Additive & Process Technologies
To realize the full potential of the world’s manufacturing technology, to drive a new era of development, manufacturing and productivity.
Additive Manufacturing
To create new business models through industrialization of additive technologies.
Hybrid Manufacturing
Industry-proven SDKs for Developing Additive and Hybrid Software Solutions.
Adaption to Market Disruptions
Additive manufacturing technologies are quickly evolving to the point where they already make a huge impact on the market. This rapid advance will lead to wide scale adoption of these technologies over the next few years. The increasing demand for additive manufacturing combined with technology differentiation will force companies to accelerate their time-to-market to meet the needs of end users.
For companies that build 3D printers, robots, machines as well as software solutions for additive or hybrid manufacturing, market adaption will generate pressure to reduce machine programming complexity, leverage operator profitability and automate the entire production workflow. Investments in product development also need to be durably targeted.
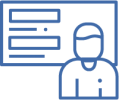
Skills Gap
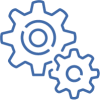
Machine Complexity
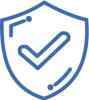
Machine Availability

Machine Connectivity
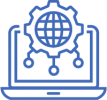
Digital Enabled Business
Services
The Additive and Process Technologies Business Area develops solutions and services that go beyond the technical state of the art. Our toolpath and simulation components enable rapid adoption of additive and hybrid manufacturing technologies and are optimally integrated into the customer’s environment to solve the productivity challenges facing additive, robotics and ultra-precision manufacturing.
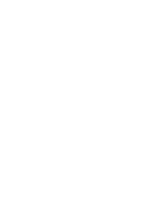
Tailored Post-Processors
ModuleWorks delivers bespoke NC-code post-processors tailored to meet the specific requirements of any additive and ultra-precision machining process. The post-processor can be implemented with open-source Python scripts based on the ModuleWorks PPFramework system.
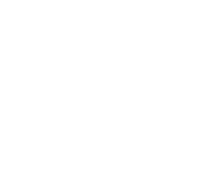
Machine Release Tests
To support complicated machining processes and release tests, ModuleWorks creates special machine simulation models and NC-programs for specific tasks.
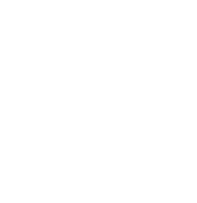
Software Integration
Services
The dedicated ModuleWorks integration team helps customers integrate all software components quickly and efficiently to accelerate time-to-market and maximize their return on technology investment.
Solution Portfolio
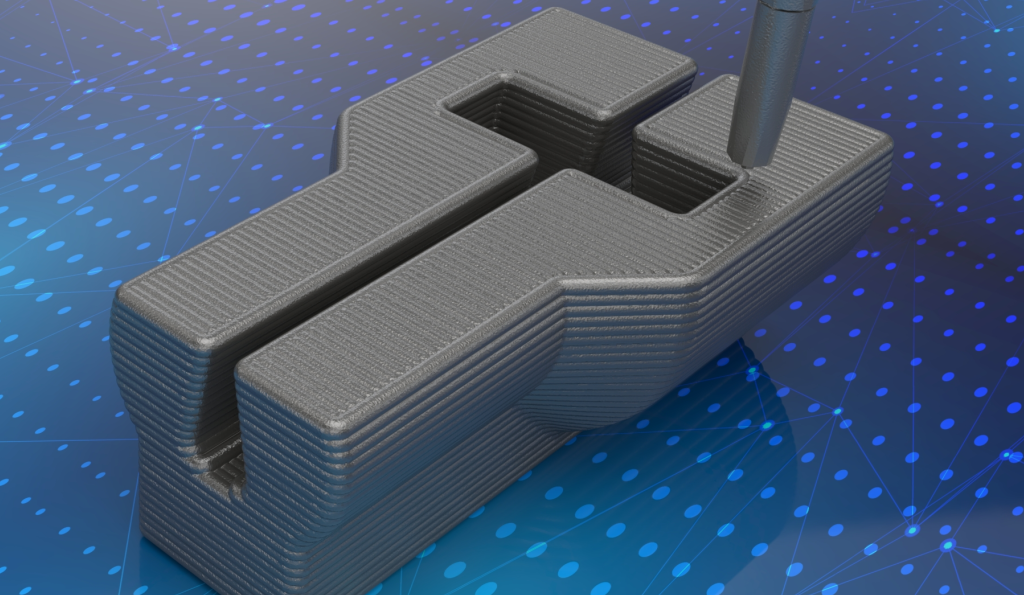
Wire Arc Additive Manufacturing
ModuleWorks Wire Arc Additive Manufacturing (WAAM) incorporates a toolpath planning algorithm specially designed for complex geometries and customized structures. The algorithm optimizes the manufacturing of near net shape geometries for different welding processes. Process parameters such as welding speed, current, voltage, wire feed, or powder speed can be defined to achieve a specific wall width/height (multi-layer) with maximum deposition efficiency.
Direct Energy Deposition
ModuleWorks Direct Energy Deposition (DED) incorporates a toolpath planning algorithm specially designed for complex geometries and customized structures. Process-critical parameters for the part can be accurately controlled and adapted to achieve a specific wall width/height (multi-layer) with maximum deposition efficiency, resulting in near net shapes that requires minimum post-processing.
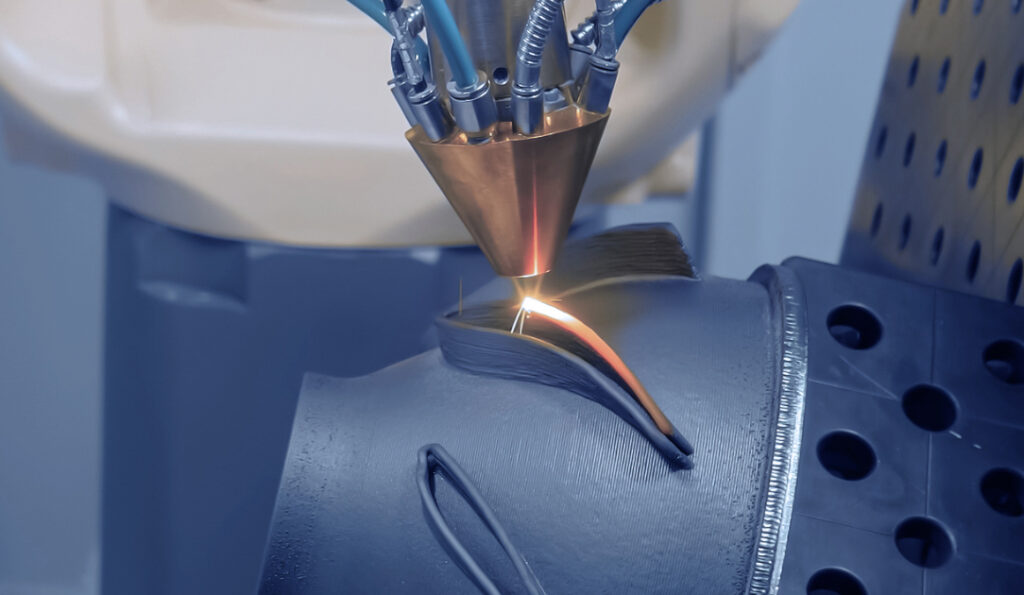
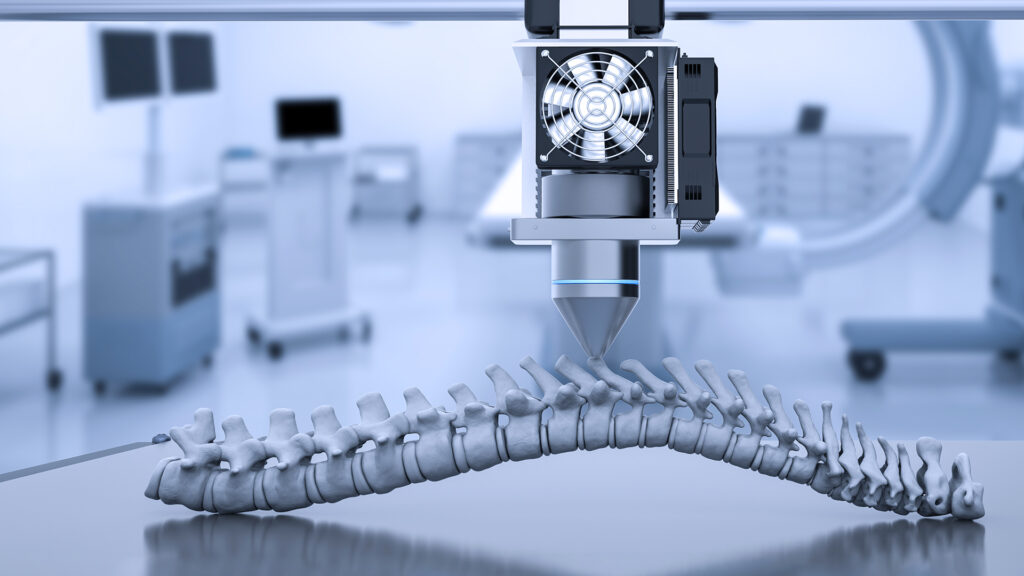
Polymer Printing
The Polymer Printing calculation core supports a wide range of applications, from desktop Fused Filament Fabrications (FFF) to Big Area Additive Manufacturing (BAAM) carbon-based component production or concrete printing.
This makes it easier to master complex challenges in these demanding environments and provides the flexibility to calculate toolpaths for complex freeform geometries and freely configure sub-components, such as print patterns in the infill and support areas.
Powder Bed Fusion
The ModuleWorks Powder Bed Fusion (PBF) software library enables quick and easy development of advanced, all-encompassing PBF solutions. It delivers high-performance laser melting for a range of materials including plastics, metals, ceramics and sand. Freely configurable sub-components support different hatching patterns such as chess, striped and parallel hatching. Support for very large parts enables cost-effective rapid prototyping.
