Robots are playing a key role in the implementation of Industry 4.0. From manufacturing to assembling complex parts, robots are now essential for various industrial applications/processes. Robotic technologies are efficient, automated, and safe as well. To support the implementation of robotic technologies, ModuleWorks offers Robotics SDK, a solution that addresses the requirements of organizations developing software solutions used with a robot. This includes CAD/CAM software developers, robot integrators, and robot OEMs that are planning to enter the robotic market, as well as organizations using robots for specific industrial processes/applications such as welding, Wire Arc Additive Manufacturing (WAAM) and Direct Energy Deposition (DED).
Major Challenges
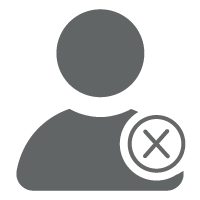
Need for Easy to Learn/Use Solution
Simple tasks can still be effectively handled with manual robot programming, but as the complexity of parts or processes increases, manual methods become inefficient and error-prone. Moreover, manual programming is time-consuming and dependent on operator skills, making it difficult to scale operations.
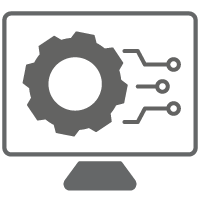
Ensuring Safe Operation
Technological advances in safety measures enable today’s collaborative robots to work safely alongside humans. However, manual programming increases the risk of human error, which can lead to unsafe robot movements and potential collisions. Additionally, the most advanced technology for ensuring safe robot operations, is not always available for most robotic systems due to higher costs or compatibility issues, making it difficult to integrate with certain robots.
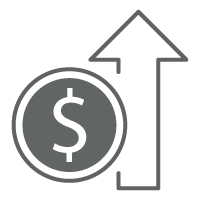
High Costs for Workpiece Planning
The time required for manual programming results in higher downtime, affecting overall production efficiency and increasing operational costs. Moreover, a skilled operator may be needed for manual programming, leading to higher labor costs.
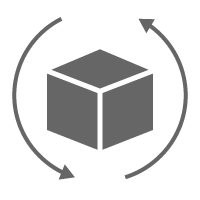
Process Complexity
As the complexity of certain processes or applications increases, manual teaching may no longer be feasible as complex processes often involve multi-axis movements and intricate sequences that are challenging to program without advanced tools.
Solution Offered by ModuleWorks
ModuleWorks complete Robotics package comprises a kinematic solver MultiXPost (MXP Robots), a Machine/Robot Simulation, and the Post Processor Framework for generating NC-Code. Via API integration, the system can run in the background to transform a calculated toolpath into robot NC-coordinates. This enables seamless and automatic offline planning for complex multi-axis toolpaths.
Robotic Components
MultiXPost Robots
Fast, multithreaded kinematic solver for inverse and direct robot kinematics to convert collision-free CAD/CAM toolpaths to your robot’s tool coordinate system.
- Support for 4-6-axis robots, along with workpiece positioners, gantry systems, and additional mechanisms such as grippers
- Cooperating robots in one machine model
- Automatic synchronization of any additional axis, such as workpiece positioners
- Configurable motion constraints and optimizations
- Advanced features such as retract and rewind for computing optimal robot trajectories
Simulation
The Machine Simulator lets you visualize the robot‘s motion and check for potential collisions.
- 3D visualization of the full robot, including toolpath, robot components, fixtures, and workpiece
- Supports both subtractive and additive manufacturing process simulation
- Toolpath statistics, such as reporting motion point collisions and highlighting colliding parts
- Axis motion sliders for jog mode
- Kinematics tree editor
- Open XML format for robot definition
Post-Processor Framework
The Post-Processor Framework (PPF) uses a custom post-script to generate NC-code from the output of e.g. the MW kinematic solver or any other source. PPF can run on a network server and on any operating system that supports Python.
- Flexible scripting for any controller or output format
- Streaming of the output to any device or machine
- Fast NC-code generation
- Open kinematics format definition via ModuleWorks MXP
- API integration interface
- Programming in Python
Industry Applications
- Wire Arc Additive Manufacturing (WAAM)
- Direct Energy Deposition (DED)
- Deburring
- Laser Cutting
- Glue Deposition
Key Benefits

Enhanced precision and versatility of the robotic systems using ModuleWorks’ kinematics solver, which supports complex kinematic calculations for 4-6-axis robots, including additional axes
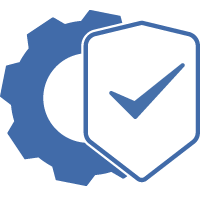
Safe path planning using ModuleWorks’ techniques for automatic collision avoidance
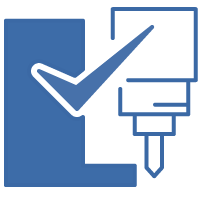
Robust collision detection, singularity handling, and axis-limit checks integrated into the complete kinematic chain, including additional axes, to prevent collisions and equipment damage
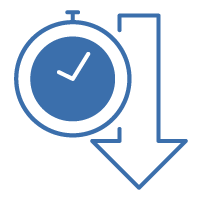
Reduced programming time and increased operational efficiency using an automated production-ready robotics package
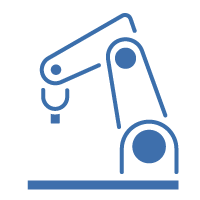
Accurately program and predict the robot's behavior and its interaction with the environment for even the most complex processes
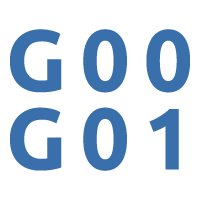
Improved overall productivity through generation of effective NC code, eliminating the need for manual teaching or editing
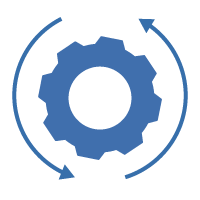