. This process allows for thorough verification of the toolpath quality prior to production, enhancing overall efficiency and accuracy.
The toolpath calculation is performed in a 3D neutral space, utilizing the ModuleWorks Post-Processor Framework (PPF) to deliver machine-optimized output. This enables ultra-accurate, high-speed post-processing of millions of toolpath points, ensuring optimal performance and precision of machining operations.
Key Highlights
Enhanced Performance
Multi-threading uses the highest precision 64-bit algorithms for ultra-fast calculation of machine-adapted toolpaths, leveraging cutting-edge 3D technologies for machining optical components. This unified approach accommodates all types of optical parts, allowing seamless integration of conventional CAM technologies with specialized optics toolpaths for efficient machining of the desired components.
Process Configurations
Ultra-precision machining supports a wide range of process configurations, delivering a comprehensive end-to-end solution. With customized tool support, users can effectively machine even the most complex geometries.
- Turning (slow & fast tool)
- Milling
- Fly cutting
- Grinding & Polishing
- Drum machining
- Diamond ruling
Automation Framework
Automation Framework empowers users to program parts with greater efficiency, significantly reducing production time while maintaining high precision. The Feature Aware Manufacturing Core allows users to automate and efficiently program even complex parts.
With Manufacturing Application Development Framework (MADF), users seamlessly transfer pre-defined manufacturing workflows into fully functional end-user applications. This framework enables customers to rapidly develop customized manufacturing applications tailored to their specific needs.
Key Benefits

Advanced multi-threading 64-bit algorithms deliver ultra-fast calculations for machine-adapted toolpaths, enhancing production efficiency

Optical machining patterns, based on NURBS, analytical formulas, or point clouds, significantly enhance process accuracy

Comprehensive support for a wide range of processes including turning, grinding and milling

Highly intuitive workflow ensures shorter learning curve

The contact-point-based feedrate ensures smooth cutting, improving surface quality

Secondary drive surface offers greater flexibility for enhanced tool axis control
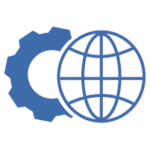
Conventional CAM strategies (drilling, roughing, chamfering etc.) can be combined with UPM cycles