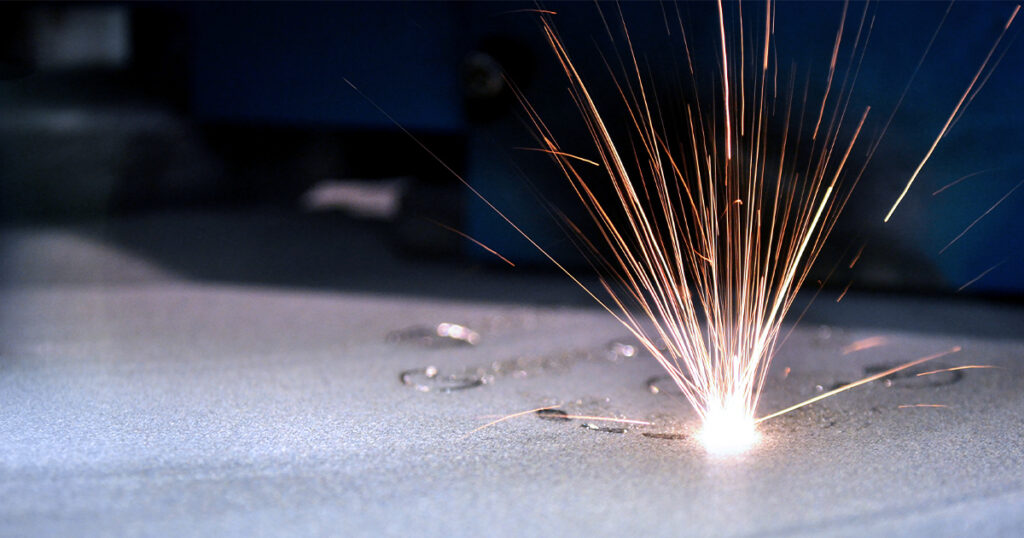
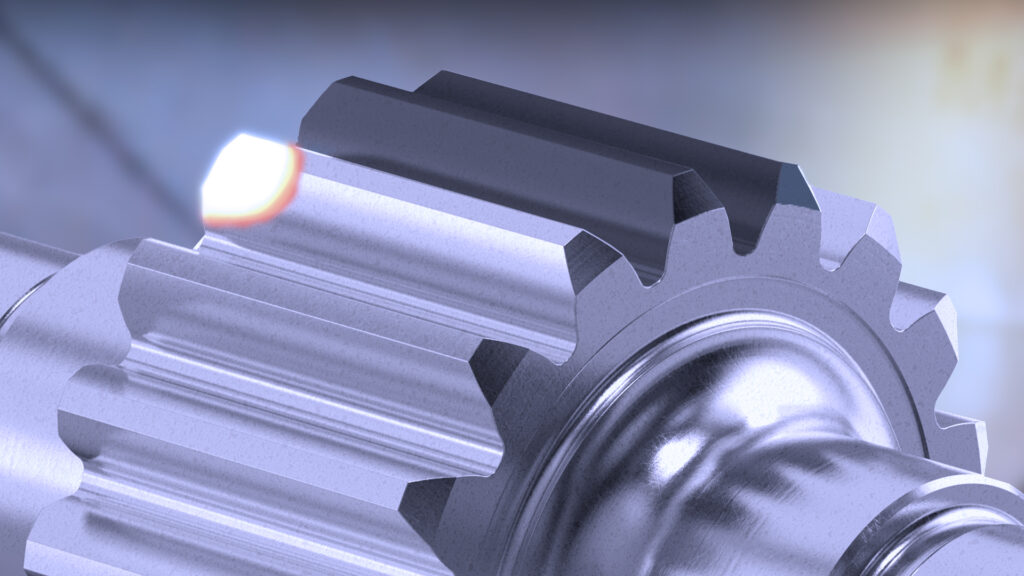
Laser Surface Treatment
ModuleWorks Laser Surface Treatment technology is an advanced surface treatment process. It offers the most advanced features and functionalities, including collision avoidance, reduction of overlaps to prevent duplicate treatment in specific areas, and achieving consistent treatment across all areas. This technology addresses major challenges like manual control, complex part geometries, and collision avoidance by precisely controlling laser parameters, automatic toolpath generation, and collision-free operation. This technology supports Remote Laser Hardening, Laser Coating, and sensor and scanner integrated solutions.
Hammer Peening
ModuleWorks Hammer Peening technology enhances the surface quality of parts through a controlled hammering process. It offers the most advanced features and functionalities such as collision avoidance, reduction of overlaps to prevent duplicate treatment in specific areas, and achieving consistent surface finish across all areas. As a result, this technology ensures that the whole surface is treated accurately, resulting in superior quality and reliability for the produced parts.
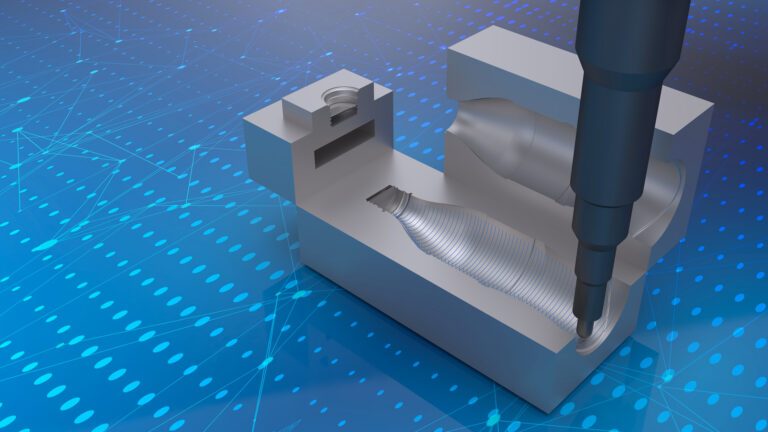
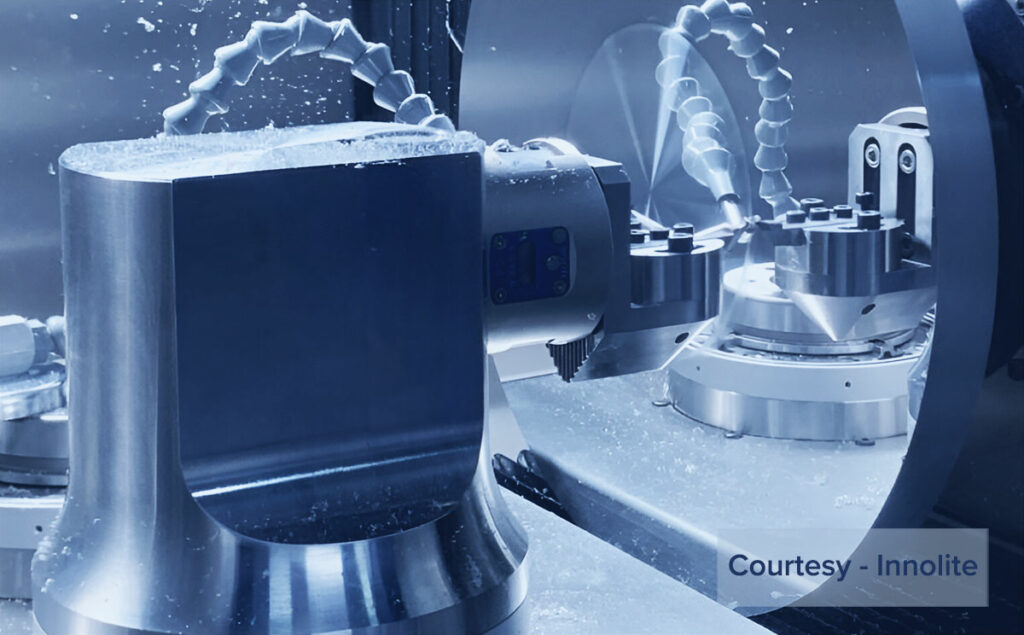
Ultra-Precision Machining
Generic surface-based cycles, high-performance ultra-precision algorithms (UPM) and support for 5+1-axis machining deliver the power and flexibility to manufacture a vast variety of optical parts. These conventional CAM technologies and optics toolpaths can be combined in a single manufacturing process. This enables effective and rapid development of solutions for simplified and cost-efficient grinding, diamond turning and fly cutting applications. The algorithms generate optimized machining patterns based on NURBS geometry, analytical formulas or point clouds.
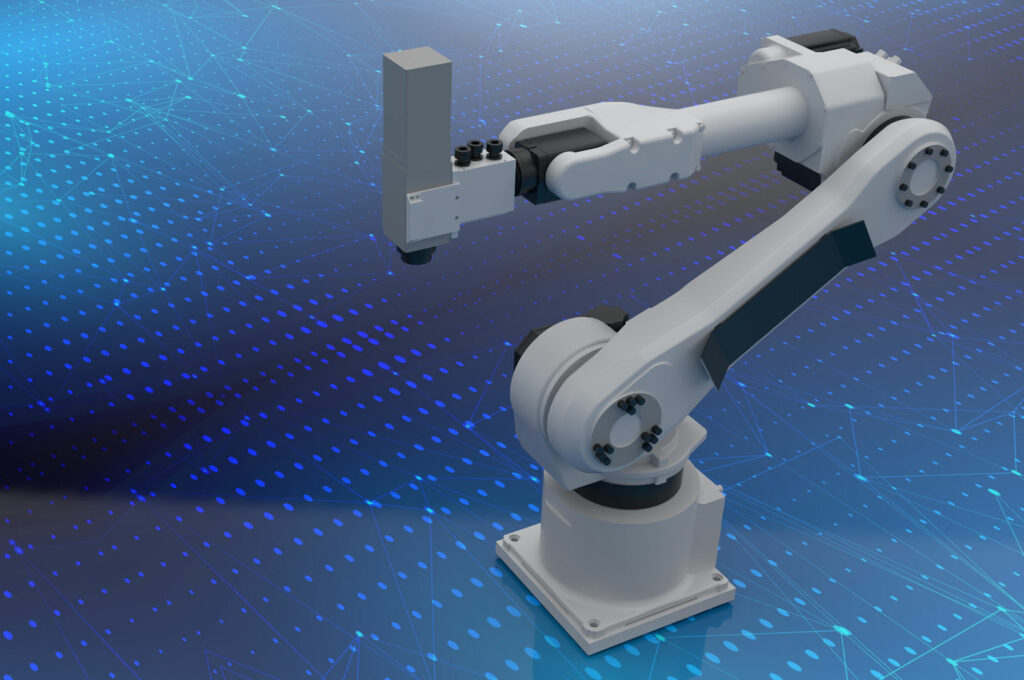
Robotics SDK
The advanced scientific algorithms of the ModuleWorks Robotics SDK optimize the performance and precision of kinematics calculations. Designed for fast and seamless integration, the software library enables rapid development of powerful robotics solutions that transform calculated toolpaths into robot NC-coordinates for automatic offline planning of complex toolpaths.
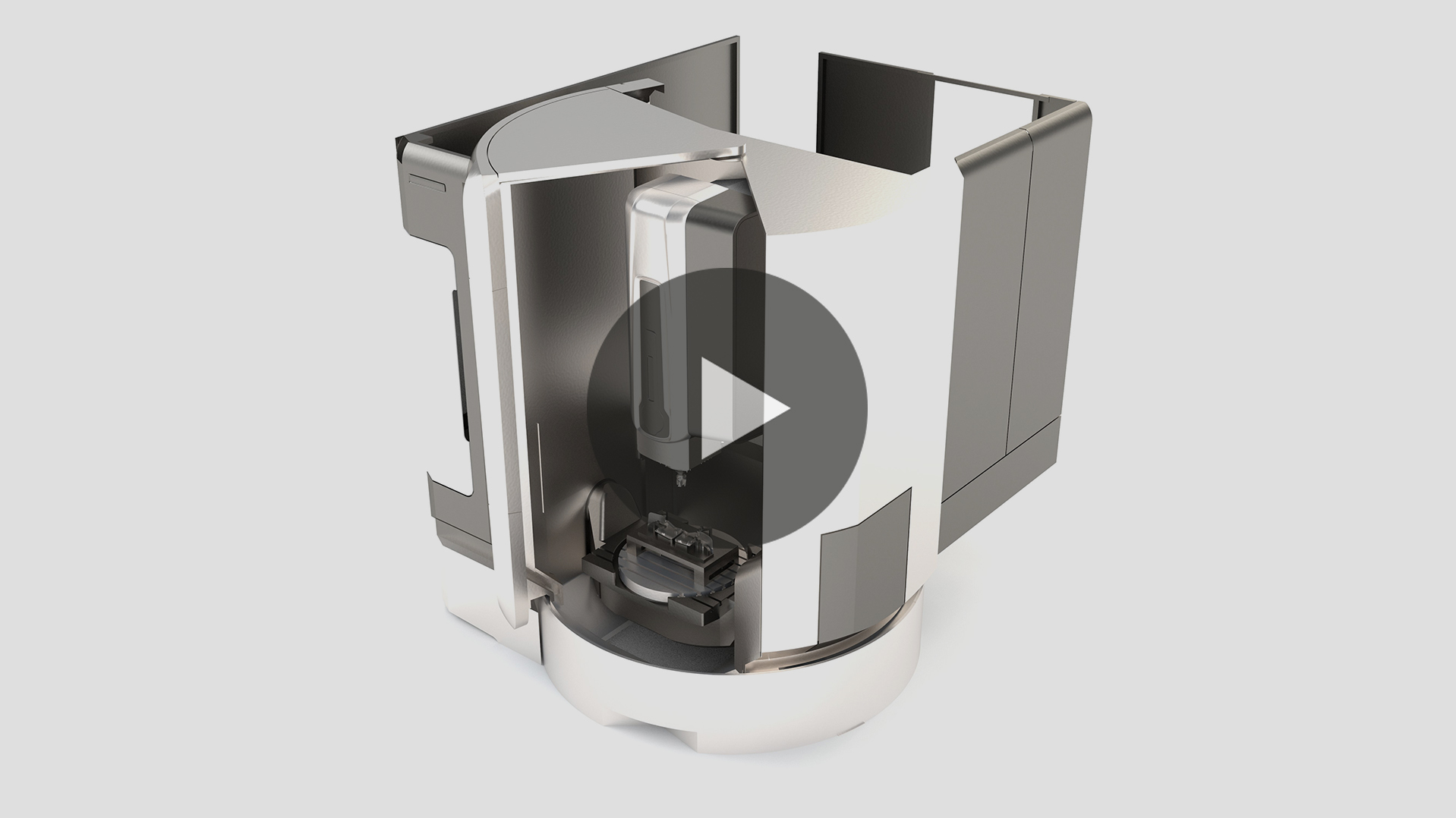
Machine Simulation
ModuleWorks Machine Simulation optimizes profitability and machining safety across the full spectrum of machining operations, from simple jobs to highly complex manufacturing scenarios, including 5-axis and combined mill / turn machining. Flexible kinematic definition, powerful APIs and customization tools enable quick tailoring for specific applications, empowering workflows with high-performance machine simulation and toolpath verification tools.
Simulation on Control
Simulation on Control connects the proven ModuleWorks simulation components directly to the CNC control’s output data or a Digital Twin. It accepts either interpolated axis data or combined motion data in the form of lines and arcs. The system is fully scalable, from a basic verification system to full machine simulation with collision detection.
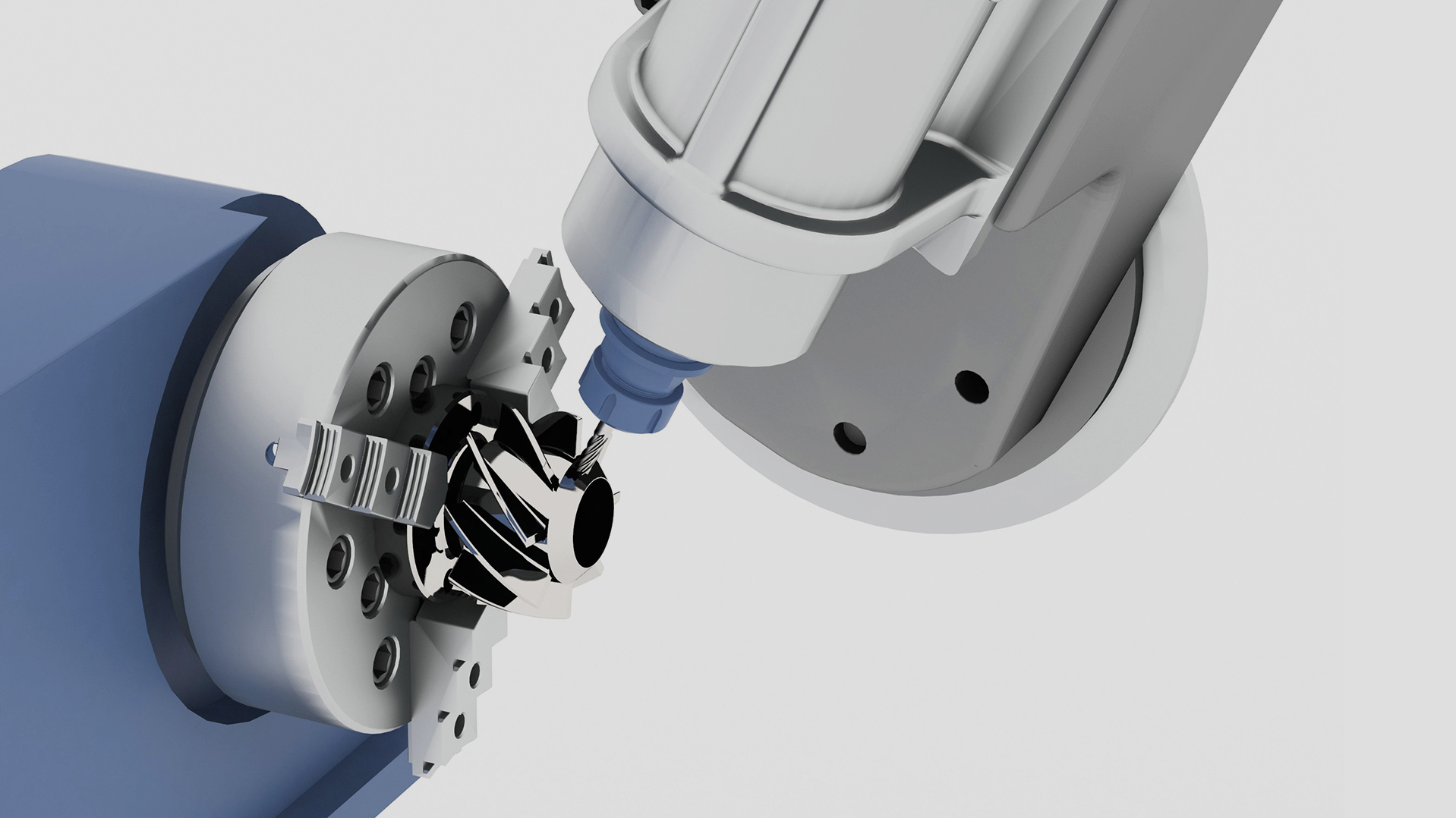
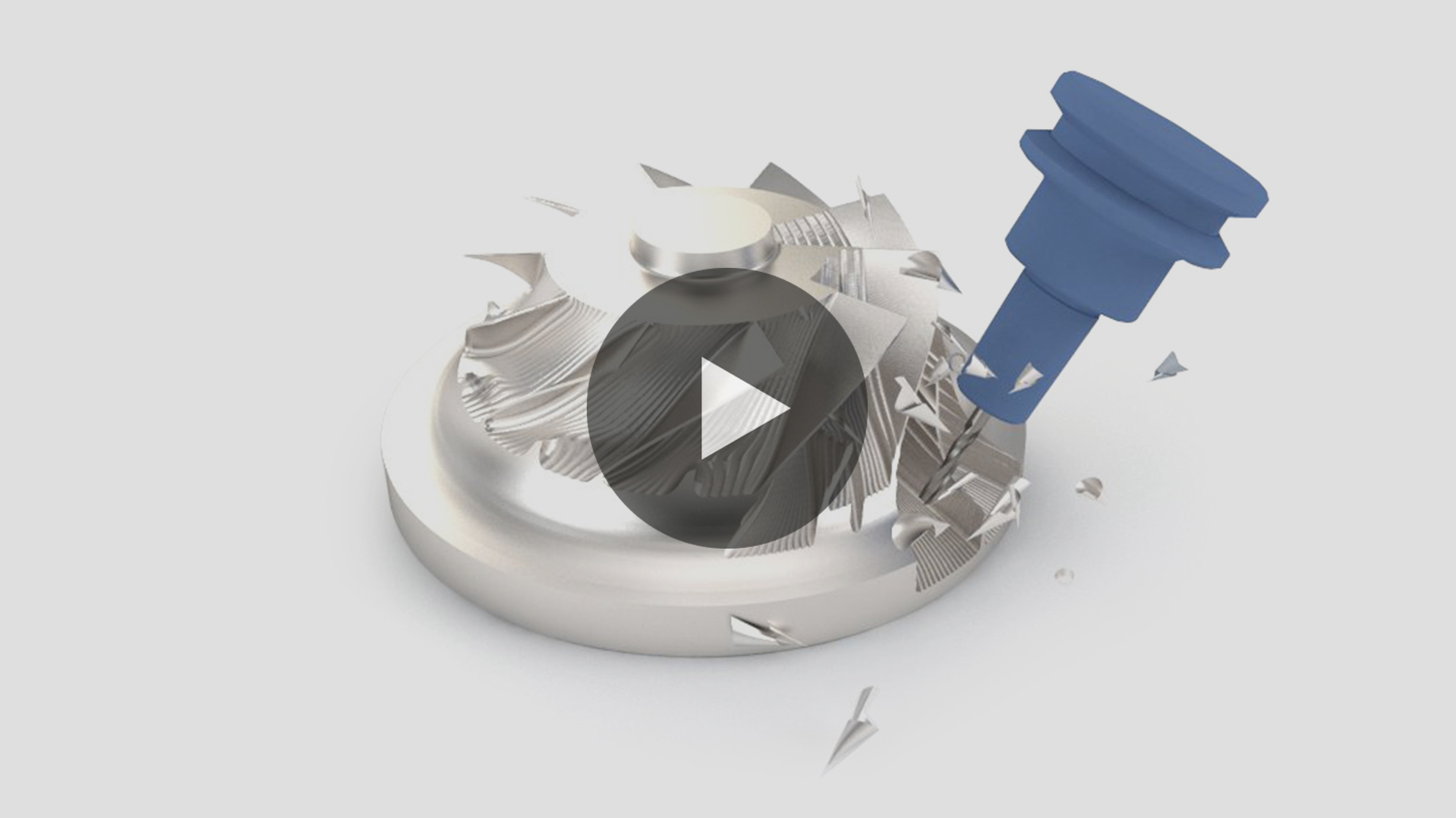
Cutting & Additive Simulation
Add value to applications with high-performance digital verification of stock removal as well as powerful error detection and analysis tools. The adaptive refinement technology delivers a precise definition of the machined component, even on the smallest of features. The built-in animation provides a preview of the machining process.
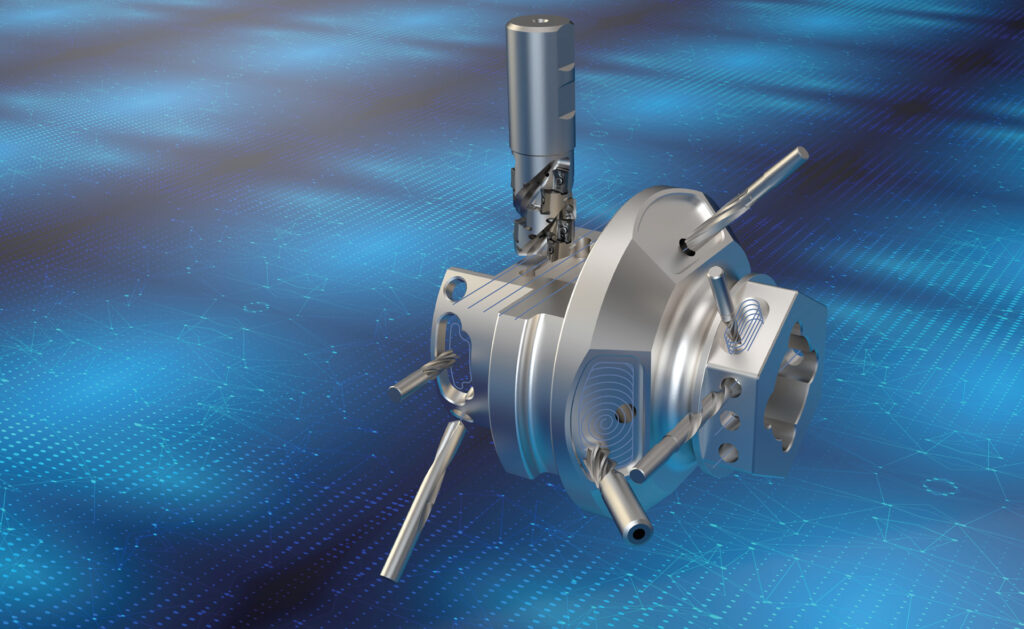
Post-Processor Framework
With ModuleWorks Post-Processor Framework (PPF), users create a custom postscript to generate NC-code from the output of the ModuleWorks kinematic solver or any other source. The versatile PPF runs can run on a network server and on operating systems that support Python. Users can script the NC output for any custom tool and stream it to any machine tool or robot.
Automation Solution
Equipped with process automation intelligence, ModuleWorks Automation Solution enables engineers and machine operators to dramatically speed up programming. Automatic manufacturing without any user interaction is supported through a headless mode. The toolpath is calculated from imported geometries to automatically setup efficient consecutive operations and keep production moving.

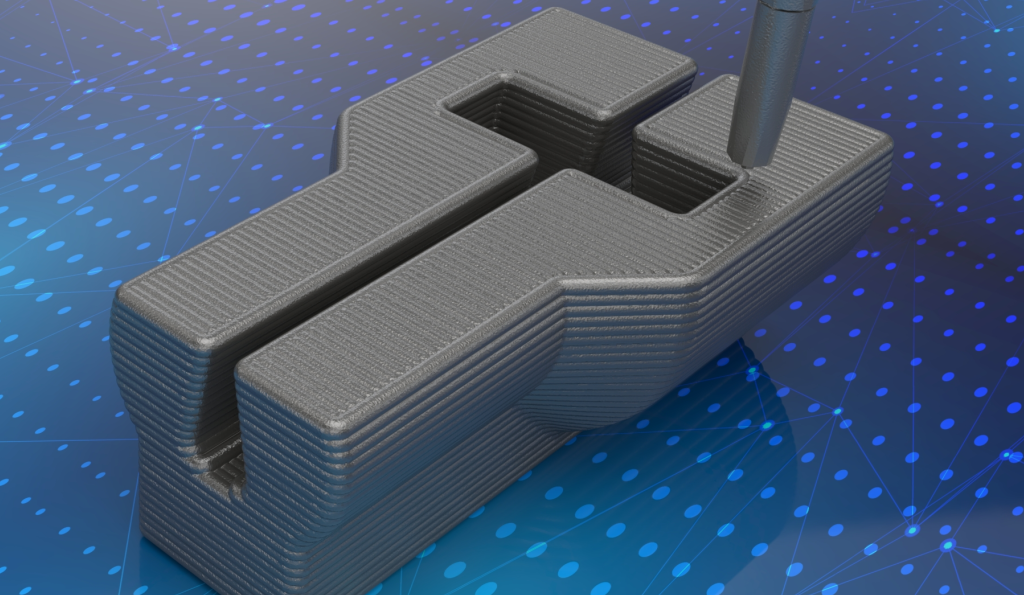
Wire Arc Additive Manufacturing
ModuleWorks Wire Arc Additive Manufacturing (WAAM) incorporates a toolpath planning algorithm specially designed for complex geometries and customized structures. The algorithm optimizes the manufacturing of near net shape geometries for different welding processes. Process parameters such as welding speed, current, voltage, wire feed, or powder speed can be defined to achieve a specific wall width/height (multi-layer) with maximum deposition efficiency.
Direct Energy Deposition
ModuleWorks Direct Energy Deposition (DED) incorporates a toolpath planning algorithm specially designed for complex geometries and customized structures. Process-critical parameters for the part can be accurately controlled and adapted to achieve a specific wall width/height (multi-layer) with maximum deposition efficiency, resulting in near net shapes that requires minimum post-processing.
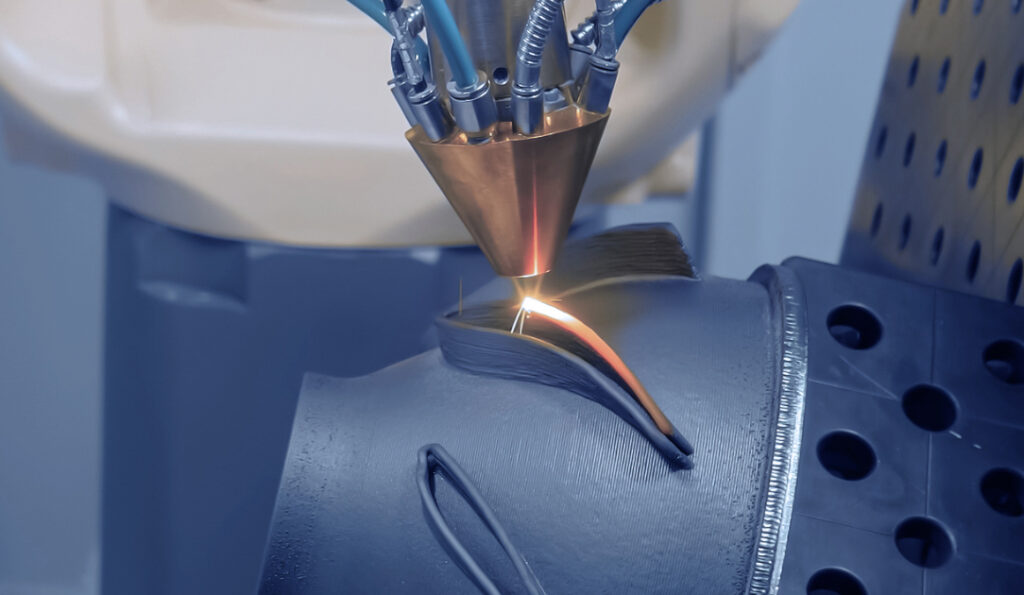
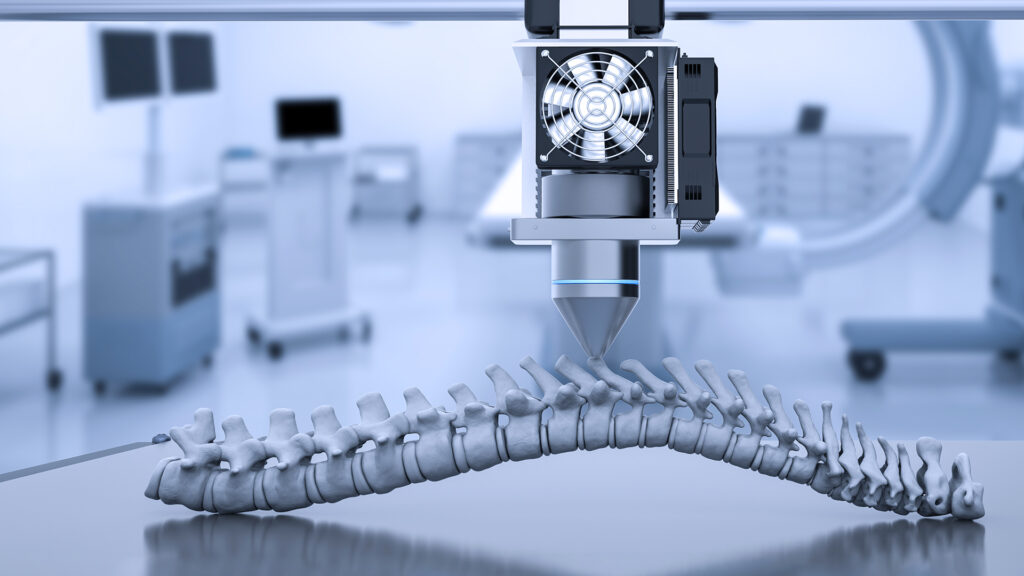
Polymer Printing
The Polymer Printing calculation core supports a wide range of applications, from desktop Fused Filament Fabrications (FFF) to Big Area Additive Manufacturing (BAAM) carbon-based component production or concrete printing.
This makes it easier to master complex challenges in these demanding environments and provides the flexibility to calculate toolpaths for complex freeform geometries and freely configure sub-components, such as print patterns in the infill and support areas.
Powder Bed Fusion
The ModuleWorks Powder Bed Fusion (PBF) software library enables quick and easy development of advanced, all-encompassing PBF solutions. It delivers high-performance laser melting for a range of materials including plastics, metals, ceramics and sand. Freely configurable sub-components support different hatching patterns such as chess, striped and parallel hatching. Support for very large parts enables cost-effective rapid prototyping.
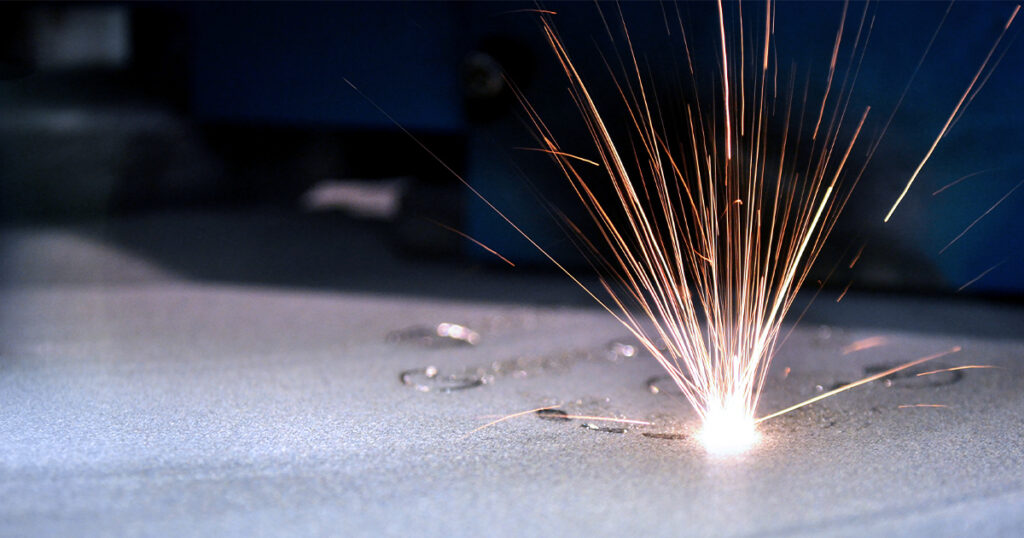
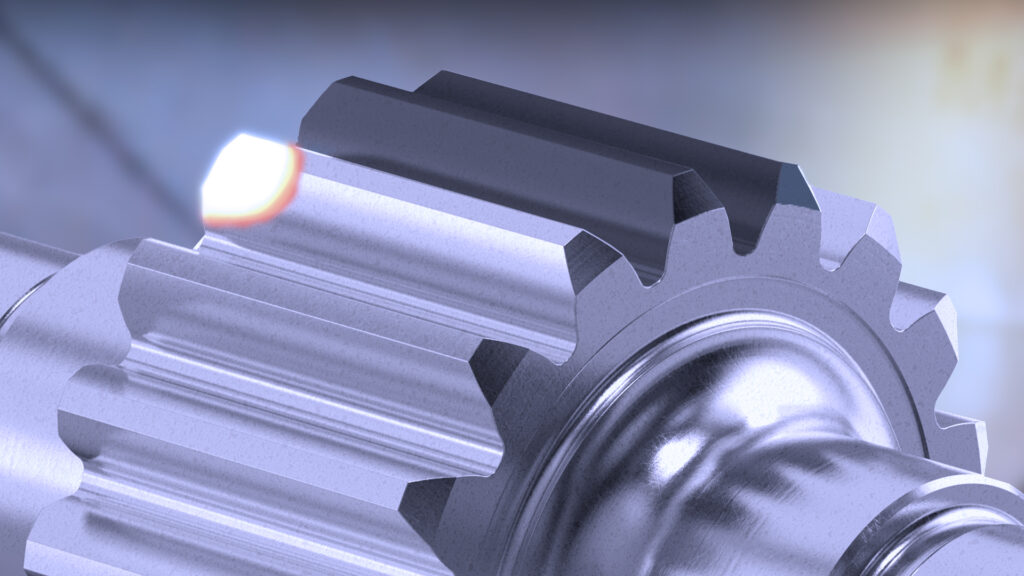
Laser Surface Treatment
ModuleWorks Laser Surface Treatment technology is an advanced surface treatment process. It offers the most advanced features and functionalities, including collision avoidance, reduction of overlaps to prevent duplicate treatment in specific areas, and achieving consistent treatment across all areas. This technology addresses major challenges like manual control, complex part geometries, and collision avoidance by precisely controlling laser parameters, automatic toolpath generation, and collision-free operation. This technology supports Remote Laser Hardening, Laser Coating, and sensor and scanner integrated solutions.
Hammer Peening
ModuleWorks Hammer Peening technology enhances the surface quality of parts through a controlled hammering process. It offers the most advanced features and functionalities such as collision avoidance, reduction of overlaps to prevent duplicate treatment in specific areas, and achieving consistent surface finish across all areas. As a result, this technology ensures that the whole surface is treated accurately, resulting in superior quality and reliability for the produced parts.
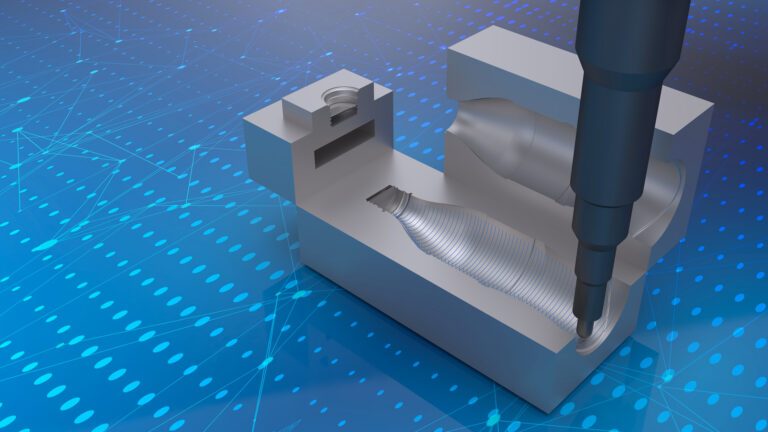
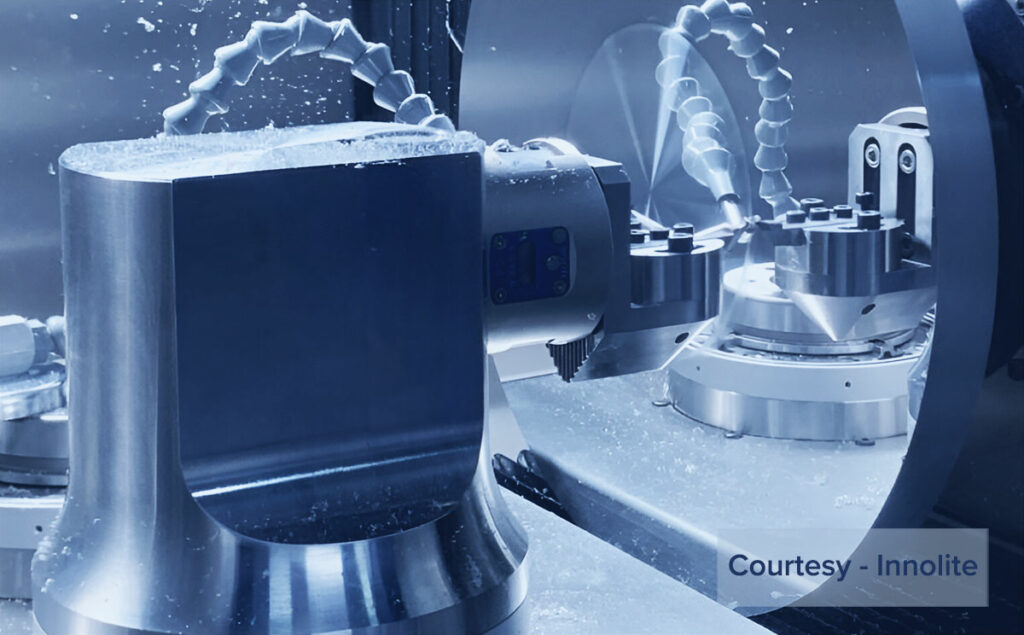
Ultra-Precision Machining
Generic surface-based cycles, high-performance ultra-precision algorithms (UPM) and support for 5+1-axis machining deliver the power and flexibility to manufacture a vast variety of optical parts. These conventional CAM technologies and optics toolpaths can be combined in a single manufacturing process. This enables effective and rapid development of solutions for simplified and cost-efficient grinding, diamond turning and fly cutting applications. The algorithms generate optimized machining patterns based on NURBS geometry, analytical formulas or point clouds.
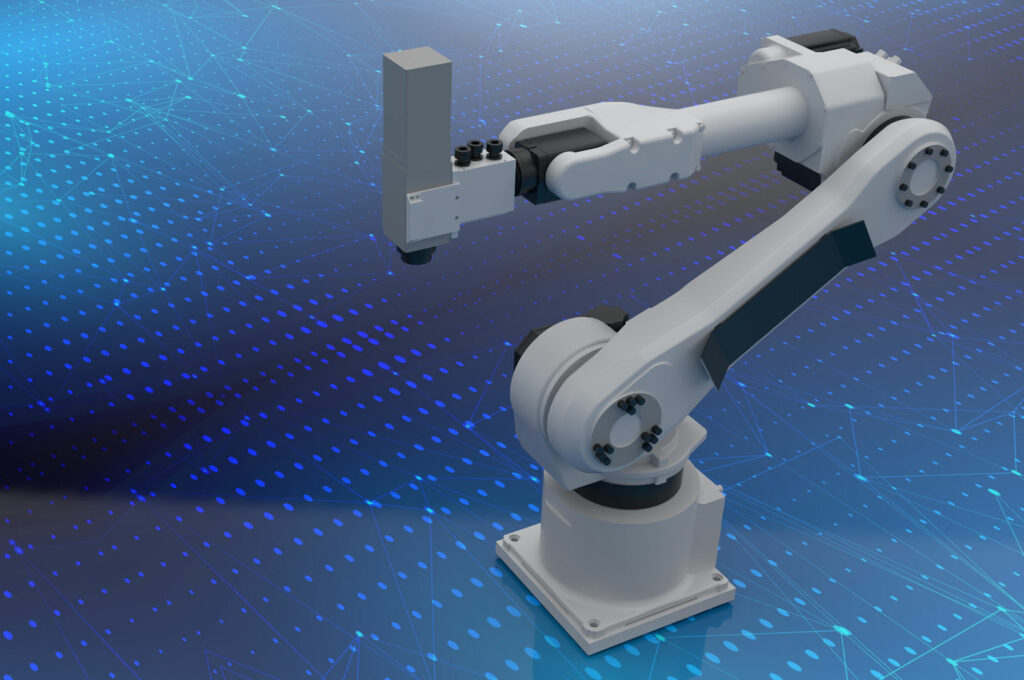
Robotics SDK
The advanced scientific algorithms of the ModuleWorks Robotics SDK optimize the performance and precision of kinematics calculations. Designed for fast and seamless integration, the software library enables rapid development of powerful robotics solutions that transform calculated toolpaths into robot NC-coordinates for automatic offline planning of complex toolpaths.
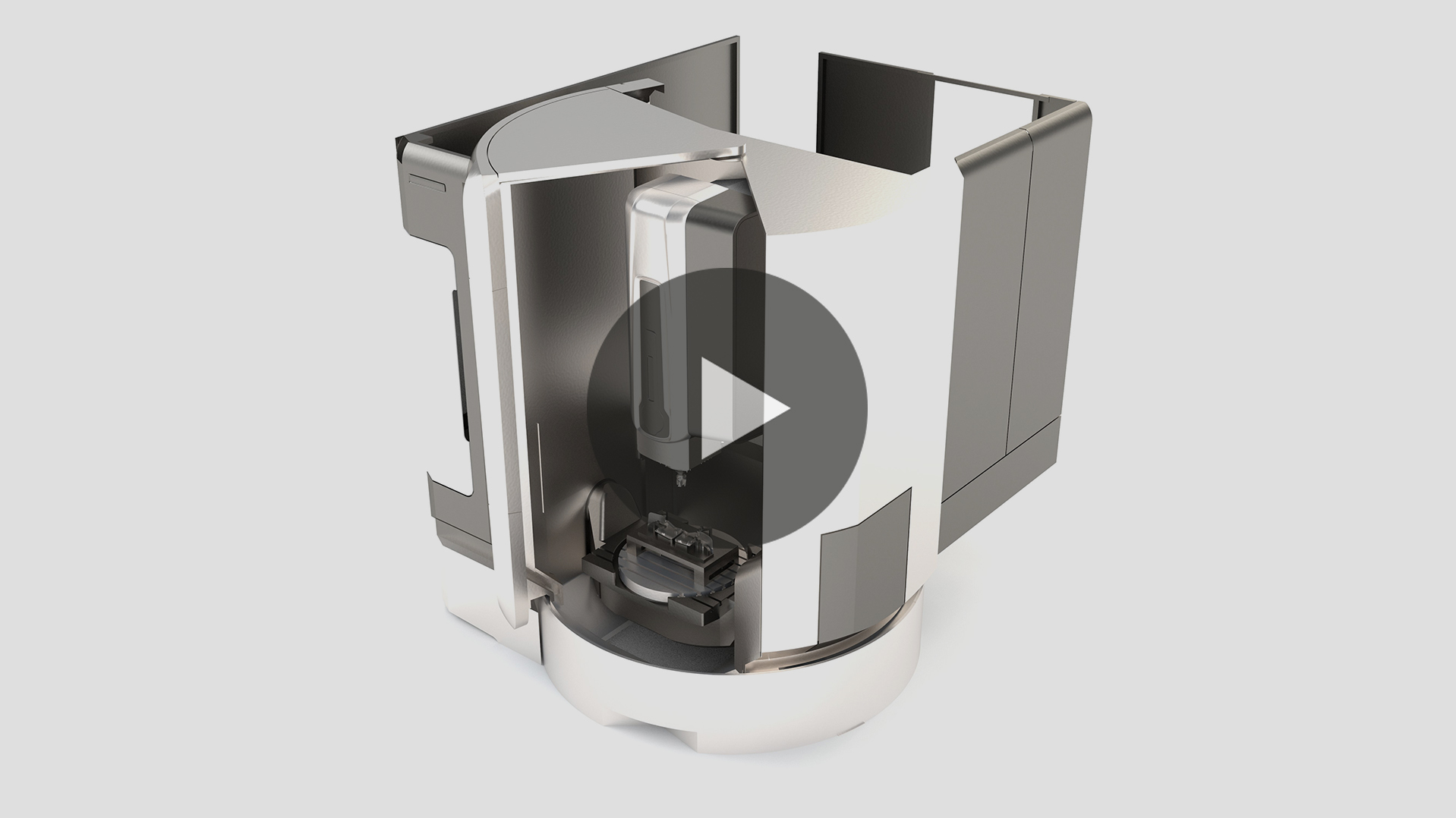
Machine Simulation
ModuleWorks Machine Simulation optimizes profitability and machining safety across the full spectrum of machining operations, from simple jobs to highly complex manufacturing scenarios, including 5-axis and combined mill / turn machining. Flexible kinematic definition, powerful APIs and customization tools enable quick tailoring for specific applications, empowering workflows with high-performance machine simulation and toolpath verification tools.
Simulation on Control
Simulation on Control connects the proven ModuleWorks simulation components directly to the CNC control’s output data or a Digital Twin. It accepts either interpolated axis data or combined motion data in the form of lines and arcs. The system is fully scalable, from a basic verification system to full machine simulation with collision detection.
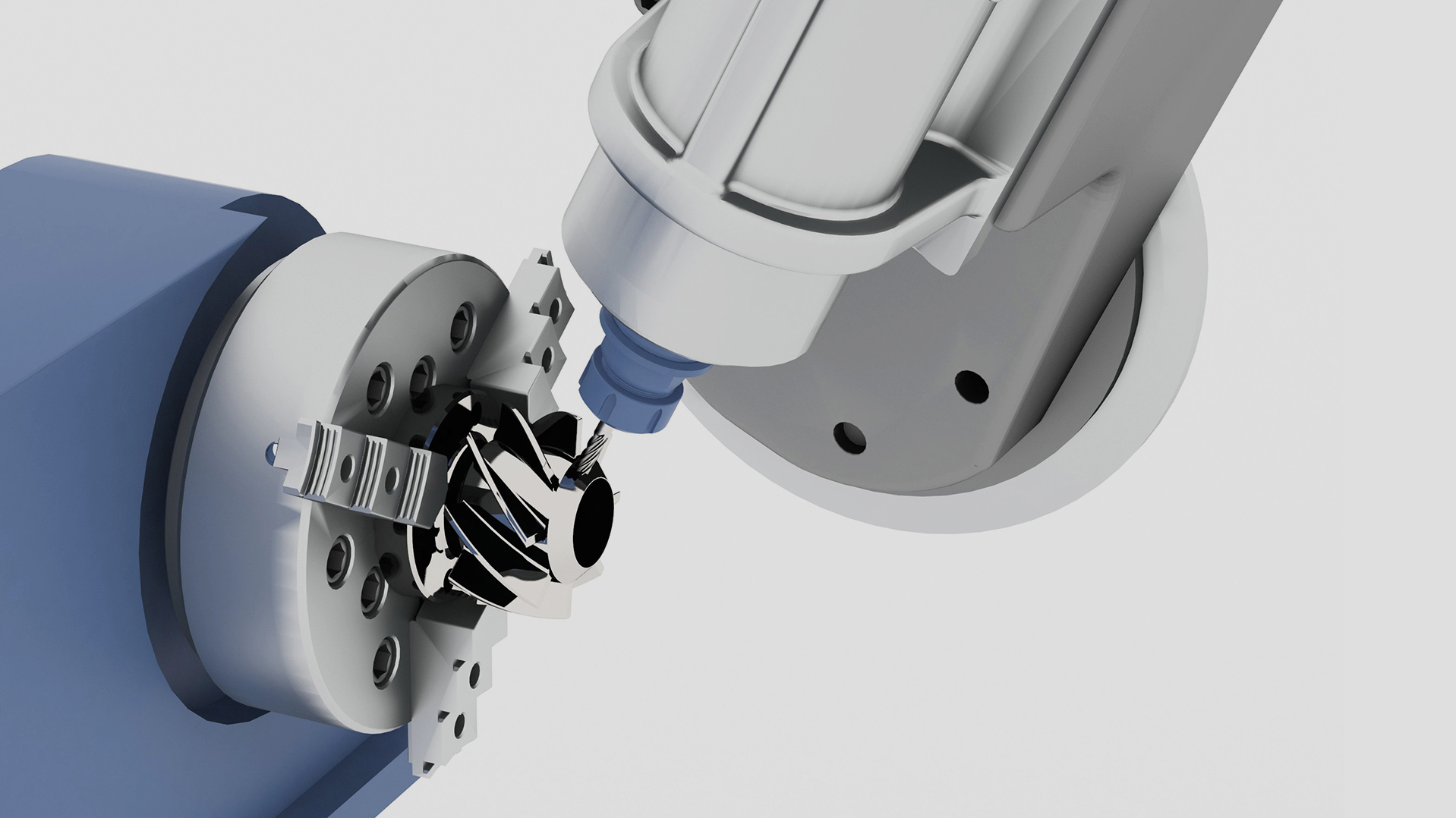
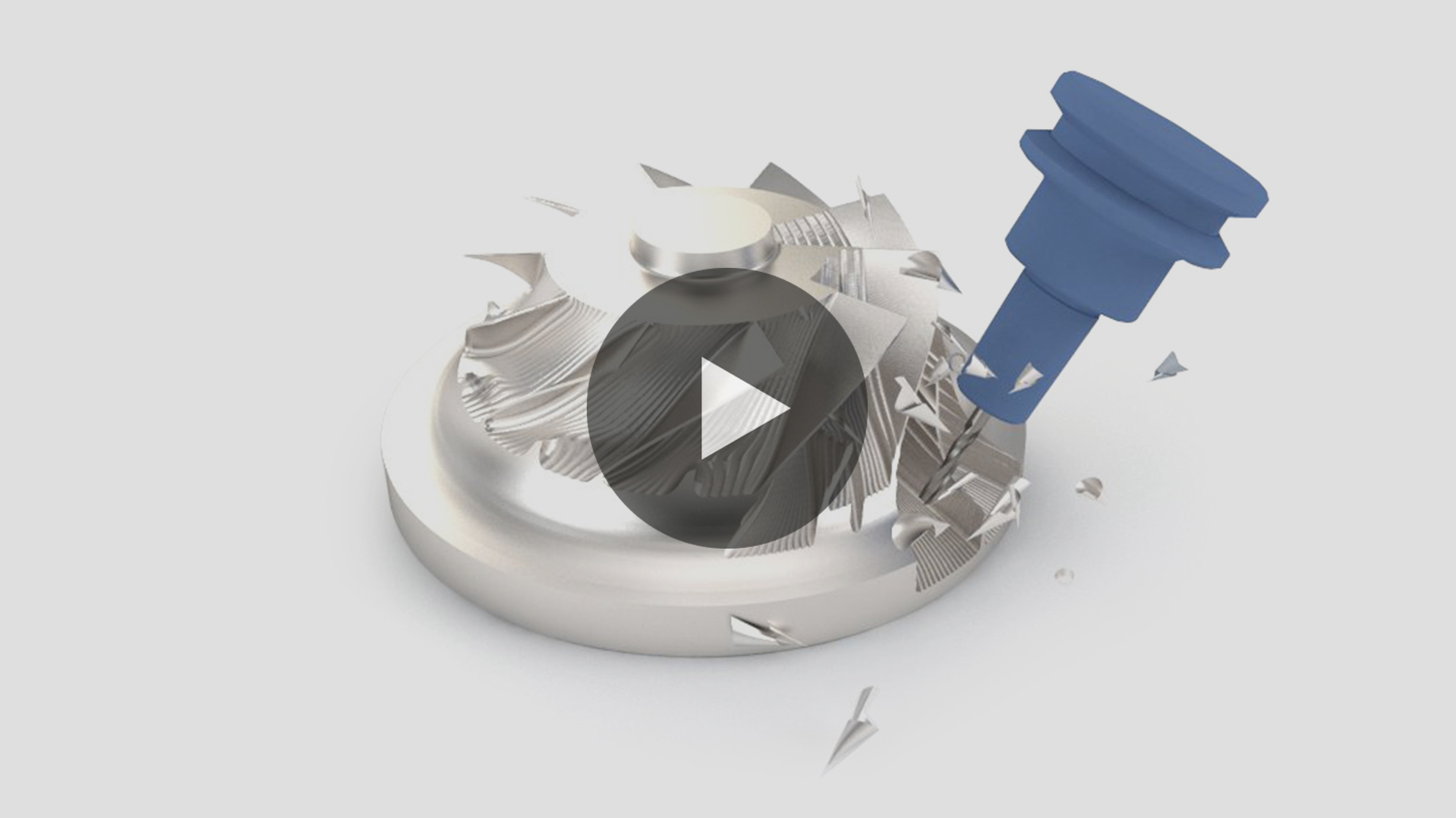
Cutting & Additive Simulation
Add value to applications with high-performance digital verification of stock removal as well as powerful error detection and analysis tools. The adaptive refinement technology delivers a precise definition of the machined component, even on the smallest of features. The built-in animation provides a preview of the machining process.
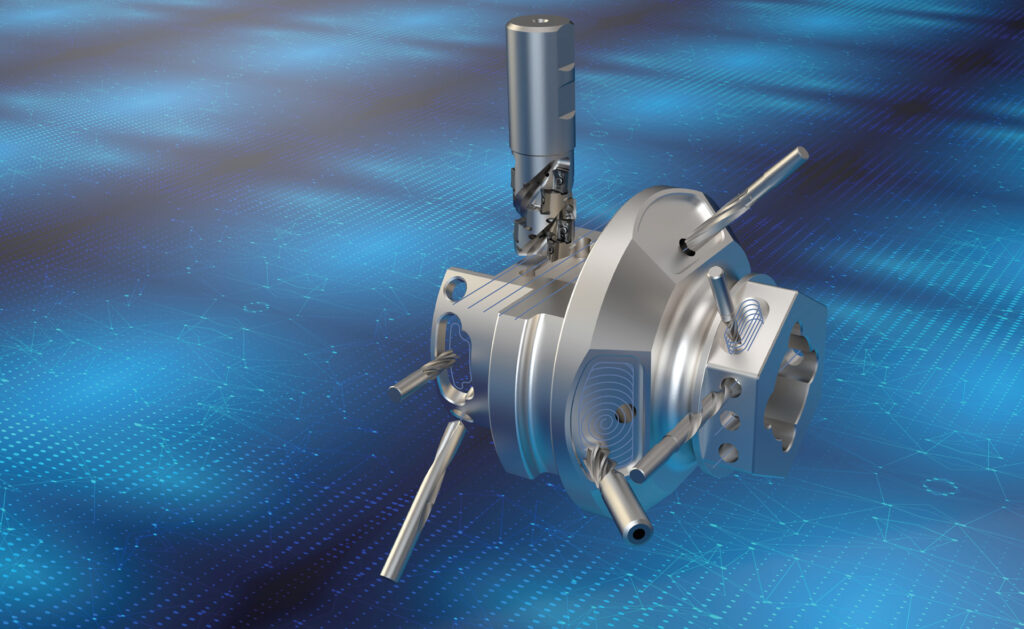
Post-Processor Framework
With ModuleWorks Post-Processor Framework (PPF), users create a custom postscript to generate NC-code from the output of the ModuleWorks kinematic solver or any other source. The versatile PPF runs can run on a network server and on operating systems that support Python. Users can script the NC output for any custom tool and stream it to any machine tool or robot.
Automation Solution
Equipped with process automation intelligence, ModuleWorks Automation Solution enables engineers and machine operators to dramatically speed up programming. Automatic manufacturing without any user interaction is supported through a headless mode. The toolpath is calculated from imported geometries to automatically setup efficient consecutive operations and keep production moving.

Additive & Process Technologies in Numbers
Your Partner for Success and Innovation
We believe in building long-term partnerships with our clients, working together to achieve shared goals and drive innovation.
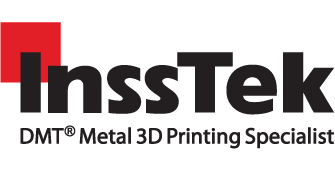
We believe in building long-term partnerships with our clients, working together to achieve shared goals and drive innovation.
Dongmin Shin
Director I AM Technical Sales Division
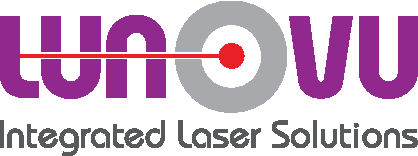
In cooperation with ModuleWorks we managed to realize innovative methods for path and process planning for additive manufacturing by use of laser, powder and wire. We therefore completed the digital process chain for our machines and applications.
Oliver Steffens
Managing Director
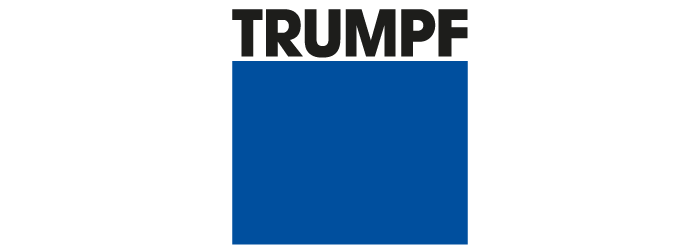
With the new software, we can offer our customers a customised solution for operating our TruPrint 3D printers. We greatly simplify the whole process for our customers, from initial idea to the real component, and thereby increase the overall attractiveness of additive technologies. With ModuleWorks, we’ve gained an experienced partner in digital manufacturing for collaboration and product development.
René Kreissl
Head of Additive Manufacturing Unit
Our Experts in Additive & Process Technologies
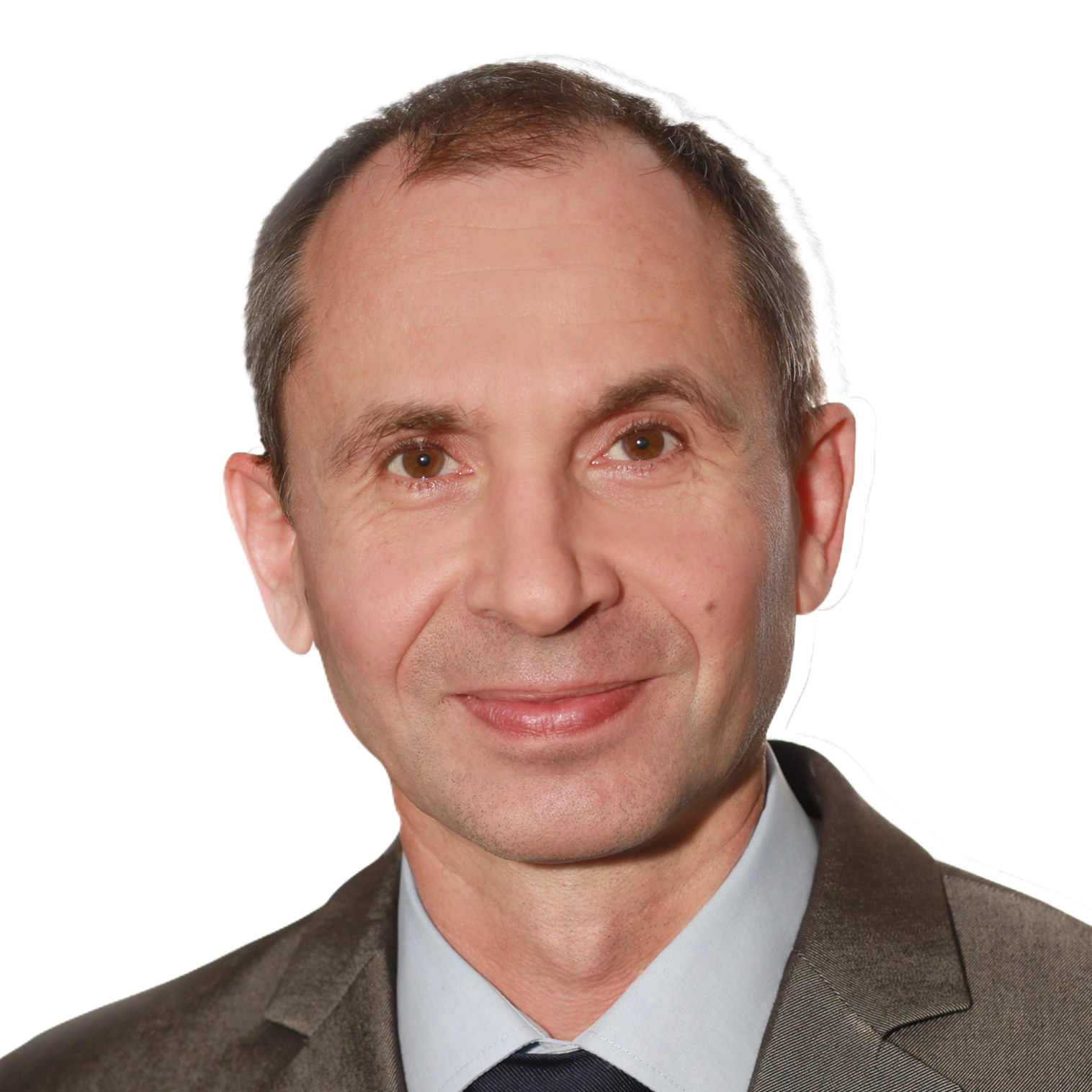
Lothar Glasmacher
Head of Additive & Process Technologies
Project Director
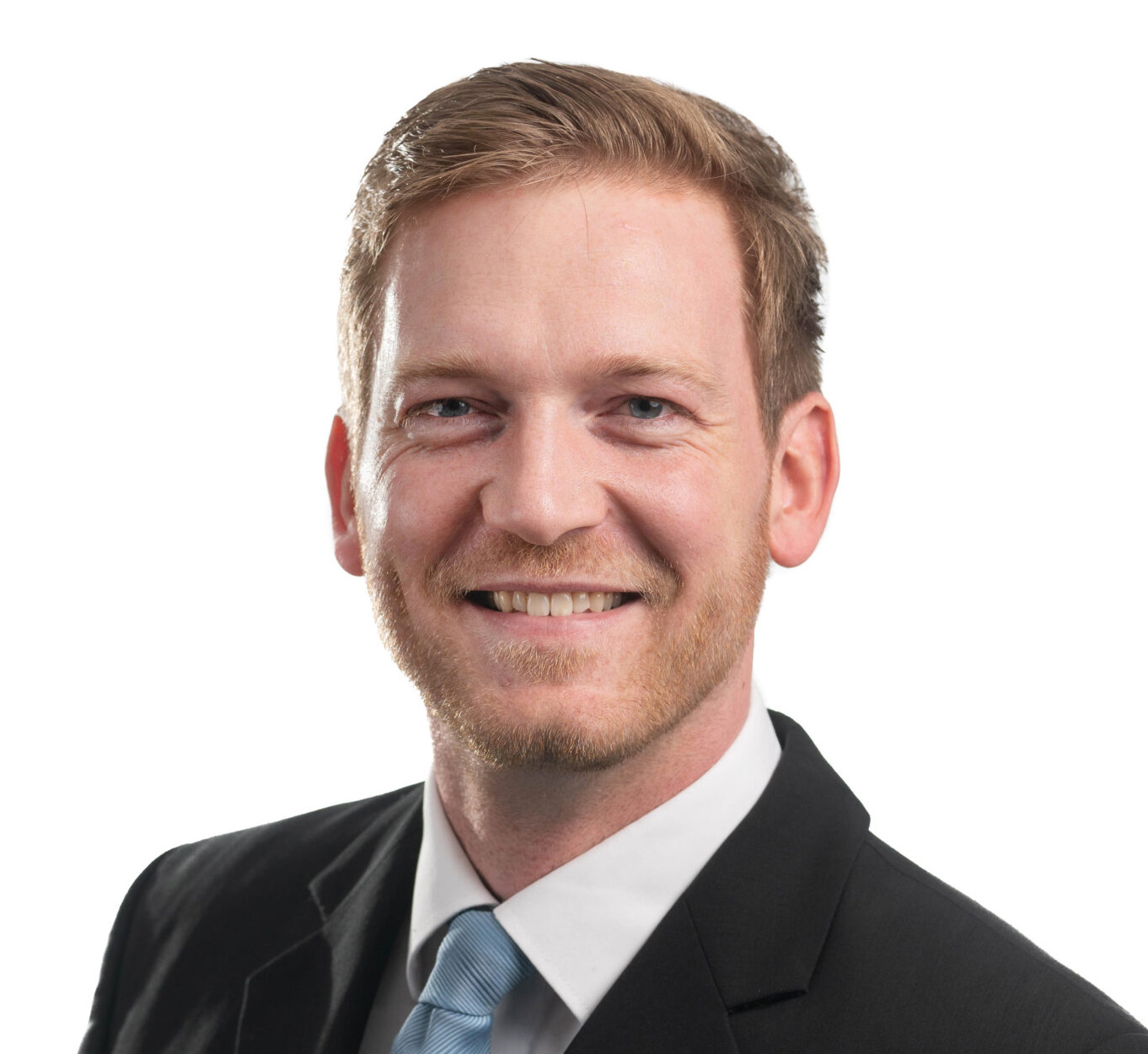